Test Systems
What are Test Systems and Why Does it Matter?
Test systems are equipment, setups, or environments that validate the quality and functionality of diverse products and processes. Including applications like semiconductor thermal forcing systems and medical imaging or diagnostics, these systems identify or resolve challenges and issues at an early stage. Test systems help ensure product accuracy, reliability, safety, and performance in manufacturing. Early detection through medical testing expands potential treatment windows to increase the possibility of positive patient outcomes.
Why Boyd for Test Systems Solutions?
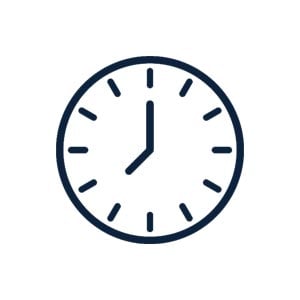
Enable faster and more accessible diagnosis and treatment decisions.
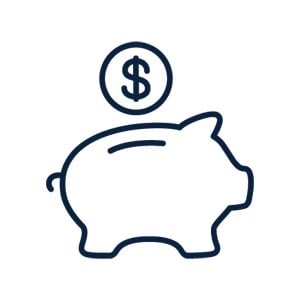
Maximize material yield and minimize waste with efficient manufacturing techniques.
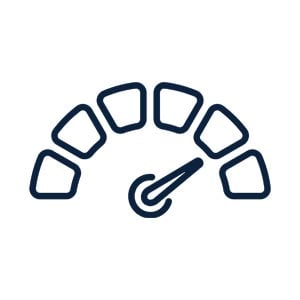
Iterate complex samples quickly to reduce design cycle time.
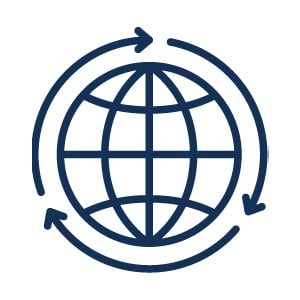
Material science innovation and global agility balance best total cost management, performance, and supply continuity.
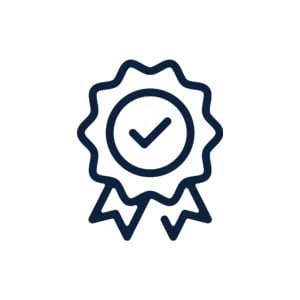
Streamlined product design is optimized for manufacturability, reliability, automation, innovative performance, and minimized carbon footprint.
Test System Examples
The semiconductor industry utilizes burn-in test sockets and thermal forcing systems to ensure the quality, reliability, and functionality of integrated circuits (ICs), semiconductor components, and innovative R&D. Burn-in testing, test sockets, and thermal forcing systems improve quality control, optimize semiconductor performance, minimize field failures, and improves IC innovation and accuracy.
Medical test systems like X-ray imaging systems, computed tomography (CT) scanners, magnetic resonance imaging (MRI), and ultrasound imaging systems enable healthcare professionals to visualize internal structures, detect diseases, and gather valuable diagnostic information essential for effective patient care. The medical industry also relies heavily on polymerase chain reaction (PCR) testing for rapid point-of-care diagnostics and testing.
The Boyd Difference for Test Systems
Semiconductor Burn-In Test Sockets
Enhance semiconductor reliability and testing efficiency with Boyd’s advanced burn-in sockets. Our sockets are meticulously engineered to minimize damage to solder balls, utilizing the lowest actuation force possible. Meet your technical requirements and maximize board density with innovative contact technology in both platform sockets and fully custom designs with the most compact socket footprint.
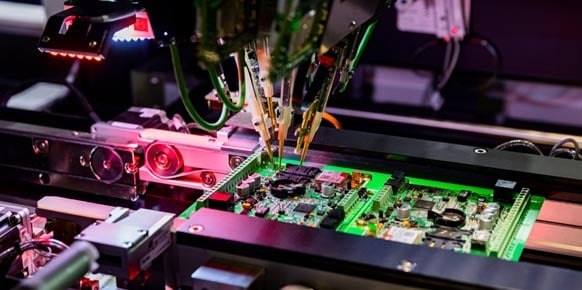
Semiconductor Test Thermal Forcing Systems
Boyd’s liquid-free thermal systems leverage innovative phase change technologies to enable an extensive temperature forcing range spanning -55°C to 250°C, tailored specifically for semiconductor testing deployed at multiple stages within the manufacturing cycle. Our thermal forcing systems, characterized by their compact design, seamlessly integrate into your setup enabling quieter, portable test solutions with fast stabilization, superior power handling, and precision control.
Innovative Cooling Solutions for Imaging Systems
Complex medical imaging systems such as X-rays, MRIs, CT scanners, and ultrasound equipment generate immense heat and must be cooled for consistent system operation and reliability. Improve imaging system speed and accuracy while reducing energy consumption with Boyd’s innovative cooling solutions. Our lightweight, low profile, rugged liquid cooling systems, cold plates, heat exchangers, and high-efficiency encapsulated spreaders enable smaller, quieter, lighter imaging thermal systems for better performance in a compact format capable of withstanding exceptional gravitation force.
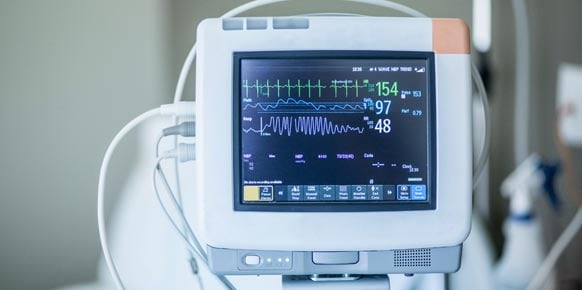
Enhance Imaging Technology Experience with Display Innovation
Unlock marketable differentiation through Boyd’s display and Human-Machine Interface (HMI) experience. Our innovative display solutions are optimized to thrive in diverse environments with varying light levels and sources, create optimal visibility and readability, and withstand the rigors of repeat sanitation processes, ensuring both quality and hygiene. Enhance imaging tech experience with Boyd display solutions.
Medical Device Interfaces, Housing, and Finishing
Boyd’s broad portfolio of switches, touch screen interfaces, and decorative molded plastic enclosures enables high quality, custom printed membrane switch technology, comprehensive front panel display integration and bonding solutions, or durable graphic overlay and labels for long-lasting, easy-to-clean user interfaces.
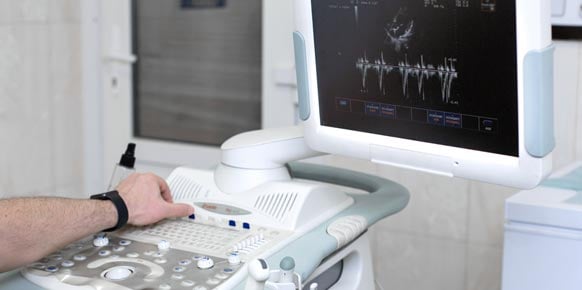
In-Vitro Diagnostics Innovation: Faster and Affordable Diagnostics
In-Vitro Diagnostics (IVD) Equipment, polymerase chain reaction (PCR), microfluidics, and diagnostic and laboratory disposables accompanying these devices increase the speed and convenience with which medical providers diagnose and treat patients. In-Vitro Diagnostics (IVD) innovation enables faster, more accessible, and affordable diagnosis and treatment decisions.
In-Vitro Diagnostics Innovation: Enhance Testing Accuracy
Enhance testing accuracy by precisely controlling operating temperature during IVD laboratory equipment operation and managing sample stability with high reliability, high-performance cold plates and liquid cooling systems or with precision medical laminates enabling highly accurate fluid flow protected from contaminants.
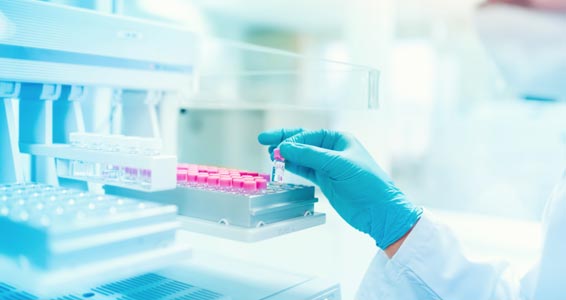

Microfluidic Quality Control: Leverage Boyd Clean Rooms and Process Control
Boyd’s exceptional precision converting capabilities available in clean rooms certified from 100 to 100k, and medical material science expertise enables our medical engineers to design and fabricate PCR Plate Seals and Microfluidic Diagnostic Laminates as a fully outsourced and packaged medical solution.
Medical Manufacturing: High Quality as the Standard
Boyd’s ISO 13485 quality management system certification ensures reliable performance, cleanliness, and patient safety with medical components manufactured in a controlled environment that adhere to strict regulatory compliance, thorough documentation, inspection, and traceability processes. Our medical facilities feature strict process control, constant quality assessment, and clean room environments to exceed regulatory and design specifications through each step of our product’s life cycle from sourcing, fabrication, assembly, kitting, and sterilization.
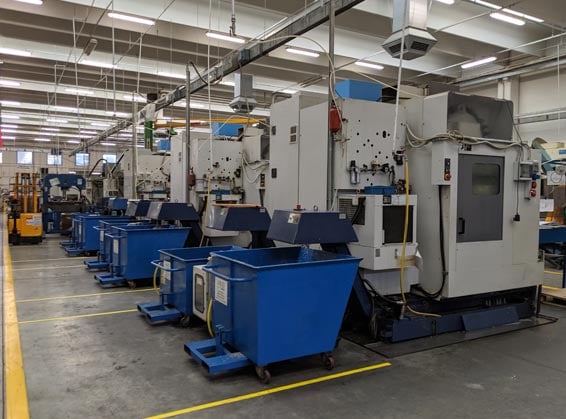
Benefits of Test Systems
Ensure the quality and reliability of products by identifying defects, errors, or malfunctions early in the manufacturing process to prevent faulty items from reaching customers.
Improve product performance by evaluating under various conditions to ensure they meet design specifications and user expectations.
Enhance accuracy with consistent and repeatable test procedures to ensure reliable results across different testing cycles.
Accelerate the product development cycle and speed up time to market with early issue detection and faster validation through test systems.
Mitigate risks associated with product failures bu ensuring that products are safe for users and compliant with regulations.
Enable targeted testing of unique features or functionalities with test systems customized to specific requirements.
Test systems help ensure products meet industry standards, regulations, and certifications, minimizing legal and compliance risks.
Enable predictive maintenance by monitoring the performance of equipment and identifying potential issues before causing downtime.
Test Systems Challenges
Complexity and Integration: Test systems often involve multiple components, instruments, software, and interfaces that need to be integrated leading to compatibility issues and requiring specialized knowledge for setup and maintenance.
Customization Challenges: Customizing test systems to specific product requirements requires extensive modifications, leading to delays and increased costs.
Testing Variability: Variability in test results arises from factors like operator errors, equipment inconsistencies, and environmental conditions.
Maintenance and Calibration: Regular maintenance, calibration, and validation of test equipment are essential for accurate results.
Scalability: As product volumes increase, designing systems that handle high volumes without sacrificing accuracy or speed can be challenging.
Data Management and Analysis: Managing and analyzing large volumes of data generated by test systems requires efficient data storage, processing, and interpretation.
Closing
500K+ liquid cold plates installed in the field with zero leaks for safe direct liquid cooling interfaces
30 billion + field hours with zero leaks in liquid cooling systems to reliably maximize performance
60+ years of field-proven performance and over 1 billion units shipped in transportation, aerospace, and defense applications for trusted reliability in markets where safety is a key concern
20+ years of thermal design expertise and robust, proprietary modeling tools to iterate designs quickly and accelerate speed to market
Have questions? We’re ready to help!