Burn-In and Test Sockets
Semiconductor burn-in and test sockets are essential to test and validate all types of integrated circuits (ICs) including processors and microchips. Sockets serve as a critical interface between the semiconductor device and testing equipment, enabling precise testing and validation with efficiency and cost-effectiveness in semiconductor manufacturing processes.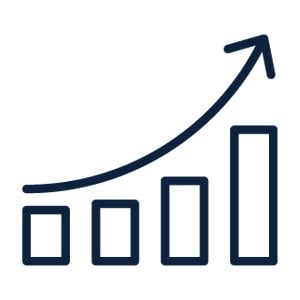
Accelerate Time to Market
Boyd’s decades of semiconductor socket design expertise and robust proprietary modeling tools enable us to swiftly iterate designs and expedite time to market.
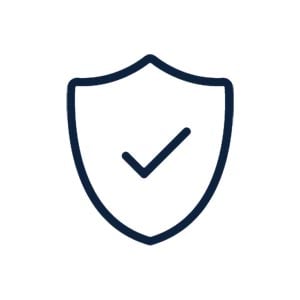
Enhance Chip Test Handling
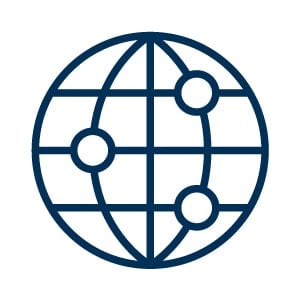
Global Reach, Local Support
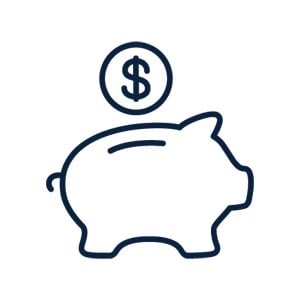
Lower Total Cost of Ownership
Integrated solutions minimize or eliminate waste, maintenance expenses, and downtime.
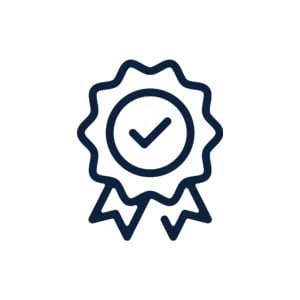
Reduce Warranty Claims
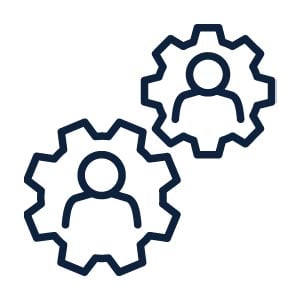
After Market Service
Total Semiconductor Development Support with Sockets
Semiconductor sockets support chip architects and manufacturers throughout the entire development and fabrication process. From initial design verification, to test batches and full-scale production, semiconductor sockets validate performance and identify early failures. Sockets are an extremely customizable component that semiconductor manufacturers leverage to accelerate chip testing and improve reliability.
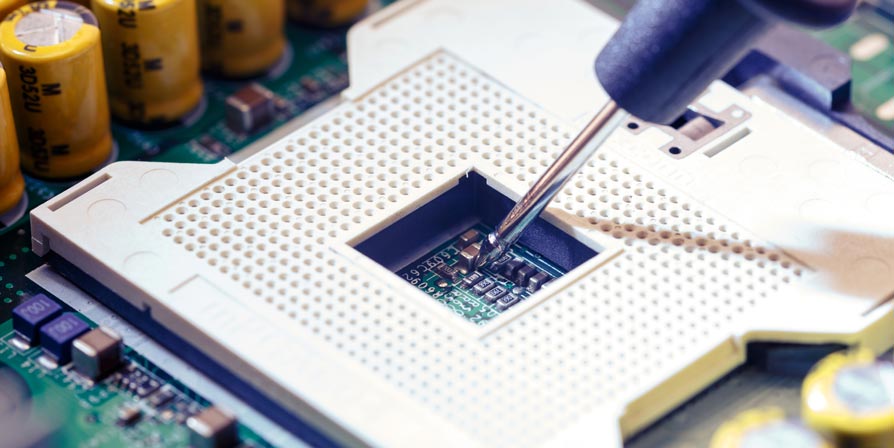
Have a Question?
What are Semiconductor Sockets?
Semiconductor sockets are specialized devices that interface the semiconductor device under test (DUT) to test equipment, enabling precise and efficient testing of semiconductor components. Sockets combine electrical, mechanical, and thermal aspects into a single assembly to streamline testing or validation of the DUT. Semiconductor sockets can be categorized as test sockets or burn-in sockets.
What is a Semiconductor Test Socket?
Test sockets are used to determine the functionality and performance of a semiconductor device. Test sockets can be used during the entire development process from initial semiconductor design to final production. Test socket features depend on specified test requirements.
What is a Semiconductor Burn-In Socket?
A Burn-in socket is an electro-mechanical device used to accelerate stress on an IC and create infant mortality, allowing the semiconductor company to eliminate weak ICs from the production population. This enables manufacturers to extend the minimum lifetime of final electronic assemblies by ensuring the reliability and quality of semiconductors before they are integrated into electronic devices. Burn-in testing increases overall reliability and reduces warranty claims of electronic products.
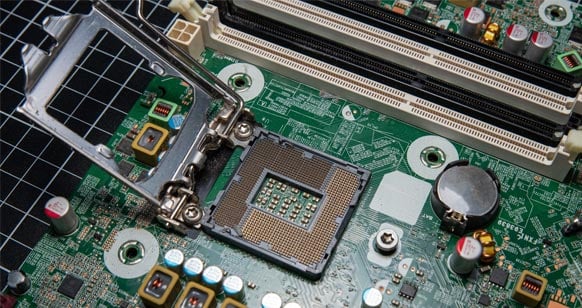
Which Semiconductor Devices Need Testing?
Semiconductor chips of all types and functionalities benefit from socket testing to identify defects, malfunctions, or performance issues early in design or manufacturing. Chip testing reduces design cycles and ensures chips meet their design specifications and quality standards and perform reliably across diverse conditions.
For instance, semiconductor chips involved in memory/data storage and logic/processing, such as DRAM, NAND Flash, ASICs, GPUs, and CPUs, undergo socket testing. Yet the specific testing approach, whether batch or 100%, varies depending on the chip’s criticality, intended application, and production volume. Regardless of the testing method, socket testing is a vital step in verifying the function and quality of these chips before they are integrated into electronic devices.
Why Do You Need Socket Testing?
Socket testing automation empowers high-speed testing and swift validation, effectively slashing test times for semiconductor components. Prompt identification and addressing defects or performance concerns during the development phase allows engineers to expedite necessary improvements, leading to shorter development cycles and quicker time-to-market. Rigorous socket testing serves as a crucial preventive measure to reduce field failure and warranty claim probability, elevate electronic product dependability and durability, and amplify customer satisfaction.
Why use Boyd Semiconductor Test and Burn-in Sockets?
Boyd stands as a pioneer in the realm of adapting package types and sizes to standard socket platforms. Our extensive semiconductor heritage spans decades, endowing us with a deep understanding of the intricacies and challenges associated with semiconductor testing. We continuously explore and develop cutting-edge contact solutions that optimize electrical connectivity, ensuring accurate and reliable testing, all while safeguarding semiconductor components against potential damage. Our package adapter is compatible with a wide spectrum of semiconductor package types and sizes, guaranteeing non-destructive testing and preserving the integrity of your valuable semiconductor components.
Elevate Testing Capabilities by Pairing Test Sockets with Boyd’s TCUs
Pair your testing sockets with Boyd’s TCUs to enhance the accuracy of test results and identify potential issues related to temperature sensitivity. Boyd sockets combined with TCUs lead to more reliable and high-performance semiconductor component development.
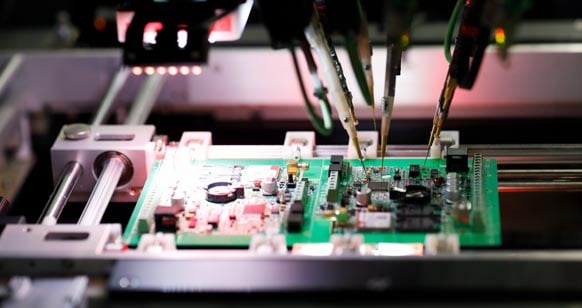
Boyd’s Semiconductor Burn-In and Testing Sockets
Boyd’s highly reliable logic and memory Burn-In and Test Sockets incorporate groundbreaking contact technology to ensure robust electrical and mechanical connections. Our platform design offers non-destructive testing capabilities and delivers unmatched flexibility in base sockets to enable seamless compatibility with various package sizes. Customized adapters are tailored to meet specific customer requirements. Our sockets come with a lifetime rating, rated to withstand up to 10,000 insertions and withdrawals, underlining their durability and long-lasting performance.
Reliability and Characterization of Testing Sockets
Reliability and characterization test sockets for semiconductor production entails rigorous assessments, a relentless focus on stability optimization, and an unwavering commitment to upholding consistent quality. By proactively addressing potential weaknesses and perpetually seeking improvement, Boyd test sockets adhere to the most stringent standards of quality and reliability throughout their entire operational lifespan, spanning from the initial test to the thousandth.
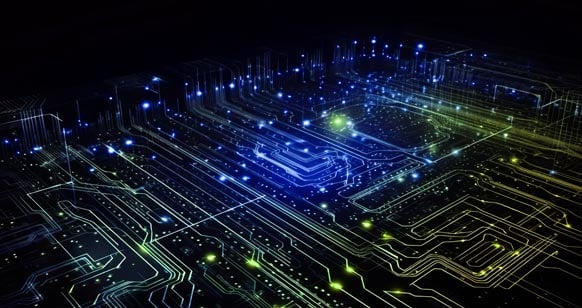
Have questions? We’re ready to help!