Medical Wearables Solutions, Stick to Skin Biosensors, and Transdermal Patches
What are Medical Wearables, Stick-to-Skin Biosensors, and Transdermal Patches and Why Does it Matter?
Medical wearables solutions including wearable devices, biosensors and transdermal patches improve patient diagnosis and treatment while reducing healthcare costs. They enable monitoring and drug delivery outside of clinical settings.
What are Medical Wearables and Stick-to Skin Biosensors?
Medical Wearable Devices are sensors specifically designed to measure a person’s biometric data like vitals, physical activity, or other physiological measurements, and are worn by the user. These devices can be disposable or durable. Disposable adhesive biosensors are self-contained with every component needed to sense and transmit patient data for a few days or weeks. Durable medical wearables feature a disposable cradle for the durable electronic device that lasts longer than a single adhesive patch.
What are Transdermal Patches?
Transdermal patches deliver medication on a wearable patch where the patient absorbs medication through their skin. Transdermal patches enable extended-release pharmaceutical delivery with comfortable long-lasting skin adhesives.
Why Boyd for Medical Wearables Solutions?
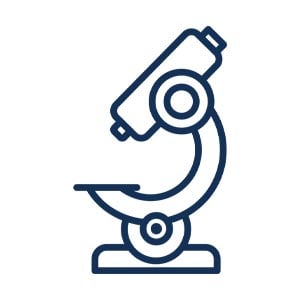
Boyd’s clean room capabilities and process innovation ensure high quality assemblies with high yield rates and minimal raw material waste to manage overall costs.
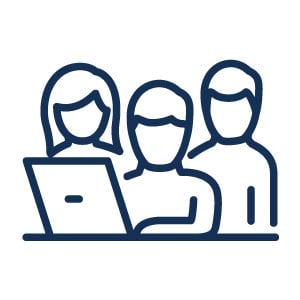
We match the right medical-grade materials to meet your specific application requirements and recommend design improvements for better manufacturability.
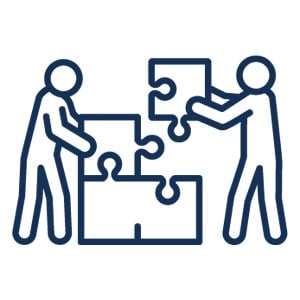
We cost-effectively source the best-fit materials for patient comfort and safety, healthcare provider efficiency, high reliability, and total cost management.
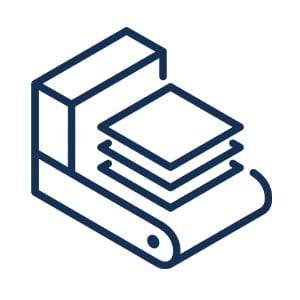
Leverage our broad manufacturing expertise to produce complete wearable devices and transdermal patches that reduce supply chain complexity.
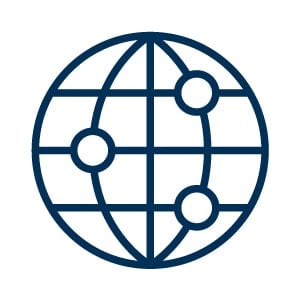
Our global FDA compliant and ISO 13485 certified clean room facilities gives you regional flexibility for sourcing and manufacturing.
Medical Wearable Solutions
Explore the intricate layers of a medical wearable in Boyd’s interactive tool.
View the medical wearable assembly components that Boyd supports by clicking the image or the button below!
Medical Adhesive Tapes and Other Wearable Solutions
(View transcript)
Medical Devices: Essential Components for Medical Wearables
(View transcript)
The Boyd Difference in Medical Wearables Solutions
Boyd has decades of experience designing, manufacturing, and delivering medical wearables solutions of all shapes and sizes with a focus on patient safety and medical efficacy. We take an integrated approach to wearable design to identify complimentary components that can be manufactured and delivered in a single assembly. With our extensive supplier relationships and innovative design support, we combine medical-grade adhesives, printed flex circuitry, injection-molded housings and components, integrated displays, switch technologies, and more to lower cost and streamline production.
Benefits of Medical Wearables Solutions:
Accelerated patient recovery with increased monitoring of prescribed activities, vitals, and other health events.
Enhanced diagnosis accuracy and speed.
Increased healthcare efficiency, convenience, customization, and cost management.
Improved diagnoses data with more frequent and consistent patient monitoring.
Better preventative care by identifying risks before they become critical.
Increased patient comfort and reduced healthcare staff workload by monitoring outside clinical environments.
Enables patients to take a more proactive role in personal health.
Ideal for insurers with reduced cost per patient.
Medical Wearables Solutions Challenges:
Small size and thin profile of most wearable designs can limit battery size and lifespan.
Medical grade adhesives, printed circuitry, hydrogels, and other components can be costly when compared to similar, non-wearable medical devices.
Balancing water resistance and breathability for cover layers can be an engineering challenge.
Specialized adhesives must be biocompatible and maintain continuous contact with the skin throughout movement and exposure to the environment.
Wearable devices can have extensive required testing for patient safety and diagnostic efficacy to meet stringent standards.
Patient comfort is key, so solutions must not only stick to skin, but be lightweight and comfortable for the wearable period.
Types of Wearables
Wearable Biometric Monitoring Devices:
Biomedical wearable devices are medical sensors that track biometric markers and information for patient testing and monitoring. This broad category of wearable devices can measure heart rate, respiration, movement, temperature, and other biometric information for diagnostics, research, or personal health. Stack-ups usually include flex circuits, PCB and battery assemblies, housings, and stick-to-skin adhesives to gather information which is either saved locally on the wearable device or sent wirelessly to the cloud.
Examples include pulse oximetry devices, blood pressure monitors, continuous glucose monitors (CGM), heart rate monitoring, and sleep trackers.
Transdermal Patches:
Transdermal patches are wearable devices that deliver extended-release pharmaceuticals, nutraceuticals, and other medicines. Transdermal patches are often worn for extended periods of time, so patient comfort, adhesive hold, and breathability are important concerns. Transdermal patch designers tailor them to specific applications to ensure that adhesives, sealing, and other components don’t negatively interact with the released medicines or chemicals.
Microfluidic Diagnostic Devices:
Microfluidic diagnostic devices are small, intricate medical wearables used to monitor glucose, metabolites, pH levels, and other biomarkers from blood, sweat, or other fluids at the molecular level. Microfluidic diagnostic devices include sensors that receive data from the user, and are often made up of many intricate layers, including cover films, cushioning layers, printed flex circuits, hydrogel electrodes, battery and PCB assemblies, and more.
Examples include blood glucose strips, diabetic testing, diagnostic tapes, and in-vitro diagnostic equipment.
Ground Dressing and Electrode Wearables:
Ground dressing and electrode wearables use electrodes and grounding contacts along with stick-to-skin adhesives to measure electrical impulses for diagnostics or transfer electronic pulses to the body for electrotherapy. Like wearable biomedical and diagnostic devices, these can include complex stack-ups, but always include electrodes for electrical current sensing or stimulation. Biocompatibility, durability, and patient comfort are the primary considerations for biomedical and electrode wearables as they are often worn over long periods of time.
Examples include electrocardiography (ECG/EKG), electroencephalography (EEG), electromyography (EMG), and electrotherapy devices.
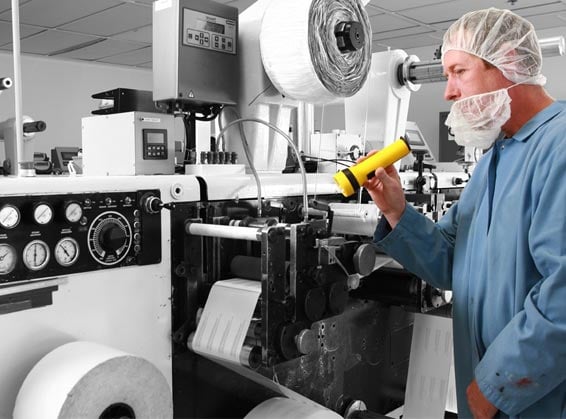
Boyd’s Medical Expertise
Boyd’s medical converting and material expertise spans over 25 years. Our world class Quality Management Systems enable us to consistently fabricate high quality medical products for a broad range of applications. Through our FDA Registration, UL certified fabrication, and RoHS and REACH compliance, Boyd’s team is ready to support your most challenging medical wearable applications with reliability, repeatability, and traceability. We have experienced medical staff throughout operations, engineering, sourcing and customer success support personnel. Our qualified team can support your medical wearable device with thorough project management from concept to commercialization.
Global Support for Medical Manufacturing
Boyd’s medical design team spans six countries and three continents, leveraging seven ISO 13485 Certified manufacturing facilities worldwide. This team provides regulatory support through design, prototyping and manufacturing of Class I, II and III medical devices. Our design for excellence (DFX) services and rapid prototyping enable quick regulatory revisions and responsiveness through design, development and prototyping cycles. Our engineering and manufacturing team maintains deep knowledge and support for medical sterilization services in Class 100 to 10,000 Medical Cleanroom Manufacturing. We pride ourselves in our medical compliant processes and traceability from site to the work order level.
Medical Material Science and Handling Expertise
Cleanliness is critical for patient safety and medical wearable device reliability. Wearables must be free of foreign debris and contaminants to ensure the utmost quality. These devices adhere to skin, one of the most diverse and sensitive substrates to attach to. Medical Wearable Devices must feature specialty adhesives designed for patient comfort and reliable performance across a variety of skin types, including neonatal and geriatric, and a variety of skin conditions. Boyd maintains a variety of clean room environments in all key geographies with processes and protocols to handle and fabricate medical materials with increasing levels of cleanliness requirements:
- Contaminant-free material storage and handling protocols
- Cleanroom raw material slitting and preparation processes
- Cleanroom advanced rotary converting manufacturing lines
- Cleanroom flat bed converting manufacturing lines
- Cleanroom cosmetic inspection
- Class 100 clean rooms
- Class 1000 (Class 1K) clean rooms
- Class 10000 (Class 10K) clean rooms
- Class 100000 (Class 100K) clean rooms
- UV sensitive clean room manufacturing
- Temperature sensitive material handling processes
Cleanroom environments include ongoing monitoring to assure medical materials and medical wearable devices are contaminant-free and on-specification:
- Filter installation leak testing
- Airborne particle count testing
- Airflow velocity testing
- Temperature testing
- Relative humidity testing
- Light intensity level testing
- Sound pressure level testing
- Room pressurization testing
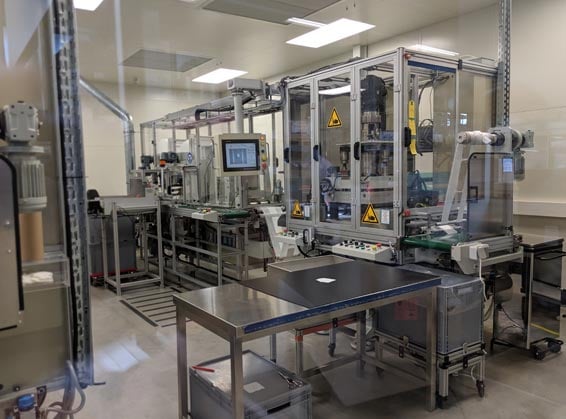
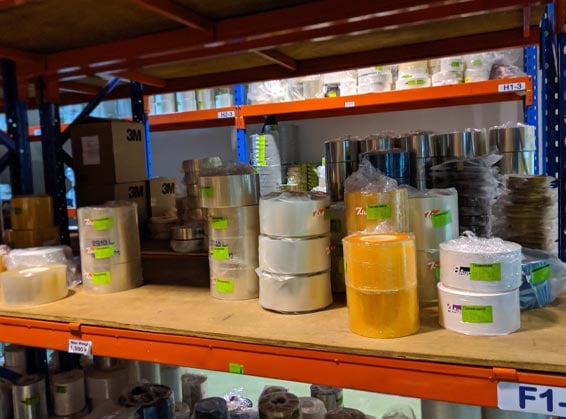
Supply Chain Management
The medical wearable device value chain is complex with many participants. Boyd helps simplify this landscape for you, delivering innovative medical wearables solutions and differentiated performance at optimal total cost.
We help raw material suppliers innovate material formulations and enhance material performance constantly. These high quality medical materials are available in large format rolls and sheets that we use to custom fabricate medical wearable designs. Boyd’s strategic supply relationships date over 50 years, including raw material suppliers like 3M, tesa, and Nitto. We actively search for new, innovative materials that can help our customers differentiate their wearable devices by improving patient comfort, extending wearable material wear time, and optimizing wearable application for healthcare professionals.
Leverage Boyd’s 25+ years of medical expertise to enhance your product.
Key Wearables Terms to Know :
Term | Definition |
---|---|
Decorative Overpatch | Decorative layer that encases the entire wearable patch to protect it from the elements and hold it together. Can be a printable film or a molded component. |
Cover Film | Nonwoven, foam, or tech-fabric layer that provides sealing protection, enhances aesthetics of wearable |
Inner Cushion Layer | Encases the internal electrical assembly of the wearable and provides cushioning and protection. It can be cut foam or a thermoformed foam cover if 3D features such as pockets or cavities are needed. |
Printed Flex Circuit / Trace Layer | The electronic circuit that connects stick-to-skin electrodes to the device electronics. Can be flexible copper traces or printed with conductive inks with single or dual side printing to connect the hydrogel to PCB. |
Printed Circuit Board Assembly (PCBA) | On-device electronics that connect power and sensors, also houses on-board data storage or data transmission via Bluetooth or other signals |
Battery Assembly | Lightweight power source that powers the PCBA and biosensors connected via the flex circuit. |
Construction Adhesive | Pressure sensitive adhesives that bond various layers of a medical wearable together to enhance structural integrity. |
Pressure Sensitive Adhesive (PSA) | Adhesives that are permanently tacky at room temperature and firmly adhere to irregular surfaces with just the need for light pressure and no cure time. Can be blends of natural or synthetic rubber and resin, acrylic, silicone, or other polymers. |
Skin Contact Foam | Foams used on the back of the skin contact adhesive used to improve wearability and comfort. Hydrophobic and hydrophilic foams are often used to improve sealing and breathability. |
Skin Contact Adhesive | Biocompatible adhesives used to attach wearable to skin chosen based on wear time, removability, skin sensitivity, and other specific application needs. |
Conductive Hydrogel Electrodes | Thick, gel-like polymer with high moisture content and minerals added to increase electrical conductivity. Used for both sensing and stimulating applications. |
Hydrocolloids | Complex polymeric adhesives that are highly adhesive and absorbent, and impermeable to bacteria. Often used to provide a moist healing environment ideal for uninfected wounds. |
Delivery Liner | A medical-grade liner and carrier used to protect stick-to-skin layer and aid the wearable application to patient. Available with pull tab features, split liners, and folded liners for ease of removal and application. |
Closing
1 billion + skin contact grade products fabricated globally.
One Decade + of supporting wearable device design and fabrication innovation.
World Class customer support through extensive regulatory cycles, approvals, and ramp complexities.
Decades long relationships with the world’s best material suppliers, getting customers the latest materials available.
Continued capacity expansion, capability improvements, and process development.
Have questions? We’re ready to help!