Wearable Tech’s Material Edge
Wearable medical technology, ranging from diagnostic and monitoring devices to drug delivery patches, is transforming healthcare and driving medical care innovation. Selecting the right materials is essential to ensure optimal performance and durability of these devices. By leveraging Boyd’s extensive fabrication services and industry-leading materials, medical device manufacturers enhance product quality, streamline production processes, improve patient safety and treatment, and accelerate time to market.
Material Selection for Optimal Wearable Device Performance
Boyd plays a crucial role in advancing various types of wearable medical devices, including continuous glucose monitors (CGMs), biosensors, ECG monitors, blood pressure monitors, drug delivery devices, and transdermal patches. Selecting materials for each device layer is critical for these devices to perform optimally and to enhance patient comfort. Starting from the outermost decorative protective layer to the innermost skin contact layer, Boyd ensures every component is meticulously engineered to meet the specific needs of the device while maximizing patient safety.
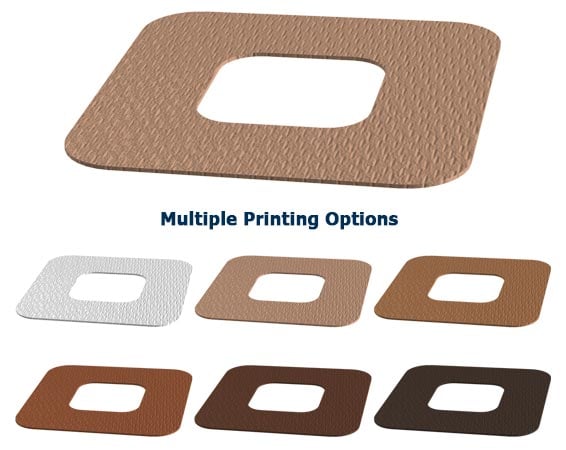
Decorative Protective Layer: Sealing, Aesthetics, and Branding
The decorative protective layer provides essential sealing protection and holds all device components together while enhancing its aesthetics. Often made from printable films or molded components, this outermost layer ensures durability and allows for branding differentiation. Boyd uses materials like nonwoven fabric, foam, and tech-fabric, and places printed logos, branding elements, or user instructions directly onto these surfaces. These materials withstand regular wear, routine cleaning, and exposure to harsh sanitizing chemicals without compromising skin adhesion or causing patient discomfort.Housing Layer: Waterproofing and Component Protection
The housing layer protects sensitive internal components within the wearable device stack-up. Boyd uses materials like flexible single-coated medical film tape to waterproof devices. We carefully select materials that ensure compatibility across all layers, maintain breathability, and prevent skin damage, ultimately enhancing the device’s overall performance and safety.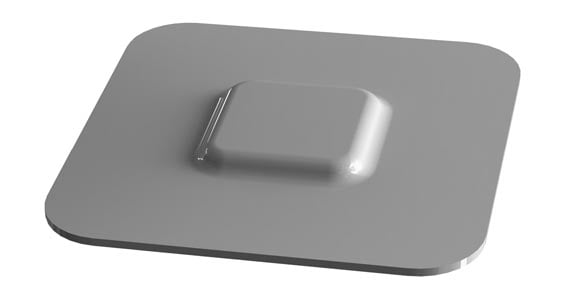
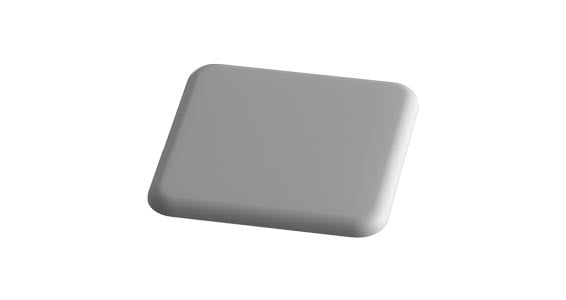
Cushioning Layer: Impact Protection and Comfort
Cushioning materials encase internal electrical assemblies, provide impact protection, and ensure user comfort by preventing skin damage. We use foams and foam tapes, which we can easily die-cut or thermoform to cover complex 3D features such as pockets or cavities in device designs. Additionally, we employ conductive foams to offer EMI/RFI protection, safeguarding sensitive electrical components from potential damage.Printed Flex Circuit Layer: Connectivity and Power Supply
The printed flex circuit layer connects stick-to-skin electrodes to the device’s electronics using flexible copper traces or conductive inks. Boyd offers single- and dual-side printing to maximize design flexibility and enable efficient connections between hydrogels and PCBs. We collaborate with material fabricators to develop complete printed circuit board assemblies (PCBA) that facilitate power connections, data storage, and wireless data transmission via Bluetooth or other signals. Common materials used in this layer include double-coated foam tape, films, and conductive inks.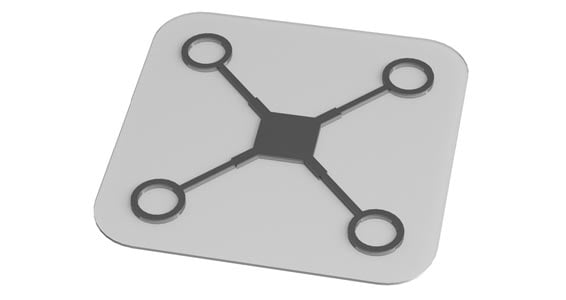
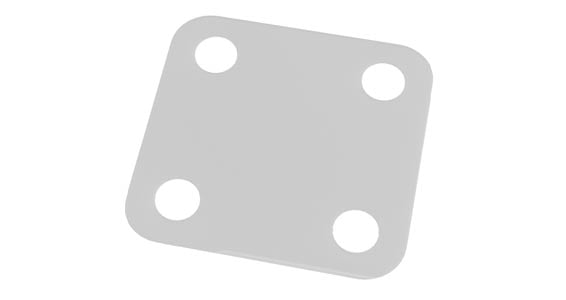
Skin Contact Layer: Adhesion, Comfort, and Safety
The skin contact layer ensures patient comfort and safety. Boyd selects biocompatible adhesives that securely attach wearable devices to the skin, considering factors such as wear time, removability, skin sensitivity, and moisture management. We use foam materials on the back of skin contact adhesives to enhance comfort and wearability. Boyd employs hydrophobic and hydrophilic foams to improve sealing and breathability, ensuring a comfortable and safe experience for the patient. Common materials used in this layer include short-term-wear acrylic adhesives, medium-term-wear acrylic adhesives, and long-term-wear acrylic adhesives.Delivery Liner: Easy Removal and Application
Boyd designs easy-to-remove delivery liners to optimize application efficiency and enhance patient comfort. We die-cut liner materials into complex shapes to match device designs precisely, minimizing material waste. Our delivery liners feature pull tabs, split liners, and folded liners for easy and efficient liner removal and patient application. Common materials used for liners include poly coated paper, super calendered Kraft, and polymeric films (PET, HDPE, BOPP), with options for single-side siliconized, double-side siliconized, and custom liners.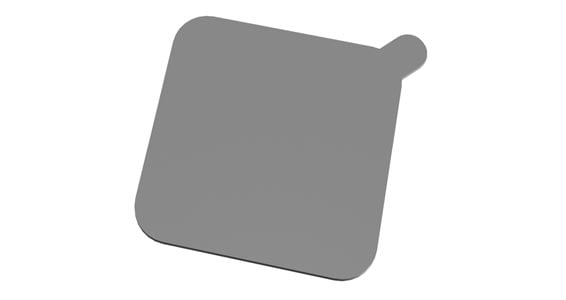
Enhanced Patient Outcomes with Boyd’s Material Solutions
With the combined expertise of Boyd’s engineers and material specialists, we expertly guide medical material selection and optimize wearable device design. Our comprehensive solutions address every aspect of wearable medical devices, from housing layers that protect internal components to cushioning layers that provide impact protection and user comfort, printed flex circuit layers for electronic connectivity, skin contact layers for patient safety, and delivery liners for efficient application. These innovations ensure reliable device performance, improved patient treatment and safety, and accelerated time to market. Choose Boyd for your material selection needs in medical wearables to benefit from our expertise. Contact us today to discuss your project or schedule a consultation with our experts.