Precision Converting
Precision Converting blends advanced engineered material science and the art of reliable, high accuracy fabrication processes to transform multiple raw materials into usable formats. Boyd’s specialty is to use precision converting to integrate multiple materials or processes to generate one integrated finished component.
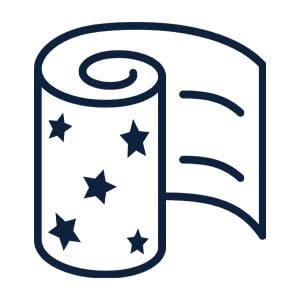
Unlimited Raw Material Options
With Boyd’s close material suppliers and our own fabrication, we can find the best fit material for your application that balances function, performance, and cost.
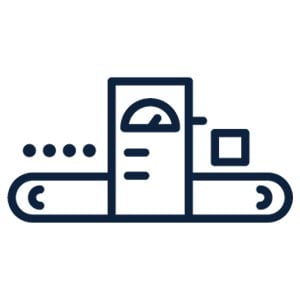
High Volume Product Quality and Consistency
Quickly and consistently convert raw material into usable components and assemblies, maximizing material utilization and reducing costs.
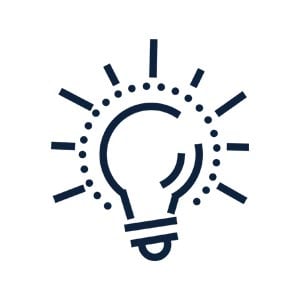
Creative Design Support
Boyd’s experienced design and manufacturing teams help you develop innovative solutions and processes to meet your project needs.
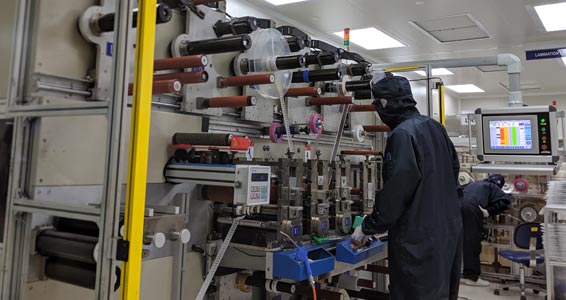
Why Boyd’s Precision Converting?
Boyd’s precision converting expertise spans a broad range of capabilities that service high to low volume mass production and advanced prototyping capabilities easily scalable and translatable into volume processes. Our engineering and manufacturing teams are not only experts in traditional converting processes but also constantly innovate these processes and systems. Boyd’s innovations in precision converting methodologies allow us to maximize efficiency, yield and material utilization to deliver to our customers better service, more repeatable and reliable results, advanced solutions and optimized total cost of ownership.
Boyd’s Complete Support for Your Precision Converting Project
Boyd partners closely with your research, design, and purchasing teams to solve complex manufacturing and assembly problems that reduce your overall costs. Our team determines the most optimal raw materials that will inherently exceed the performance requirements of a component, recommends ways to blend raw materials together for more advance performance characteristics, evaluates the design landscape around a component for additional opportunities to integrate complementary elements, designs for scalable mass production within our own converting processes and the most efficient integration into your end device assembly channels, all while reviewing and meeting your cost targets. We design complex laminations to combine critical performance characteristics of multiple materials, fully customized to benefit and optimize your end device performance.
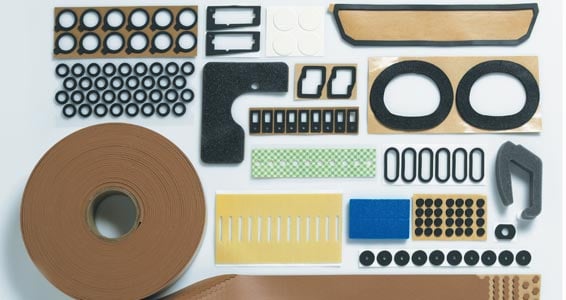
Material Science Expertise
By defining key performance characteristics and carefully selecting best-match raw material solutions, Boyd maximizes your product’s long-term and reliable performance. We bridge the gap between the hundreds of thousands of mass format raw materials globally available and identify the specific materials you need that are consumable in a format that you can incorporate within your design. A key tenant to helping you develop the most cost-effective material solutions includes maximizing material utilization. We are experts in utilizing smart industrial manufacturing design to optimize yields and help you save on raw material costs.
Value-Add Precision Converting Processes
Boyd specializes in incorporating additional value within our components by integrating easy-peel-tabs, extended liners, and high precision registration control. These features help streamline your assembly process by reducing the likelihood of component tear upon liner removal and minimizing the difficulty of removing peel liners. High accuracy registration control ensures proper automated component pick-and-place within your assembly operations to increase yield rate.
Boyd’s fully integrated, in-house precision converting capabilities are globally available across multiple facilities across three continents with expertise to provide competitive solutions to virtually any industry.
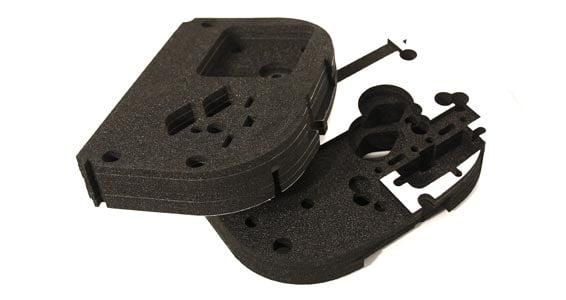
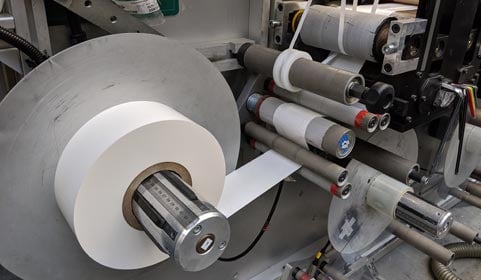
Advanced Rotary Die Cutting
A wide range of integration possibilities with ultra-tight or zero-gap tolerances, combining multiple products into one deliverable solution with registration optimized for automated assembly systems. Boyd’s Rotary Converting is ideal for high volumes and has the capability to die cut, kiss cut, slit, laminate, score and sheet your product in line.
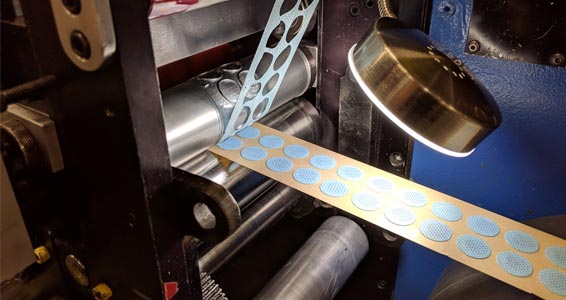
Laminating & Multi-Layer Assemblies
Laminate a variety of materials to produce easy-to-handle multifunctional assemblies instead of purchasing separate components. Boyd’s laminating processes combine materials like advanced adhesives, thermally conductive and optical films, electromagnetic control films, foams and many other materials, with easy-peel-tabs and extended liners on roll stock to optimize yields, improve your assembly time, enhance material utilization, and reduce raw material and supply chain costs.
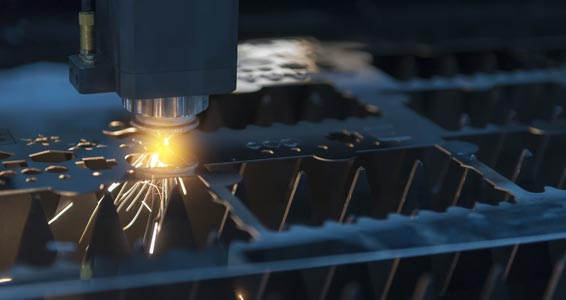
Laser Cutting
Convert raw materials into complex shapes with a precision-controlled laser. Laser cutting is ideal for quick prototyping since it’s die-less with no tooling cost, meaning you can receive samples fast and cost affordably. Laser converting is also great for thick or tough materials that may not be suitable for die cutting and for low to medium mass production volumes.
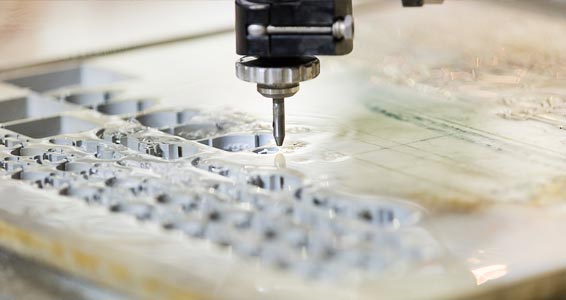
Water Jet Cutting
Convert raw materials into complex shapes with a high-power precision water jet, optimal for low to medium mass production volumes and thicker, highly compressible raw materials that may deform in traditional die cutting processes. Water Jet Cutting is CAD-controlled meaning you have no tooling investment, making it ideal for affordable, quick prototyping.
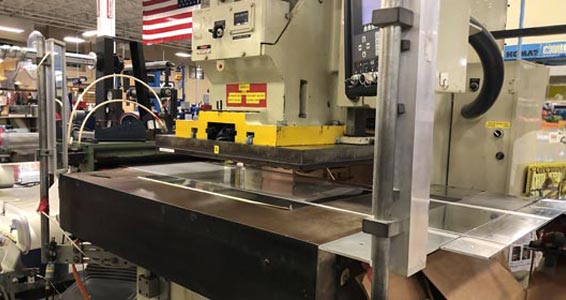
Flatbed Die Cutting
Utilize steel-rule, horizontally oriented dies to convert raw materials with processes and equipment that incorporate varying degrees of automation, press tonnage and dimension constraints optimized to suit a wide range of production volumes. Flatbed die cutting is an ideal alternative for larger format components, thicker materials and demand volumes that may not be ideal for rotary converting processes.
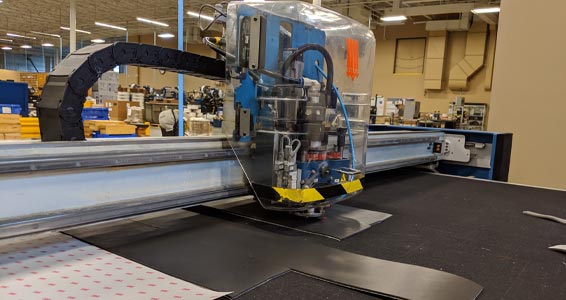
CNC Precision Knife Plotter
Precision Knife Plotters utilize a CNC program to define a knife cutting path to convert raw material into a finished product. Knife Plotters are great for prototyping and low volume production since there is no required tooling or associated tooling costs.
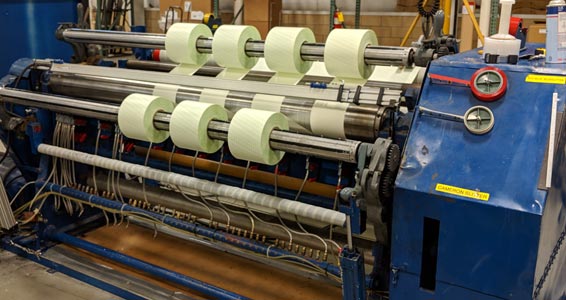
Slitting
Slitting and Splitting cut mass form raw material rolls down to a more usable and efficient material roll width. We can slit and rewind various independent raw materials to provide custom width material rolls. We can also precisely laminate various substrates and adhesives together and slit the material stack up to develop a custom roll material solution for your needs or improve input raw material yield in our downstream fabrication processes.
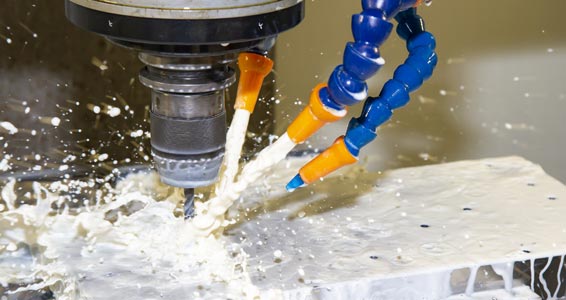
CNC Machining
CNC Machining is a unique way to fabricate 3D foam shapes for solutions that require complex geometries. By programming a machine to carve out specific shapes within a piece of foam, Boyd’s CNC Machining produces highly customized, single piece foam products.
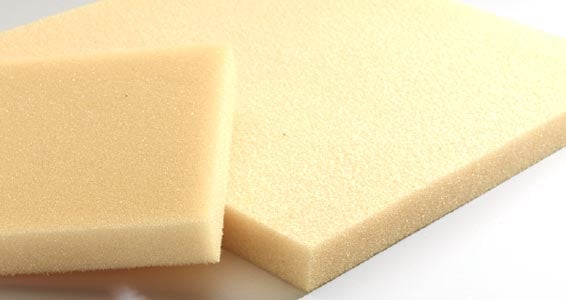
Skiving
Have questions? We’re ready to help!