What is a Liquid Cold Plate?
A Liquid Cold Plate (LCP) is responsible for efficiently transferring heat from surfaces with high heat loads to the fluid used within a liquid cooling system. The performance of the liquid cold plate is critical in defining the overall effectiveness of a liquid system.
Liquid Cold Plates
A liquid cold plate (LCP) serves as a critical interface within a liquid cooling system, guiding pumped fluid to heat sources and transferring waste heat into the coolant for subsequent cooling. Cold plates feature a heat source mounting surface, internal passages for liquid to pass through, and an inlet and outlet. Thermal engineers optimize cold plate liquid flow path design and construction to maximize cooling within the liquid cooling system constraints like pressure drop and flow.
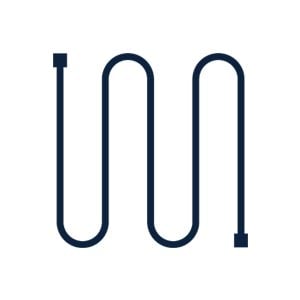
100% In-Line Testing
Reliable, 100% leak tested cold plates produced for decades.
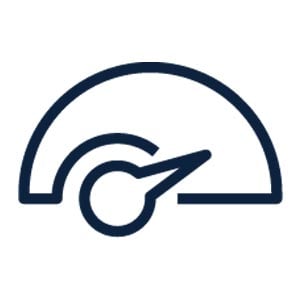
Push product performance with next level cooling
Outperform air cooling with effective liquid cooling plates
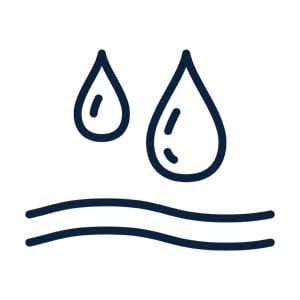
Optimize Direct Liquid Cooling Interfaces
Custom cold plate skylines and pedestals maximize the interface between a heat source and the cooling system for peak performance.
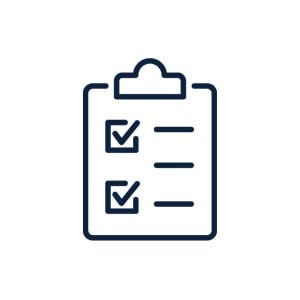
Highly Customizable
Optimize design for balance flow rate and pressure drop for optimized performance.
How Do Liquid Cold Plates Work?
A cold plate by itself does not cool devices; it must be integrated into a liquid loop that includes a pump for fluid circulation and a heat exchanger to reject the heat absorbed by the cold plate.
Why use Liquid Cold Plates?
Leverage the high heat capacity of liquid to quickly absorb more heat than air cooled thermal management solutions. Coldplates excel at dissipating high-density, high-output heat loads within a diverse range of system configurations, facilitating the effective transfer of heat into the liquid cooling system.
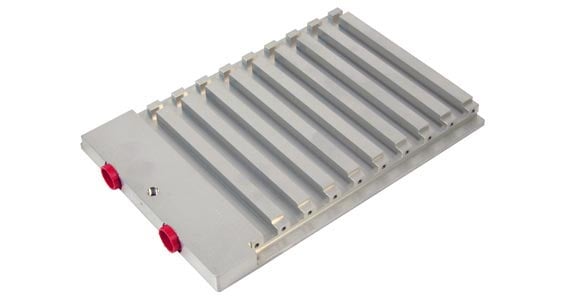
Why Choose Boyd for your Liquid Cold Plate?
Boyd’s engineers excel at developing and manufacturing high quality, compact, and durable coldplates to meet your system requirements while reducing weight and complexity. We leverage accurate performance simulations based off decades of empirical data to quickly optimize cold plate design and accelerate your design cycle. Boyd’s extensive fabrication methods and 100% leak tested construction options help you reduce product weight, push performance, or decrease overall assembly size with high performance LCPs.
Liquid Cold Plate Solutions for e-Mobility and Transportation
(View transcript)
Ruggedize Batteries to Withstand Environmental Exposure
(View transcript)
High Efficiency Cooling Components
Liquid cold plates act as the part of a liquid cooling system that absorbs waste heat from devices like semiconductors, microprocessors, printed circuit board assemblies (PCBAs), or other power electronics and transfers it to the liquid cooling system. Optimize cooling efficiency and uphold the ideal operating temperature of electronic components by harnessing the exceptional heat-absorbing capabilities of liquid through cold plates.
Have a Question?
Boyd Liquid Cooling Loop and Cold Plate Reference Designs for Latest Chips from
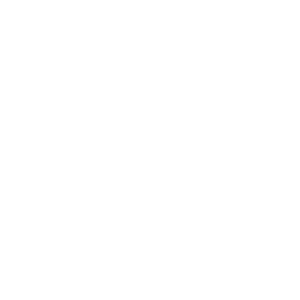
NVIDIA
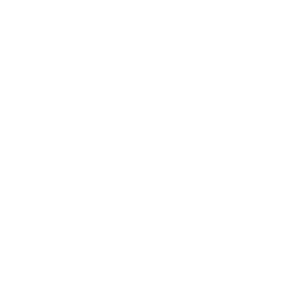
Intel
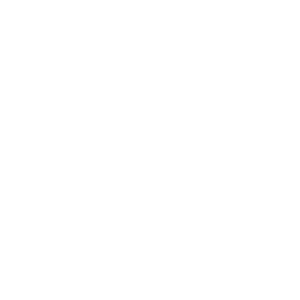
AMD
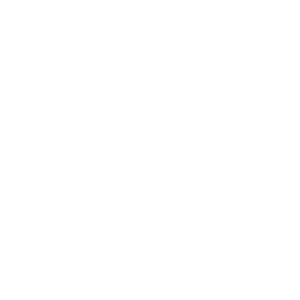
Broadcom
EV Battery Solutions
View our 3D interactive tool to explore Boyd’s EV battery solutions and how we drive multifaceted innovation. Click the image or the button below to immerse yourself with our EV battery solutions!Meet Application Requirements with the Right Construction
Since liquid cooling is utilized in a wide variety of applications, Boyd has developed a diverse range of liquid cold plate technologies to offer customers an optimized solution for their application. Our engineering team leverages the best fit technology to meet project requirements like thermal performance, flow rate, resistance and pressure drop, wetted path materials, weight, durability, and geometry.
Learn more about our most popular LCP technologies:
Part Number | Description | Downloads | Contact Us |
---|---|---|---|
CP20G01 | Flat Tube Liquid Cold Plate | Thermal Graph | Contact Us |
CP20G03 | Flat Tube Liquid Cold Plate | Thermal Graph | Contact Us |
416101U00000G | Hi-Contact™ Tube Liquid Cold Plate | 416101U00000G Datasheet | Contact Us |
416201U00000G | Hi-Contact™ Tube Liquid Cold Plate | 416201U00000G Datasheet | Contact Us |
416301U00000G | Hi-Contact™ Tube Liquid Cold Plate | 416301U00000G Datasheet | Contact Us |
416401U00000G | Hi-Contact™ Tube Liquid Cold Plate | 416401U00000G Datasheet | Contact Us |
416501U00000G | Hi-Contact™ Tube Liquid Cold Plate | 416501U00000G Datasheet | Contact Us |
416601U00000G | Hi-Contact™ Tube Liquid Cold Plate | 416601U00000G Datasheet | Contact Us |
CP10G01 | Tube Liquid Cold Plate | Performance | Contact Us |
CP10G03 | Tube Liquid Cold Plate | Performance | Contact Us |
CP10G05 | Tube Liquid Cold Plate | Performance | Contact Us |
CP10G07 | Tube Liquid Cold Plate | Performance | Contact Us |
CP10G14 | Tube Liquid Cold Plate | Performance | Contact Us |
CP10G16 | Tube Liquid Cold Plate | Performance | Contact Us |
CP10G18 | Tube Liquid Cold Plate | Performance | Contact Us |
CP10G20 | Tube Liquid Cold Plate | Performance | Contact Us |
CP12G01 | Tube Liquid Cold Plate | Performance | Contact Us |
CP12G05 | Tube Liquid Cold Plate | Performance | Contact Us |
CP15G01 | Tube Liquid Cold Plate | Performance | Contact Us |
CP15G05 | Tube Liquid Cold Plate | Performance | Contact Us |
Stamped Liquid Cold Plates
Stamped cold plates are a lightweight cold plate construction that leverages the manufacturing efficiency of aluminum stamping one or both sides of the LCP. This approach further reduces manufacturing time and costs by streamlining flow path, mounting geometry, and other features into a single process and eliminates CNC time. Stamped cold plates can be enhanced with internal fins to boost thermal efficiency and are controlled atmosphere brazed (CAB) brazed for 100% leak tested seals.
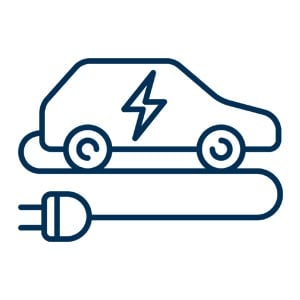
eMobility
Electric vehicle batteries, on-board electronic, power conversion
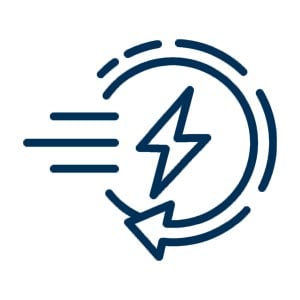
Energy Management
Power conversion
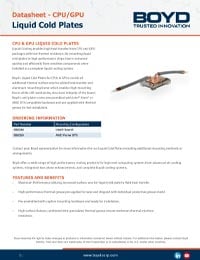
Standard Reference Design: Boyd Standard CPU Liquid Cold Plate Datasheet
Machined Liquid Cold Plates
Machined and brazed cold plates offer the most flow path and structural geometry customization for a heat source to liquid system interface. Optimize complex, 100% leak tested flow channels with precision CNC machining and high-quality CAB or vacuum brazing. Boyd’s broad technology portfolio enables additional performance boost with fin inserts to further enhance heat transfer into the liquid system.
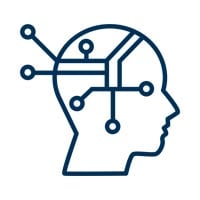
Artificial Intelligence & Cloud Computing
Semiconductor and processor cooling

Industrial Process Equipment
Motor drive cooling, power conversion, laser and sensor cooling
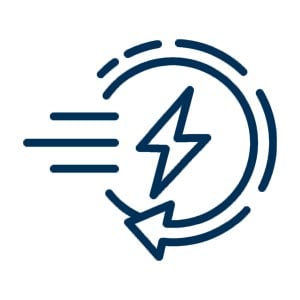
Energy Management
Power conversion, battery energy storage systems
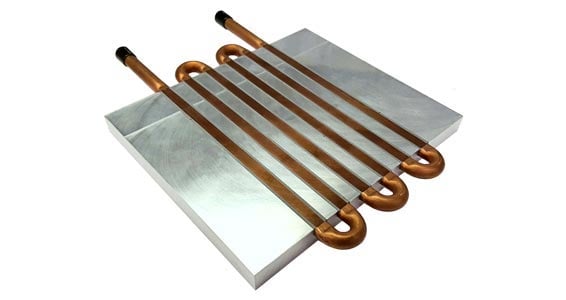
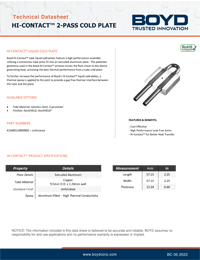
Boyd Hi-Contact 2 Pass Datasheet
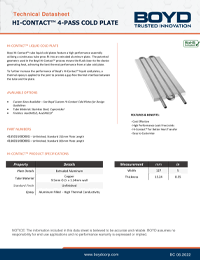
Boyd Hi-Contact 4 Pass Datasheet
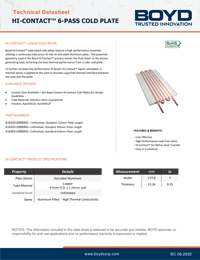
Boyd Hi-Contact 6 Pass Datasheet

Industrial Process Equipment
Motor drive cooling, power conversion, laser and sensor cooling
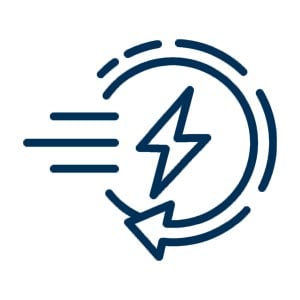
Energy management
Power conversion
Flat Tube Manifold Liquid Cold Plates
Flat tube cold plates are ideal to cool small, high heat density components like thermoelectric coolers in limited vertical spaces. Using thin-walled aluminum multi-port extrusion (MPE) tubing, flat tube cooling plates minimize thermal resistance between the cold plate and heat source and produce surface thermal uniformity. Flat tube LCPs use more viscous fluids like ethylene glycol and water (EGW), oils, 3M Fluorinert®, and Polyalphaolefin (PAO) with their enhanced internal surface area and low pressure drop.
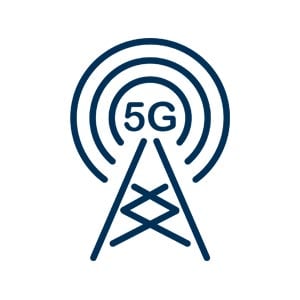
Telecommunications
Computer or server microprocessor cooling and test equipment thermal management

Aerospace
Lightweight avionics, motor and electronics cooling solutions in more electric aircraft (MEA), electronic heat transport to stowed radiator panels during satellite launch. They can also operate as thermal diodes to prevent backward heat leak.
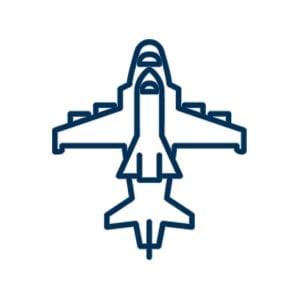
Defense
Actuator-mounted electronics cooling, engine waste heat wing and cowl anti-icing, and thermal signature suppression
Liquid Cold Plate Customization
Materials
- Aluminum
- Copper
- Stainless Steel
Wetted path needs to be compatible with other components in the liquid loop. Mixing copper and aluminum leads to galvanic corrosion that decreases system performance and lifetime.
Flow Path Options
- Meso-channel
- Parallel channel
- Tube and/or manifold
Manufacturing Processes
- CNC machining
- Friction stir welding
- Stamping
- CAB brazing
- Vacuum brazing
Cold Plate FAQs
What is a cold plate?
A cold plate is a thermal management component that cools high-heat devices by transferring heat directly to a liquid coolant flowing through the plate. This process effectively removes excess heat and helps maintain optimal operating temperatures. A cold plate must be connected to a complete liquid cooling system.
How does a cold plate work?
A cold plate transfers heat from high-heat components to a circulating liquid coolant. When a component generates heat, the cold plate absorbs it through its surface, the heat flows into the liquid coolant, which carries it away from the component.Where are cold plates used?
Cold plates are used in applications where efficient thermal management is essential. They help prevent overheating and improve performance in applications like data centers, power electronics, and electric vehicles (EVs).What is the purpose of a cooling plate?
The purpose of a cooling plate is to dissipate heat from high-heat components, preventing overheating and ensuring stable operation. By efficiently transferring heat to a liquid coolant, cooling plates help maintain optimal temperatures and improve the performance and reliability of systems in demanding environments.
What is the principle purpose of a cold plate?
The principle purpose of a cold plate involves transferring heat away from high-heat components through conduction and convection. As a component or device generates heat, the cold plate absorbs it through its surface. The absorbed heat flows into circulating liquid coolant, which carries the heat away and dissipates it through a heat exchanger or liquid cooling system.How to design a cold plate?
Engineers analyze a system’s heat load and flow requirements. They select materials with high thermal conductivity and design internal channels to optimize coolant flow and heat transfer. They use computational simulations to refine the design for maximum efficiency. Engineers tailor cold plates to fit specific applications like power electronics, EV batteries, or medical devices. Explore more about liquid cold plate design.
Is a cold plate a heat exchanger?
Technically yes, a cold plate functions as a type of heat exchanger that focuses on energy absorption. It absorbs heat from high-heat components and transfers the heat to a circulating liquid coolant, efficiently removing heat to maintain optimal temperatures and prevent overheating in systems. But the thermal management industry typically uses the term “heat exchanger” to refer to thermal components that use two fluid paths focused on heat rejection from the system. Explore more about heat exchangers.
What is the thermal resistance of a cold plate?
The thermal resistance of a cold plate measures its effectiveness in transferring heat from the component or device to the coolant. It is calculated as the temperature difference across the cold plate divided by the heat flow rate. A lower thermal resistance indicates better heat transfer performance, enabling the cold plate to efficiently manage heat in various applications.What are the dimensions of a cold plate?
The dimensions of a cold plate vary based on its specific application and design requirements. Cold plates range from a few inches to several feet in length and width, with thicknesses typically between 0.25 inches and 1 inch. Engineers customize these dimensions to fit the components they cool, ensuring optimal performance in various applications.
What is the difference between a cold plate and a heat pipe?
A cold plate and a heat pipe serve distinct roles in thermal management. A cold plate transfers heat directly from a component or device to a circulating liquid coolant, efficiently dissipating heat to maintain optimal temperatures. In contrast, a heat pipe uses a phase change process to move heat. A liquid inside the heat pipe evaporates when heated absorbing heat. It condenses back into a liquid when cooled, releasing heat. Cold plates excel in cooling high-heat components, while heat pipes effectively manage passive heat transfer across longer distances. Visit our heat pipes page to learn more about how heat pipes function and their applications.
What material is used for cooling plates?
Cooling plates are typically made from materials with high thermal conductivity, such as aluminum and copper. Aluminum is lightweight and corrosion-resistant, making it ideal for many applications, while copper offers superior heat transfer but is heavier. Engineers choose the material based on factors like thermal performance, weight, cost, and the specific requirements of the cooling system.What is the difference between a heat sink and a cold plate?
A heat sink dissipates heat from a component into the surrounding air through convection and radiation. It consists of metal fins, or a solid structure designed to increase surface area for better airflow. In contrast, a cold plate transfers heat directly from a component to a liquid coolant circulating through it. Cold plates provide more efficient heat removal in applications with high heat loads, such as power electronics and data centers, while heat sinks are often used in less demanding environments.
Have questions? We’re ready to help!