Electric Vehicle Liquid Cold Plate Case Study
Introduction
When creating a new series of batteries for electric vehicles (EVs), a leading battery producer approached Boyd to design new liquid cold plates for the battery packs. The new battery packs would be featured in large electric specialty vehicles (such as fire and refuse vehicles) which require extensive amounts of power, leading to strict thermal and weight management requirements.
Project Details
Customer:
Electric Vehicle Battery Manufacturer
Application:
Specialty Electric Vehicle Batteries
Technology:
Liquid Cold Plates
Industry:
eMobility
Location:
United States
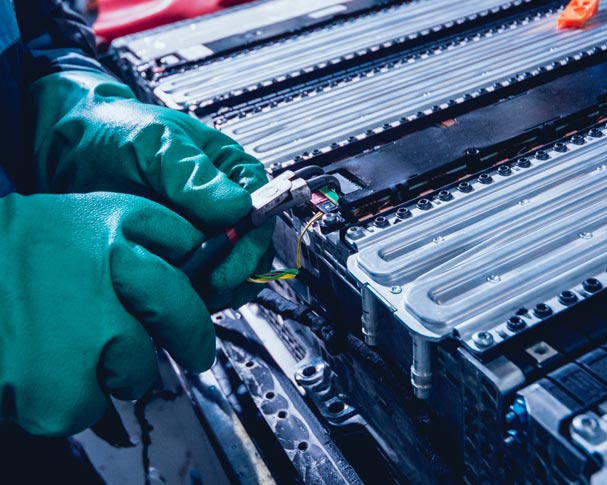
EV Battery Cooling Challenge
The customer discovered several challenges during initial battery pack development. While experienced in creating smaller batteries for power tools and indoor utility vehicles, they were transitioning to creating battery packs for large, specialty EVs.
The specialty vehicle power demand required new, larger battery pack designs for each EV model which resulted in high heat loads. To ensure that the larger battery packs remained cool enough for operation throughout the vehicle’s lifespan, the customer needed custom liquid cold plates (LCPs) designed specifically for this application. Each battery would also need a high-performing TIM (Thermal Interface Material) to contact the battery heat source and minimize heat loss during transfer to the liquid cold plates and liquid cooling system.
Initially, weight was not seen as a big design concern, given the already large size of the battery packs and the complete specialty vehicle. However, throughout evaluation and testing, concerns grew regarding the size of the LCPs potentially affecting battery range. To ensure the added LCP weight minimally affected battery range, it also became crucial for the cold plates to be as compact and light weight as possible.
Boyd’s EV Liquid Cold Plate Solution
Work began in one of Boyd’s dedicated design centers, where an extensive thermal analysis was performed on each of the new battery pack sizes to define the exact, optimal thermal requirements for the project. Once these parameters were defined, Boyd presented several different past cold plate examples that had been successfully implemented into electric vehicle batteries with similar requirements. Several TIMs were also presented, each featuring different thermal properties.
After evaluating options, Boyd’s engineers and the customer collaboratively decided that an aluminum liquid cold plate featuring a fiber-reinforced thermal pad would be the optimal solution. Boyd’s design center engineers immediately began developing drawings based on each individual battery pack’s needs. While initial designs were effective in handling the thermal management requirements, the cold plates were relatively large, and the additional weight on the battery became a concern.
Boyd leveraged its extensive experience with cold plate construction and began working on ways to cut down weight. After some experimentation, Boyd engineers significantly lowered battery cold plate weight by optimizing the size and shape of each cold plate for each individual battery. The new construction effectively cooled the extreme battery pack heat while reducing the overall weight by 40% from the initial design.
Once a design was finalized, Boyd’s prototyping team quickly began creating stamped and CAB brazed cold plate prototypes for evaluation.
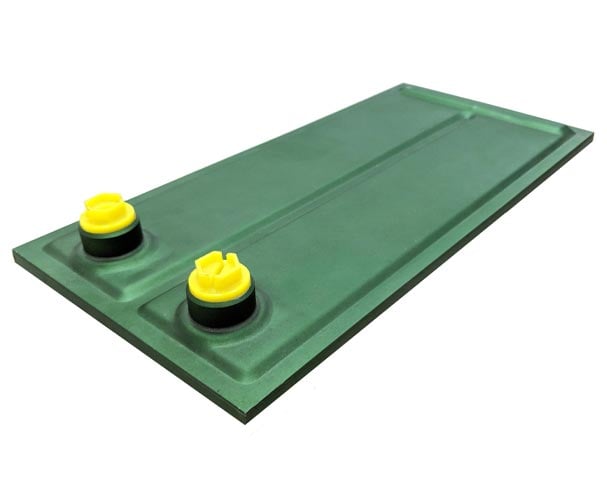
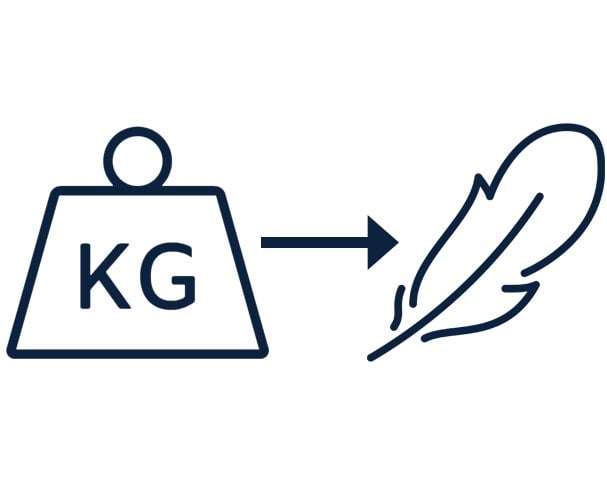
Specialty Vehicle Battery Liquid Cold Plate Results
The prototypes were extensively tested within the battery packs and proven to be highly effective at removing heat from the batteries. Ultimately, the highly-efficient and lightweight liquid cold plates were able to dramatically increase thermal performance while decreasing the overall weight of the battery pack by over 40%. The batteries will be implemented into a line of new electric specialty vehicles, and the success of the project has led to other thermal opportunities with the customer.
Have questions? We’re ready to help!