Heat Exchangers
Dissipate heat from high powered liquid cooling systems either into ambient air or into a secondary liquid cooling system through liquid heat exchangers.
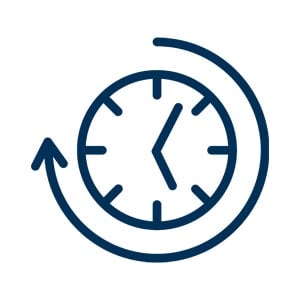
Rugged, High Reliability
Brazing assures quality system joints for long term, reliable performance.
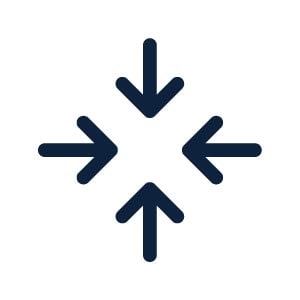
More Compact Cooling Systems
Enhanced cooling system surface area for higher cooling performance without increasing thermal system size.
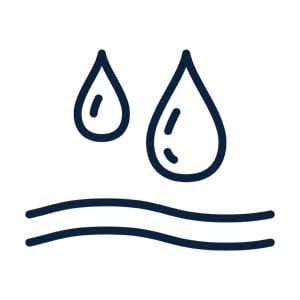
Leverage Liquid Cooling in Any System
Reject liquid cooling system heat to secondary air or liquid exhaust systems.
Boyd Aviation Solutions
(View transcript)
Liquid Heat Exchangers: Liquid System Heat Rejection
Optimize the performance of your liquid cooling system with the best-fit liquid heat exchangers from Boyd. Our liquid heat exchangers design expertise paired with our breadth of manufacturing techniques enable us to make the most of your cooling system.
Have a Question?
How Do Liquid Heat Exchangers Work?
Liquid heat exchangers absorb heat from the hot liquid flow, conduct it through the heat exchanger, and reject it into the secondary fluid flow. Heat exchangers typically employ additional surface area like stamped or folded fins to increase the rate of heat transfer.
Liquid heat exchangers’ efficiency depends on design, flow configuration, surface area, flow rates, and temperature differences between the two liquids. Engineers optimize each parameter for the specific application so liquid heat exchangers effectively transfer thermal energy between fluids.
Why Use Heat Exchangers?
To function, liquid cooling systems need a heat exchanger to reject heat. Liquid heat exchangers enables liquid systems to absorb heat while maintaining safe operating temperatures.
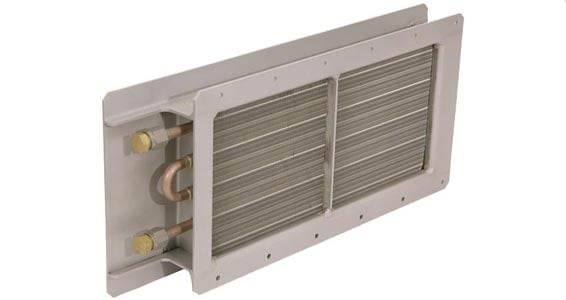
Boyd’s Liquid Cooling System Excellence
Boyd’s engineering team use their expertise to select from hundreds of custom and semi-custom liquid heat exchangers which include a variety of fin options, heat pipes integration possibilities, and other enhancements to design an optimized solution for your liquid system. Our team is well-versed in an extensive selection of fluids, oils, and coolants, and a wide range of fabrication methods to design and manufacture liquid heat exchangers to enhance your liquid system.
Different Liquid Heat Exchangers Construction Types
Leverage Boyd’s range of liquid heat exchangers construction types to optimize your liquid cooling system.
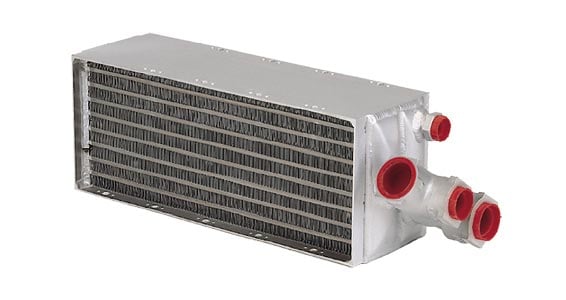
Liquid Heat Exchangers: Flat Tube Heat Exchangers
Flat tube liquid heat exchangers consist of flat tubes with extended surface channels coupled with external fins. The tubes provide additional heat transfer through a large internal surface area in contact with the fluid. Header manifolds designed for flat tube heat exchangers result in a low pressure drop that require smaller, less expensive pumps. The flat tube and extended fin structure results in an efficient, rugged, and lightweight solution ideal for challenging applications.
Our standard ES oil cooler series features aluminum flat tube heat exchangers engineered for high performance with poor heat transfer fluids such as oils and ethylene glycol/water (EGW) mixtures. Our oil coolers provide up to 2.5 times greater thermal performance per unit volume than competitive oil cooler models. Boyd’s flat tubes can be bent as tight as a 6.35 mm (0.25 in.) radius, allowing for unique, curved heat exchangers that can be further integrated into your custom system. We can add custom fittings, manifolds, paint, or anodize for extra integration and environmental protection.

Industrial
Analytical & laboratory equipment, factory machinery cooling,
plastic injection & molding equipment, chemical processing temperature control, food and beverage processing, electric discharge machining (EDM), laser equipment, induction heating.
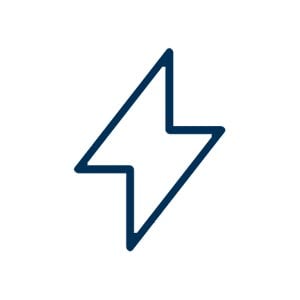
Power Generation
Power supplies and power generation stations.

Medical
Medical imaging equipment, MRI machines, dental equipment, lasers & optical equipment.
Liquid Heat Exchangers: Standard Flat Tube Heat Exchangers
Boyd’s standard flat tube liquid heat exchangers have aluminum fins and flow paths, with 3/8 – 18 NPT fittings, and pre-installed fan plate. Customers have the option of adding a fan kit with their heat exchanger, with either 115V or 230V fans. Max. operating temperature: 200°C (400°F).
Model Number | Dry Weight, kg (lbs) | Fluid Volume, mL (in.3) | # Fans in Optional Kit |
---|---|---|---|
ES0505G23 | 0.91 (2.0) | 229 (14) | 1 |
ES0510G23 | 1.30 (2.85) | 278 (17) | 2 |
ES0707G23 | 1.30 (2.85) | 393 (24) | 1 |
ES0714G23 | 2.51 (5.53) | 508 (31) | 2 |
Liquid Heat Exchangers: Brazed Plate Liquid-to-Liquid Heat Exchangers
Brazed Plate Liquid Heat Exchangers (BHE) are compact, highly efficient, and durable liquid-to-liquid heat exchangers. These heat exchangers are constructed from stacked plates brazed together that are typically corrugated to add surface area and more heat transfer. Brazed Plate Heat Exchangers’ efficient counter flow design allows 90% of the material to be used for heat transfer. These heat exchangers can be up to 80-90% smaller than a conventional shell-and-tube design. The brazed plate Liquid-to-Liquid heat exchangers construction offers a rugged, efficient, and long-lasting heat exchanger that withstands demanding environments.
Braze material and plate corrugation patterns can be configured for different operating liquids and system requirements. Our copper-brazed units are compatible with water, Ethylene Glycol based Water Solution (EGW), and other common coolants. Copper-brazed units can be operated at temperatures of up to 195°C (383°F) and pressures up to 31 bar (450 psig). Nickel-brazed Plate Heat Exchangers can use deionized water, high purity fluids, and corrosive fluids and operate at temperatures of up to 350°C (662°F) and pressures up to 16 bar (232 psig).
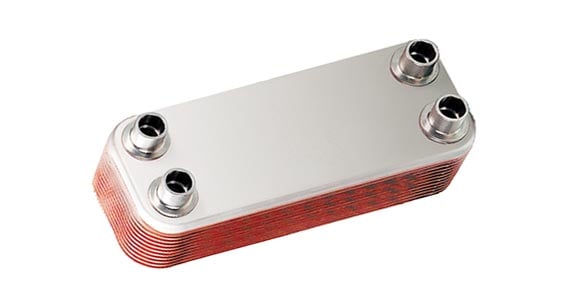
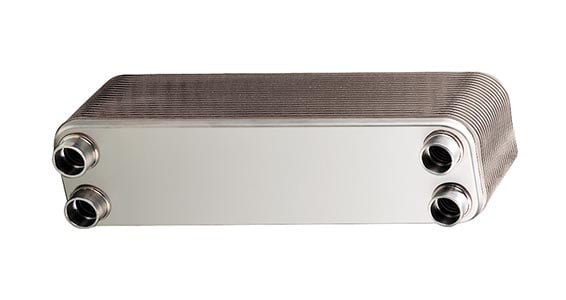
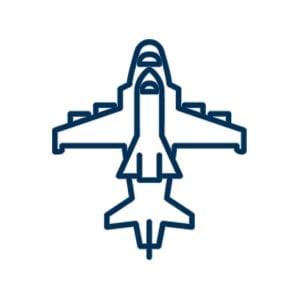
Aerospace and Defense
Oil coolers, condensers, evaporators

Industrial Equipment
Petrochemical and chemical processing, food & beverage refrigeration systems, hydraulic oil cooling, steam heaters and reboilers, condensers, smaller HVAC systems.
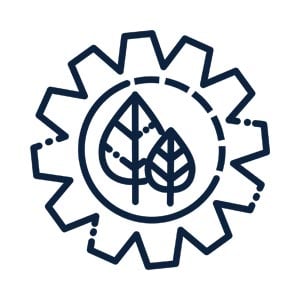
Agriculture and Construction
Hydraulic oil cooling, mining equipment, mobile HVAC systems
Heat Exchanger Recores
Heat exchanger recore or core replacements can extend the life and performance of existing thermal management systems. Heat exchanger and radiator systems installed in various industrial applications, energy processing, power generation, aerospace, defense and transportation industries are sources for efficiency improvements as technology evolves over time. Improved thermal system efficiency translates to greater energy efficiency, increased production, better yield and resource utilization, and cost savings. Maintenance and retrofit of existing installed systems provide a scalable, lower cost alternative to replacing entire thermal systems.
Boyd has decades of experience manufacturing heat exchanger core replacements for many industries that require components with high reliability and quality for maximum system uptime and minimal maintenance.
Boyd offers reverse engineering design solutions to create custom drawings that enable new production of out-of-date retrofit components.
While Boyd supports a broad range of recore applications, we specialize in commercial, military, and general aviation aircraft. Utilizing approved data and procedures, we collaborate with FAA/EASA certified repair stations for aerospace aftermarket heat exchanger recore support. Working with FAA approved repair stations, more than 100 different Boyd heat exchanger cores are available to replace OEM parts on Boeing, Airbus, McDonnell Douglas (MD), Bombardier Canadair Regional Jet (CRJ) and Embraer Regional Jet (ERJ) aircraft.
Heat Exchanger FAQs
What is an air to air energy exchanger?
An air-to-air energy exchanger transfers heat and moisture between two separate air streams, recovering energy from exhausted air to condition incoming fresh air.How does air to air heating work?
Air-to-air heating transfers heat from one air stream to another. The system uses warm indoor air to heat incoming fresh air through a heat exchanger, without mixing the two streams. This process improves energy efficiency by reusing heat that would otherwise be lost.What is the AHU air to air heat exchanger?
An AHU (Air Handling Unit) air-to-air heat exchanger transfers heat between incoming and outgoing air streams in HVAC systems. It uses exhaust air to precondition fresh air, reducing the energy required for heating or cooling and improving overall energy efficiency.How to size air to air heat exchanger?
Engineers size an air-to-air heat exchanger by analyzing system requirements, including airflow rate, temperature differential, and heat load. They consider factors like thermal efficiency, pressure drop limits, and available space. Proper sizing ensures optimal performance and energy efficiency tailored to the specific application. Contact us for help sizing your air to air heat exchanger.What is the principle use of air-to-air heat exchanger?
An air-to-air heat exchanger transfers heat between two air streams without mixing them. It absorbs heat from exhaust air and uses it to warm incoming air, improving energy efficiency and reducing the need for extra heating or cooling.How does an air-to-air exchanger work?
An air-to-air exchanger works by transferring heat between incoming and outgoing air streams without mixing them. Warm exhaust air flows through the exchanger, transferring its heat to cooler incoming air. This process efficiently warms the secondary air flow, improving energy efficiency in HVAC systems.How to calculate heat exchanger size?
To calculate heat exchanger size, engineers first determine the required heat transfer using the formula: Q = U × A × ΔTlm Where Q represents the heat transfer rate, U is the overall heat transfer coefficient, A is the heat transfer area, and ΔTlm is the logarithmic mean temperature difference. Factors such as flow rates, fluid properties, and the desired temperature change are considered to ensure optimal sizing and performance for the specific application. Need help? Contact our engineering team to size your heat exchanger.What is the formula for the heat exchanger?
The primary formula for a heat exchanger is: Q = U Ă— A Ă— ΔTlm In this equation, Q represents the heat transfer rate, U is the overall heat transfer coefficient, A is the heat transfer area, and ΔTlm is the logarithmic mean temperature difference between the hot and cold fluids. This formula helps engineers calculate the heat exchanger’s performance and efficiency.How to calculate area of heat exchanger?
To calculate the area of a heat exchanger, engineers use the formula: A = Q / U × ΔTlm In this equation, Q represents the heat transfer rate, U is the overall heat transfer coefficient, A is the heat transfer area, and ΔTlm is the logarithmic mean temperature difference between the hot and cold fluids. By substituting the known values into this formula, engineers can determine the required area for effective heat transfer.How to design a heat exchanger?
To design a heat exchanger, engineers define the requirements, including heat transfer rate, fluid types, and temperature needs. They select the appropriate heat exchanger type, such as or plate or tube fin, based on the application. Next, they calculate the necessary heat transfer area and dimensions using formulas that consider flow rates, temperature differences, and pressure drops. Engineers choose durable materials that withstand operating conditions and determine the optimal flow arrangement; whether counterflow, parallel flow, or crossflow; to maximize heat transfer. Finally, they use computational tools to simulate performance and refine the design for enhanced efficiency. Contact our engineering team for help with your heat exchanger.How to calculate efficiency of heat exchanger?
To calculate the efficiency of a heat exchanger, engineers use the formula:
Efficiency = Qactual / Qmax
In this equation, Qactual represents the actual heat transfer achieved by the heat exchanger, while Qmax is the maximum possible heat transfer, calculated based on the inlet temperatures of the hot and cold fluids.
What is the SI unit for heat exchange?
The SI unit for heat exchange is the watt (W), which measures power as the rate of energy transfer. One watt equals one joule per second (J/s). This unit quantifies the heat transfer rate in heat exchangers and other thermal systems.What is the purpose of a liquid Vapour heat exchanger?
A liquid-vapor heat exchanger transfers heat between the liquid and vapor phases of a working fluid, efficiently managing thermal energy during condensation and evaporation. It is commonly used in refrigeration systems, air conditioning, and industrial processes to maintain temperature control and enhance overall system efficiency.What is a liquid heat exchanger?
A liquid heat exchanger transfers heat between two liquid streams without mixing them. It allows one liquid to absorb heat from another through a series of tubes or plates.What are the different types of heat exchanger fluids?
Heat exchanger fluids include water for its high heat capacity, oils for thermal stability in high-temperature applications, refrigerants in cooling systems, glycol for antifreeze properties, and air for simple cooling. The choice depends on application needs like temperature range and thermal conductivity.
Learn more about some of the best fluids for heat transfer.
What are the main types of heat exchanger?
The main types of heat exchangers include double pipe, shell-and-tube, plate, and condenser/boiler heat exchangers. Each type serves specific applications and offers distinct advantages in heat transfer efficiency and design flexibility. Boyd specializes in plate, plate fin, finned tube, and condenser heat exchangers.Have questions? We’re ready to help!