The Impact of Using Different Technologies in Liquid Cold Plate Fabrication
The two biggest cost drivers in cold plate manufacturing are thermal performance requirements and annual demand, which generally thermal engineers and manufacturing engineers have little or no control over. However, you can reduce costs by understanding how roughness, flatness, hardness, surface topography, mounting features, and liquid connections specifications can all affect the cost of a cold plate. By involving your cold plate manufacturer early in the design process, you’ll be able to identify the manufacturing cost drivers and select the most cost effective design.
Most cold plates are made of aluminum but some new technologies use copper. Although copper has better thermal conductivity, aluminum is used more often because it is usually cheaper, lighter, and easier to work with. Machining copper is very difficult and expensive. If aluminum meets the thermal performance specifications, it is generally the best material to use.
Two of the most popular aluminum cold plate technologies are tubed and vacuum-brazed (See Figure 1). Tubed cold plates are usually copper or stainless steel tubes pressed into a channeled aluminum extrusion. They are cost-effective and offer good bulk heat removal for low-to-medium watt densities. Vacuum-brazed cold plates consist of two plates metallurgically bonded together with internal fin. They are available in all sizes and offer extremely high performance, making them ideal for applications where heat loads are concentrated. Labor time is limited with both tubed and vacuum-brazed cold plate technologies. For that reason, U.S. cold plate manufacturers tend to be competitive with offshore manufacturers for moderate volumes. The lower labor cost reduction from buying offshore is typically offset by shipping and customs costs, and additional inventory associated with long transport times. The threshold quantity for offshore savings is usually about 10,000 cold plates or more per year.
The biggest cost drivers for aluminum cold plates, after those mentioned above, are machining time and additional processing steps. Cold plate manufacturers typically have a cost associated with machining time which covers depreciation costs of the machine, power, supplies, and maintenance. Therefore, the longer the cold plate sits in the machine the more costly it is. Each additional processing step continues to drive the cost up.
Extrusions and Castings
To minimize machining time and drive down cost, it is best to use extrusions and casting as much as possible. An extrusion is produced by pushing metal through a die to create an object with a fixed cross-section. Dies for a new extrusion are relatively inexpensive and extrusion size is limited to about 9 inches (22.86 cm) wide. Extrusion wall thickness needs to be relatively consistent and any channels or features need to be straight.
Your manufacturer can also use a combination of extrusions and machining to reduce costs. An extrusion can be made for some of the features and then the more complicated features can be machined. Another option for prototyping purposes is to machine the cold plate for lower quantities and then, once the design is proven and fixed, make the die for the extrusion. This will help to keep extrusion costs down, provided you design the plate with the extruded features in mind.
Another option is to combine casting and machining to make cold plates. For instance, if the casting is not flat enough, a secondary operation to get the cold plate to the required flatness specification will be necessary. It is important to note that sand castings are not an option for vacuum-brazed cold plates because most alloys used have a melting temperature below the vacuum-brazing temperature. Their use is strictly limited to tubed cold plates. Obtaining quotes on the two production processes and weighing the pros and cons is recommended.
Typically, the minimum purchase quantity for an extrusion or a casting is high, so you need the right application in order to justify using these processes. Both extrusions and castings can provide significant cost savings overall.
Surface Roughness
One requirement that can add significant cost with little impact on performance is surface roughness (finish). Roughness on cold plates is the inequalities, ridges, or projections on the surface that result in an unevenness on the thermal transfer surface. Contrary to some beliefs, roughness has relatively little impact on thermal performance of cold plates. (See Figure 2). In most applications there is less than 10% surface-to-surface contact or more than 90% air gaps between the cold plate and component. A smoother surface will only slightly reduce the percent of air gaps.
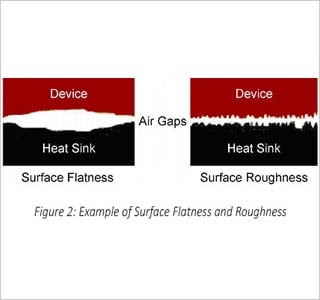
A typical machined cold plate will have a surface finish of 32-64 µin (81-163 µcm), which is sufficient for most applications. Roughness can be reduced to 16 µin (41 µcm) using a standard machining center, however this requires more rigid fixturing to reduce any potential chatter and slower speeds and feeds of the machining head. (Speed is the rate at which the cutting tool head spins and feed is the rate at which the machine head moves across the cold plate.) Reducing both speed and feed translates to longer machining center time, thereby increasing cost.
Most applications use a thermal interface material (TIM) between the component or board and the cold plate to help to minimize the gaps. A TIM should be as thin as possible, as the relatively high thermal resistance of the TIM greatly overshadows any conductivity improvements from having a smoother surface. Increasing the clamping force of the component or board to the cold plate can also help to offset a higher roughness, but it may increase the stress on the board or component. Clamping stress can also increase the impact of coefficient of thermal expansion (CTE) mismatches as the cold plate and component or board heat up.
Surface Flatness
Surface flatness has more impact on a cold plate’s thermal performance than surface roughness, as the contact area is greatly reduced if the cold plate is not flat (See Figure 2). The standard flatness specification is 0.001 inch/inch (0.003 cm/cm). Therefore, within an inch of your measurement point, the cold plate’s lowest point will not be more than 0.001 inch (0.003 cm) lower than the highest point. If your specification requires flatness better than 0.001 inch/inch (0.003 cm/cm), one way to save money is to specify a local flatness rather than a tight flatness across the whole plate. For instance, if you are mounting multiple insulated gate bipolar transistors (IGBT) on a cold plate and each IGBT requires 0.001 inch/inch (0.003 cm/cm) across the whole base plate, specify the local flatness for a single IGBT rather than requiring the whole plate to be very flat.
The flattening process of a cold plate typically involves a hydraulic press. A skim cut can be used to improve flatness. With a skim cut, the machine tool determines the lowest point of your cold plate and skims off very little metal at the lowest point and as much metal as necessary at the higher areas to achieve a flat surface. While skim cutting a block of aluminum is very easy, skim cutting a vacuum-brazed cold plate or the tubed side of a tubed cold plate is more difficult. The cooling surfaces of vacuum-brazed cold plates and tubes in tubed cold plates are typically thin in order to optimize thermal performance. If the cold plate is not flat the skim cut could be too deep and the walls will be thinned, potentially becoming too weak to hold pressure or even breaching. Alternatively, you can start with a thicker cold plate to eliminate the potential for leaks, but you’ll sacrifice some performance.
Surface Topography
Minimizing surface topography is also important in keeping costs down, particularly for board applications. Complex surface topography generally requires starting with a thick block of aluminum and machining off aluminum that is not needed. This results in high raw materials costs and excessive machining time. If topography cannot be eliminated, bundling components with similar heights on the board can reduce the machining requirements.
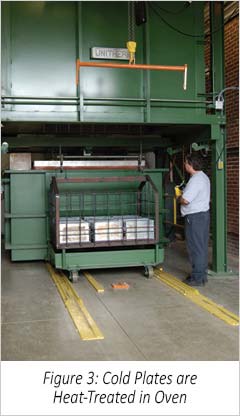
Hardness
A cast, extruded, or vacuum-brazed cold plate is very soft after processing, usually having only a T0 hardness. Cold plates must be hardened since soft aluminum is very difficult to machine and handle. To go from a T0 to T4 hardness, the cold plate must be heat-treated. The heat treat process involves bringing the cold plate up to 1000°F (538°C), letting it sit at that temperature for approximately 1 hour/inch of cold plate thickness at its thickest point, and then thermally shocking it by cooling it down very quickly (See Figure 3). One way to cool the cold plate down is to drop it directly out of the furnace and into an aqueous bath. To take the cold plate from T4 to T6, the cold plate must be artificially aged. This is accomplished by letting the cold plates sit at 300°F-400°F (149°C-204°C) for 8-16 hours. T6 provides a very hard cold plate with high tensile strength, which is a typical requirement in military and aerospace applications. For most applications, however, T4 is hard enough, and specifying T6 will only add unnecessary cost.Mounting Features / Holes
Another cost adder in cold plate manufacturing is the addition of holes. One hole may add as much as $3 to the cost of a cold plate. One of the main reasons that holes add costs is that holes cannot be made in the fluid path. Therefore, for a tubed cold plate, a bend in the tube needs to be made to accommodate the hole, and each bend adds cost. For a vacuum-brazed cold plate, an island must be created in the fluid path, which also means electrical discharge machining (EDM) the internal fin. This can add quite a bit of machining time and therefore cost.
There are several types of holes. One type is a through hole, which passes from one side of the cold plate to the other. A second type is a tapped hole, which has screw threads. Since aluminum is relatively soft, tapped holes have a limited life if the components or boards are frequently changed. With tapped holes, helicoils are often used. A helicoil is a sturdy steel insert that adds strength to the threads for applications in which there is likely to be frequent component change out. Through holes are produced by a single drilling process, while tapped holes require an additional tool on the same machine set up. Helicoils require a tapped hole in order to be installed, and the helicoil installation itself is completed outside of the machining center. In summary, through holes are the least expensive and helicoils are the most expensive.
Tight tolerance of the location and spacing of holes can also drive up costs. A reasonable tolerance specification is ±0.005 inch (±0.013 cm). As with flatness, specifying local tolerances when possible will reduce cost. With big cold plates where holes can be relatively far away from each other, the tolerance becomes harder to maintain. One reason is that machine tool tolerances increase as the head has a farther distance to travel. Another reason is that there may be thermal gradients of as much as 18°F (10°C) in the machine shop, which can expand or contract the cold plate by as much as 0.005 inches (±0.013 cm). Through holes are the easiest to specify a tighter tolerance for because creation of a through hole is accomplished with a single tool operation, while tapped holes are not as easy to tolerance because making them involves two tools. Helicoils are the hardest to tolerance because the process requires a tapped hole and the helicoil itself has a tolerance. All the tolerances add up, making it harder and more expensive to manufacture. Avoiding small tapped holes will also help to reduce cost. Hole sizes of 4-40 or smaller become difficult to tap as the taps can break while drilling. In order to minimize this problem, the machine must run much slower. One way to counter tight tolerances requirements on a cold plate is to increase the size of the mounting holes in the component or board.
Liquid Connections
For liquid connections, straight threaded O-ring female ports generally work best. Other than a welded system, it provides the best sealing at the lowest cost. Plumbing connections, such as a NPT fitting, do not provide the precision needed for components such as cold plates. On a vacuum-brazed cold plate, a male fitting, such as a barbed or beaded fitting, should be avoided because it requires another operation such as welding to attach the fitting. In addition, fittings that extend beyond the cold plate need to be protected during shipment, potentially adding packaging costs. Quick disconnects should only be used when necessary because they can cost as much as $750 per pair. Quick disconnects are required on cold plates or electronics that need to be frequently replaced. They are also required for cold plates that are shipped already charged with cooling fluid. With liquid connections another consideration is the port tolerance. Usually incoming plumbing has some flex to it. A reasonable tolerance is between ±0.030 inch (0.076 cm) and ±0.060 inch (0.152 cm).
Design and Manufacturing Partnerships
Working with a cold plate manufacturer early in a cold plate’s design or being flexible on a build to print design will allow for the greatest amount of cost savings. Although the two biggest cost drivers in cold plate manufacturing are thermal performance requirements and annual demand, there are many other factors over which thermal and/or component engineers have some control. Ensuring that there is a reason for every specification, as every specification may drive up cost, will help to keep costs down. It’s important to determine when roughness, flatness, surface topography, hardness, mounting features and holes, and liquid connections specifications are necessary. In addition, it’s important to realize that there are many alternatives in not only the design, but also the manufacturing processes used, which can save hundreds if not thousands of dollars in manufacturing.
Visit our Liquid Cold Plate Section to learn more about our solutions.