Liquid Cooling Systems
Liquid cooled server and cloud data center cooling systems, industrial chillers, and medical imaging cooling systems, like MRI chillers and ultrasound or x-ray modular liquid systems, leverage our trusted 20+ year liquid cooling system heritage for reliable, leak-free thermal systems that help you achieve next generation performance and power density levels.
Boyd Liquid Cooling Technology Highlights
Next level performance CDUs reliably cool data centers and artificial intelligence. Backed by our globally redundant, trusted manufacturing capacity that can ramp and scale with demanding schedules. In-rack, in-row, liquid to liquid, and liquid to air configurations.
Combine direct liquid cooling durable cold plates with fittings and tubes to simplify cooling AI servers, CPUs, GPUs, and networking applications. Benefit from Boyd’s decades of trusted manufacturing expertise, scalable global capacity, and reliable designs that maximize service efficiency.
Bring exceptional cooling performance direct to the heat source with Boyd’s highly durable liquid cold plates. Boyd cold plates are designed and manufactured with high reliability in mind from redundant production across three continents.
Data Center Thermal Management and Engineering Solutions
(View transcript)
How to Cool a Data Center with an In-rack Liquid Cooling System
(View transcript)
Enterprise Solutions
Delve into the breadth of Boyd’s solution portfolio for data centers, hyperscale computing, and other rack-based solutions in our interactive 3D tool.
Liquid Cooling Solutions: Innovative and High-Performance Systems and Components
Electronic devices are ever more powerful, and society is increasingly more connected with continual improvements in latency driving further compute and smart device functionality adoption into new and different applications. Liquid cooling systems are now prevalent across most advanced performance industries as the most compact, sustainable, and efficient method to cool high density heat loads to enable this continual increase in power density. These systems leverage the higher heat capacity of liquid, which absorbs and transports heat at a high rate very efficiently as compared to air cooling or solid conduction. Advanced cooling systems transfer and dissipate extreme heat at a high rate, enabling high compute performance and power density levels that cannot be solved by traditional air-cooled systems.
Have a Question?
High Reliability for Peak Performance with Sustainability in Mind
Boyd’s high reliability liquid cooling is applied at the system, enclosure, device, and component level with direct liquid cooling (DLC). Our solutions range from complex liquid cooled server systems that integrate multiple technologies to cool the largest, most demanding hyperscale compute cloud data centers in the world to compact cold plates that bring cooling directly to the silicon or power heat source with direct liquid cooling.
Increase performance efficiency, optimize energy use, maximize energy recovery, and increase reliability across all thermal system levels to minimize or remove waste, maintenance costs and downtime for a sustainable, lower total cost of cooling system ownership.
For those worried about introducing liquid into advanced electronic systems, Boyd’s liquid cooling systems have been installed in the market for decades with 20+ years of reliability data that drives continuous improvement in system design and test procedures. We offer 100% in-line thermal testing for high reliability, worry-free, leak-free liquid solutions.
Learn about Boyd’s solutions in the sections below:
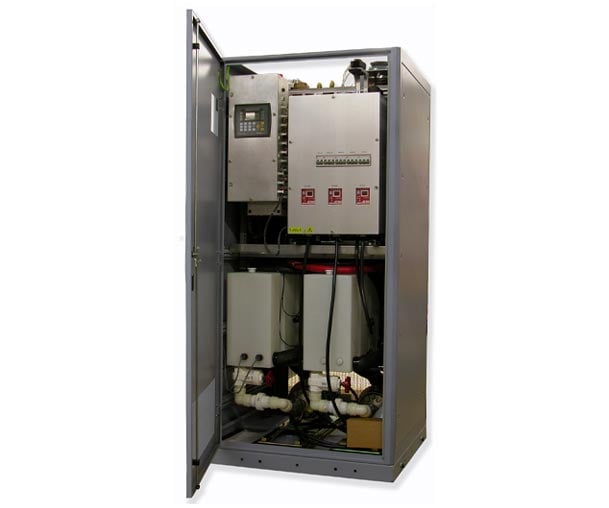
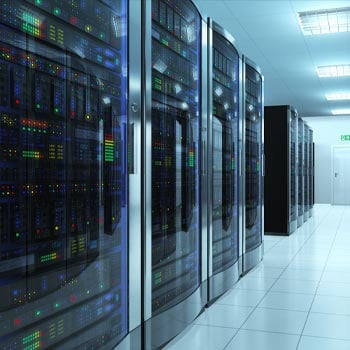
Cloud
Liquid cooled servers, data center cooling systems, and direct liquid cooled (DLC) GPUs and CPUs maximize compute density and maintain peak performance with minimal latency more sustainably with more reliable uptime. Boyd’s liquid cooling system design cycles accelerate time to market.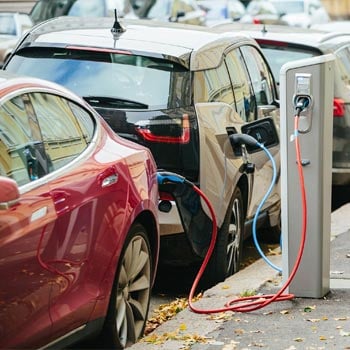
eMobility
Lightweight, ruggedized, compact liquid cooling systems extend battery range and accelerate charge cycles to differentiate new EV models and boost consumer adoption. EV battery cold plates, power conversion liquid cooling, inverter cold plates, and low profile telematics cooling.
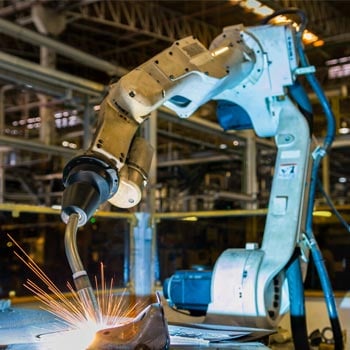
Industrial
High power density industrial equipment requires rugged, high performance liquid cooling systems. Power electronics cooling, IGBT liquid cooling, inverter cooling, IGBT direct liquid cold plates, semiconductor liquid cooling systems, battery storage liquid cooling.
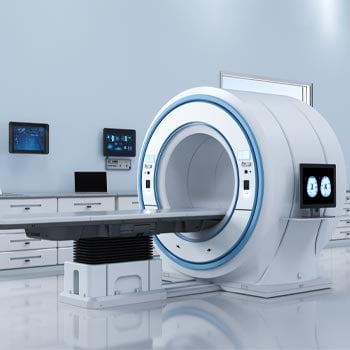
Medical
High reliability medical equipment cooling solutions. Boyd’s thermal management solutions for medical products include CT scanner liquid cooling, MRI cooling, UV light and laser cooling solutions, x-ray thermal management, medical chillers, and ultrasound thermal systems.
Liquid Cooling System Units
Boyd’s Liquid Cooling Systems undergo extensive flow network analysis using our proprietary design software powered by decades of empirical data. Meaning our thermal design engineers and system architects achieve a validated, on-specification thermal design much faster for shorter design cycles. We test each cooling system to ensure expected performance and system behavior. Our flexible development model ranges from a heavy to light touch depending on your support needs. We adapt these liquid cooling systems for new applications in high performance industries, that need to transition to the high-capacity thermal performance of liquid systems.
Smarter Liquid Systems
Boyd’s liquid systems, like coolant distribution units and recirculating chillers, incorporate detailed system intelligence to and from individual sensors, pumps, joints, and operating software for complete intelligent system behavior that maximizes sustainability and reliability. Efficiency is planned throughout the entire product lifecycle including packaging, installation fixtures, and quick service features that assure product integrity through shipping, maximize assembly throughput and minimize service time with hot-swappable quick disconnects.
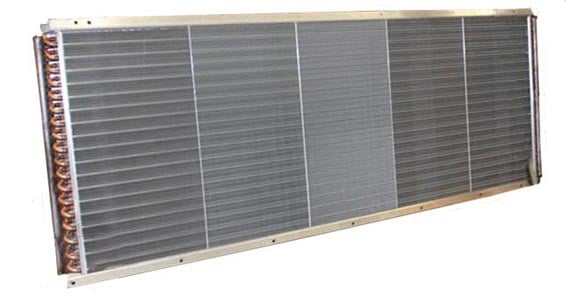
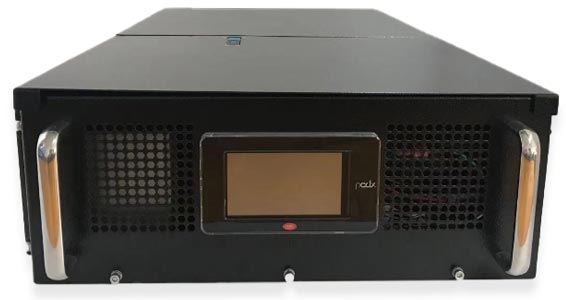
Coolant Distribution Unit (CDU)
Apply the high heat capacity of liquid cooling in liquid systems, chillers, coolant distribution units (CDUs), cold plates, and heat exchangers.
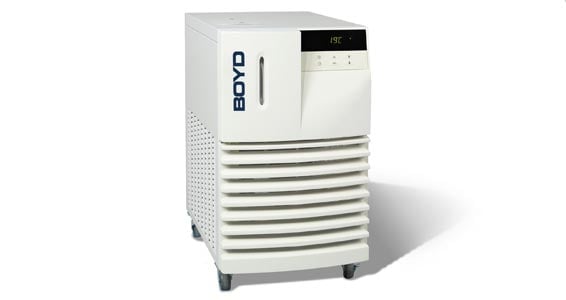
Chillers
Boyd chillers are designed for flexibility with a wide variety of available pumps, controllers, monitors, and additional safety features to cool high thermal loads while optimizing operating costs, resource utilization, and maintenance time and fees. Cool as low as -80°C or up to 50 kW cooling capacity.
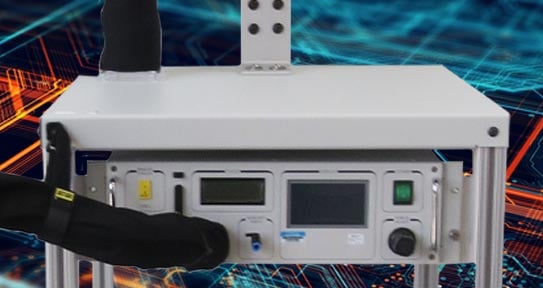
Thermal Control Unit
TCUs are complete units that maintain tight temperature profiles for a device under test in the semiconductor industry. Thermal Control Units enable rapid and stable test conditions to reliably streamline test cycles.
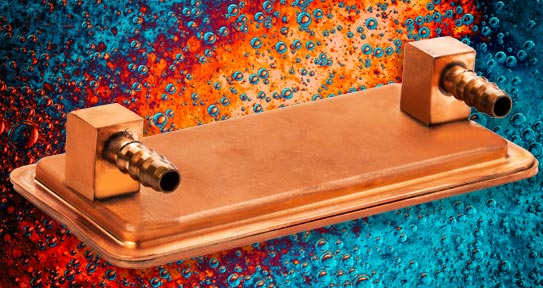
Pumped Two-Phase Cooling Systems
Pumped Two-Phase (P2P) Liquid Cooling combines the speed of pumped liquid cooling with the added heat capacity of two-phase cooling into a single advanced system. P2P are ideal for towards cooling high heat flux components quickly and reliably.
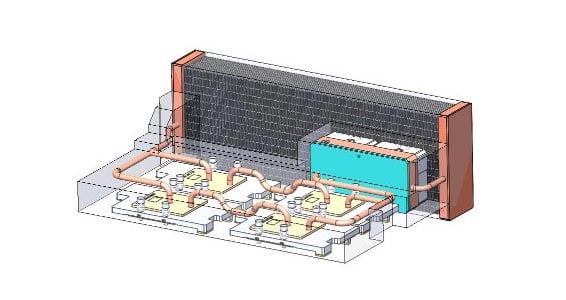
Liquid Assisted Air Cooling (LAAC)
In some systems, a liquid cooling loop cannot be utilized directly and requires the loop exchanges the heat directly to the air stream. In these cases, the Liquid Assisted Air Cooling (LAAC) is used to remove high amounts of power from the chips while rejecting the heat immediately into the air stream. This liquid assisted cooling offers customers the ability to cool the latest chips available in the market.
Liquid Cooling System Service
We stand behind our liquid cooling systems and expect them to perform reliably for you over many years. Achieving this long tenured, reliable performance does require regular maintenance to assure peak performance.
We’re responsive to customer support needs ranging from spare parts fulfillment, system service, and repair solutions. Globally available service operations and factory-certified technicians provide rapid, effective, and affordable service to minimize system maintenance downtime.
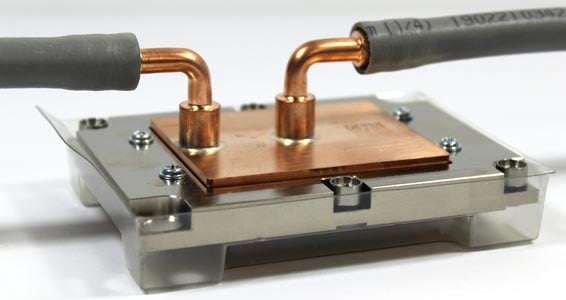
Liquid System Components
Liquid Cooling Components are a part of a complete liquid cooling system. Liquid cold plates and liquid cooled chassis absorb heat into a liquid cooling system as the primary direct liquid cooling interface between the liquid system and heat sources, while heat exchangers and radiators reject heat into ambient air or a secondary liquid cooling loop. These components determine how much heat a liquid cooling system can absorb or reject as the first and last processes in a liquid cooling cycle. Direct liquid cooling interface and heat rejection significantly impacts system effectiveness, efficiency, and performance, so they require significant design consideration.
Liquid Component Design and Optimization
Boyd Engineering excels in cold plate and heat exchanger design optimization with accurate performance simulation that accelerates our design cycle.​ We’re experts at developing and manufacturing high quality, compact liquid cold plates and heat exchangers that meet your system requirements while reducing weight and complexity. With hundreds of liquid cold plate and heat exchanger options and configurations using a variety of fabrication methods, Boyd can quickly help you optimize how your liquid system interfaces with your heat sources.
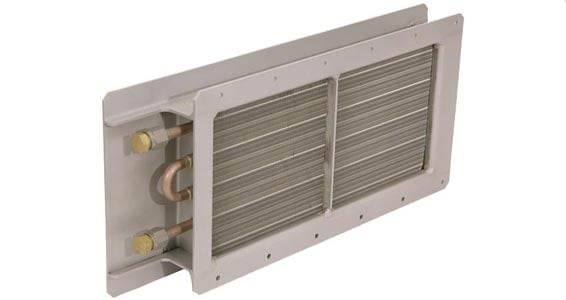
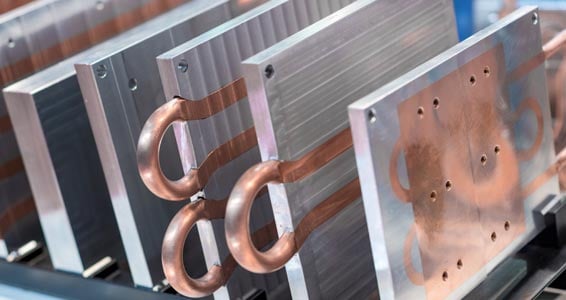
Liquid Cold Plates
Maximize thermal system efficiency and reduce total operating costs with optimized liquid cold plates. Creative direct liquid cooling designs boost turbulent flow and feature customized skylines to maximize heat source interface. 100% in-line leak testing assure reliability for EV battery cooling, advanced compute chip cooling, radar cooling, and direct liquid cooling.
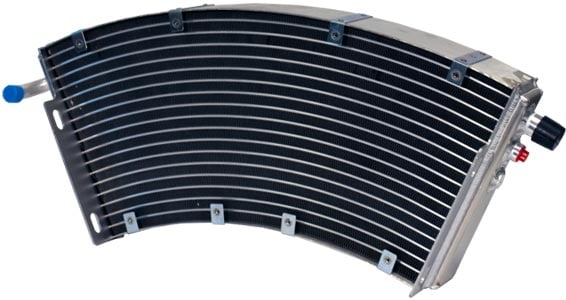
Liquid Heat Exchangers
Heat exchangers (HeX) transfer heat out a liquid cooled system, either to another liquid cooling system (Liquid to Liquid) or to an air-cooled system (Liquid to Air). Liquid heat exchangers improve complete liquid cooling system efficiency by providing high surface areas for liquid paths to reject or absorb heat.
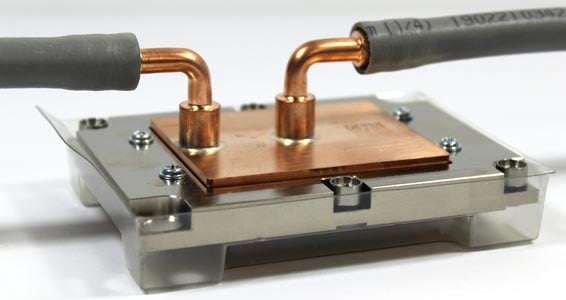
Liquid Cooling Loops
Liquid cooling loops combine direct liquid cooling cold plates with fittings and tubes to connect to pumped liquid systems to cool high-power electronics. Terminate loops with quick disconnect (QD) fluid couplings for full hot swap ability between electrical modules to maximize service efficiency.
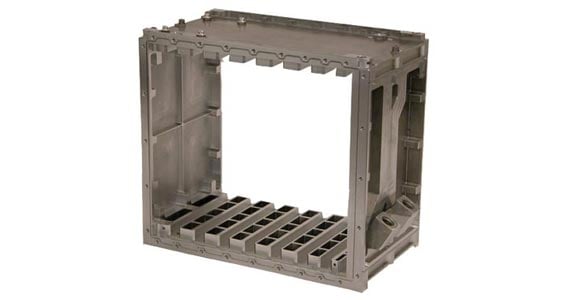
Liquid Cooled Chassis and Enclosures
Turn structural enclosures and chassis into liquid cooling system components. Liquid flow paths within walls can be as simple as tubes bonded to the structure or have complex internal geometries that optimize liquid contact area, flow rate, and pressure drop.
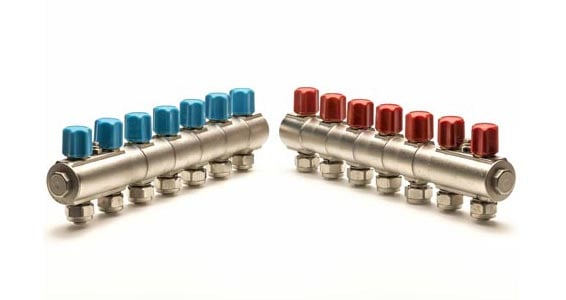
Manifolds
Accelerate installation and service with manifold quick disconnects to join liquid loops to the liquid system. Valves and sensors assure system function and controls for particle size prevent clogging and leaks. Effluent is filtered to eliminate clogging particles. Each manifold is fully tested to provide each connection with equal flow and assure zero lifetime leaks.
Have questions? We’re ready to help!