Liquid Cooling Loops
Combine durable direct liquid cooling cold plates with preassembled fittings and tubes to quickly and reliably connect to CDU manifolds for artificial intelligence processors.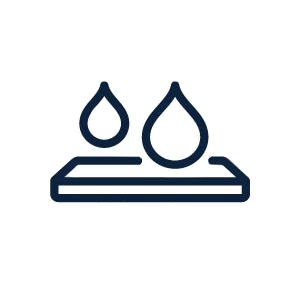
100% Leak Tested Thermal Performance
100% thermal and flow testing and validation of liquid cooling loops.
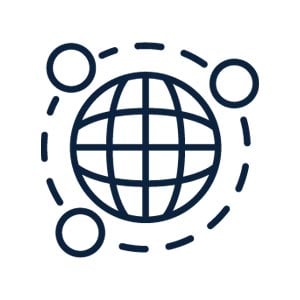
Redundant High Volume Global Fabrication Sites
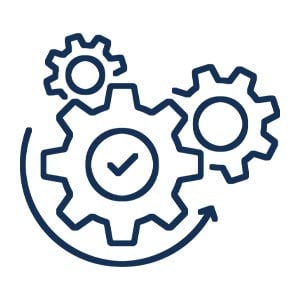
Agile Design, Ramp, and Scale Production
Leverage our reference designs to quickly build a liquid cooling loop for your specific requirements.
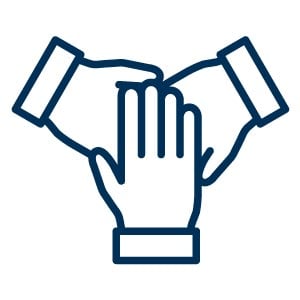
Meet and Exceed Next Gen Cooling Requirements
Prepare for architecture updates through our silicon partnerships.
Boyd Liquid Cooling Loop and Cold Plate Reference Designs for Latest Chips from
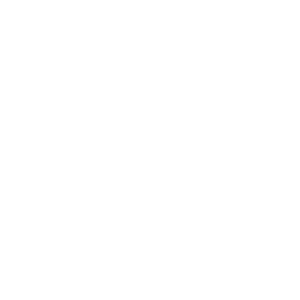
NVIDIA
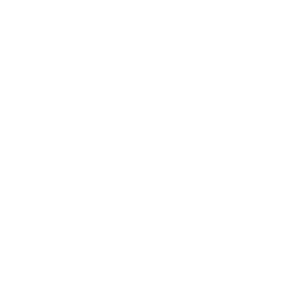
Intel
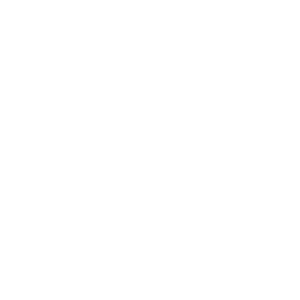
AMD
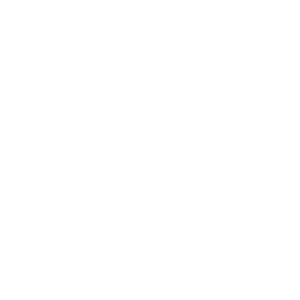
Broadcom
How to Cool a Data Center? Liquid Cooling System Solutions
(View transcript)
How to Cool a Data Center with an In-rack Liquid Cooling System
(View transcript)
What are Liquid Cooling Loops?
A liquid cooling loop is a specialized assembly with one or more cold plates connected with a single inlet port entering the enclosure and a single outlet port. Liquid cooling loop fittings and tubes are designed to quickly and reliably connect to coolant distribution unit (CDU) manifolds in a complete liquid cooling system.
As next generation processors develop, especially in data center, cloud, and artificial intelligence applications, each heat source or processor requires its own cold plate to meet high performance specifications. Common liquid cooling loop configurations serve two, four, six, eight, or more processors.
Boyd’s liquid cooling loops, direct liquid cooling cold plates, CDUs, and manifolds are all designed to optimize performance in harmony as a liquid cooling system with ultimate reliability. Existing Boyd liquid cooling system designs are available for all major processors, making them efficient plug and play liquid cooling systems for any data center or AI installation.
Have a Question?
Why Use a Liquid Cooling Loop?
Liquid Cooling Loops offer several advantages over using individual liquid cold plates and heat sinks. A single inlet and outlet port simplifies installation by enabling a top-down assembly process. Board maintenance is easily and readily accessible, and because Boyd’s liquid loops are hot swappable, efficient.
By using a one-to-one ratio for liquid cold plate to devices, system designers can focus on optimizing the mechanical attachment and reducing thermal interface resistance from the thermal interface material, maximizing thermal performance.
Why Use Liquid Cooling Loops from Boyd?
From design concept to complete product validation, Boyd’s exceptional quality and expertise can elevate your next liquid cooling loop project. We excel in rapid designs, high quality manufacturing on three continents, 100% testing, and manufacturing at scale to support demanding specifications, requirements, and launch schedules.100% Leak Tested and Exceptional Quality
Performance
Boyd 100% tests thermal and flow performance of our liquid cooling loops. We’ve had over 15 years of experience designing and fabricating liquid loops for exceptionally demanding high performance computing systems and cloud compute architectures.Brazed Joints
Boyd’s copper brazing expertise and fixture design capabilities provide high volume scalability without affecting braze joint quality. Many other cold plates on the market feature multi-piece assembled designs screwed together which are prone to leaks. Our cold plate brazing process creates the mechanical equivalent of a one-piece design for ultimate durability, quality, and reliability.Quick Disconnects (QDs)
Boyd builds loops using quick disconnects with a deep working history and knowledge of custom quick disconnects and Universal Quick Disconnects (UQDs). Our flushing and drying process ensures customers have clean loops with no particles over 100 microns which can cause QD leaks. Boyd’s liquid cooling loops are delivered free of any residual coolant, which is ideal for filling with coolant during commissioning.Nitrogen Testing Hermetic Seals
When liquid cooling ports are terminated with quick disconnects, which are required in cloud compute applications, Boyd uses a hermetic seal to pressurize the loop with nitrogen. This extra quality check leverages shipping time and receiving pressure check to ensure no leaks. All QD’s are individually leak tested before assembling to a loop.Reliability Testing
Leverage our in-house test lab to ensure long-term reliability and performance of your liquid loop. Our in-house capabilities include temperature cycling, power cycling, thermal shock, shipping tests, and more. We have also supported certification to UL / IEC 62368-1 which requires 2 weeks soak with coolant at 85°C and then hydrostatic pressure test at three times the specified operating pressure.Design Options
Most of the design load of a cooling loop is the cold plate. By eliminating this design stage, we can significantly shorten loop development when we use Boyd reference design cold plates. We have LCP reference designs for some of the latest AMD, Broadcom, Intel, and NVIDIA chips. Boyd has developed durable cold plates for CPU, GPU and Switch chips in addition to memory, optical transceivers, power modules, solid state drives, and other support chips. We leverage our extensive liquid cooling expertise to build reference designs with straight, impinged, or high flow impinged style liquid cold plates. Boyd will mix and match our existing designs to build an appropriate liquid cooling loop. While we typically see loops between 2 and 4 cold plates, we’ve produced loops that include up to 16 cold plates.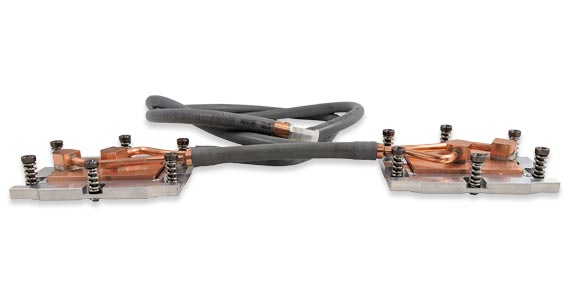
Optimize for Your Specific Installation
Boyd’s engineering and design team utilize flow network simulations to determine the right operating point based on the coolant distribution unit and manifold selection. From there, the team can design appropriate liquid cold plates, tubing, and fittings to meet your performance needs. From there, the team can design-in appropriate liquid cold plates, tubing, and fittings to meet your performance needs.
Have questions? We’re ready to help!