Metal Fabrication
Boyd complements polymer forming and precision converting with metal fabrication capabilities to develop comprehensive sealing, thermal, and protection solutions.
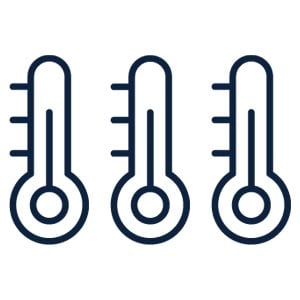
Increased Thermal Performance
Enable highly enhanced surface structures to improve thermal transfer.
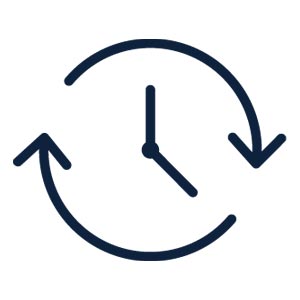
Expedite Design Cycles and Time to Market
Leverage our expertise and experience to prototype and hone designs faster, helping you beat competition to market.
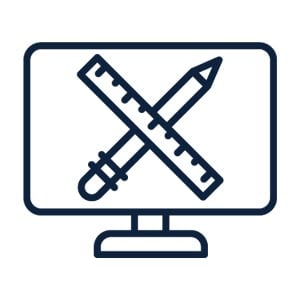
Excellent Mechanical Stability
Increase overall product strength with internal joint options, even in complex structures.
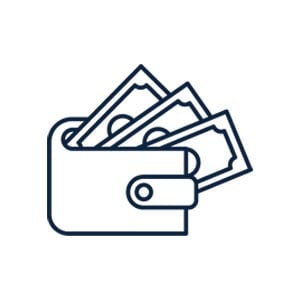
Cost Effective Solutions
Economical technologies with faster prototyping, higher production volume, and shorter lead times.
Custom Metal Solution Design with Boyd
Boyd utilizes metal and material science expertise to design and manufacture advanced cooling systems such as liquid cold plates, CDUs and chillers, heat exchangers, extreme air cooled heat sinks, thermal enclosures, and thermal chassis. Our approach to custom metal-based design begins with working to understand our customers’ performance needs, challenges, dimensional constraints, and other requirements and aligning these needs with manufacturable and scalable solutions.
Have a Question?
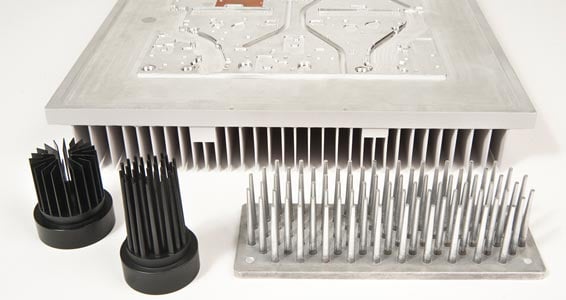
Dedicated to Quality Metal Fabrications
As with all our products, Boyd is dedicated to ensuring the quality of our metal solutions. Metal fabrication processes are controlled with our diligent quality management systems and environmental management systems. Metal solutions undergo rigorous performance testing and validation to confirm that our solutions meet or exceed your requirements. Externally qualified GD&T quality technicians leverage our fully equipped quality laboratories and specialized tools to validate quality.
Meet Application Requirements with the Right Metal Fabrication Technology
Boyd’s broad array of metal fabrication technologies enables us to prototype and manufacture complex, multifunctional metal assemblies to meet your demanding application requirements. We host a global team of over 300 engineers that work closely with customers to design optimized solutions and streamline production methods.
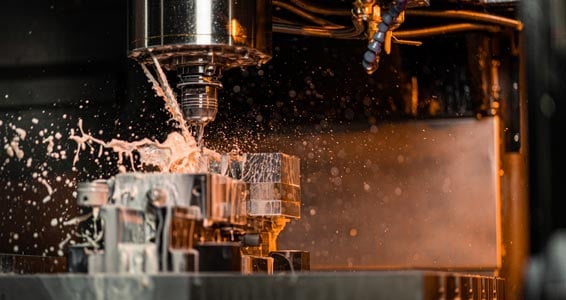
CNC Machining
Boyd’s high speed CNC machining enables us to fabricate detailed and customized geometries to meet your exacting application requirements including milling, flycutting, skiving, and other intricate features. Computer Numerical Control (CNC) machining transforms raw materials into finished products. Boyd’s world capacity and machines help turn your designs into components quickly and cost effectively.Additive Manufacturing / 3D Printing
Additive Manufacturing is gaining popularity as 3D printers advance to accommodate a wider range of materials. Boyd is on the leading edge of 3D printing and additive manufacturing for designing, rapid prototyping, and producing complex, metal-based solutions such as heat pipes, vapor chambers, liquid cold plates, heat exchangers, and heat sinks in unique geometries that are difficult to produce with traditional manufacturing methods. We print primarily with AlSi10Mg and a 6061-RAM2 powder which mimics the mechanical characteristics of Aluminum 6061-T6, the popular wrought alternative.
Brazing and Soldering
Brazing and soldering are manufacturing processes that join components by heating a braze or solder alloy between assembly components. This process is ideal for products where high-quality joints, lightweight assemblies, and high thermal and mechanical performances are required. Boyd employs in-house brazing and soldering capabilities such as vacuum brazing, salt bath dip brazing, controlled atmosphere brazing, and solder ovens to integrate components into multifunctional and complex assemblies or complete fabricated solutions. Our braze furnaces are certified to braze per AWS C3.7 Class A, B, and C. We specialize in brazed heat exchangers, liquid cold plates, heat sinks, chassis, and enclosures.
Fiction Stir Welding
Friction Stir Welding (FSW) is a solid-state joining process that uses a customized tool consisting of a probe, pin, and shoulder, submerged into two solid materials at a joint line. A spindle’s downward and rotational force generates frictional heat. As the tool traverses the surface, the probe stirs material, forming a solid-phase joint. Liquid cold plates are often friction stir welded on a high-speed vertical CNC machine. With faster prototyping, higher production volume, and shorter lead times, friction stir welding is the preferred process to manufacture cold plates for customers looking for cost-effective solutions.
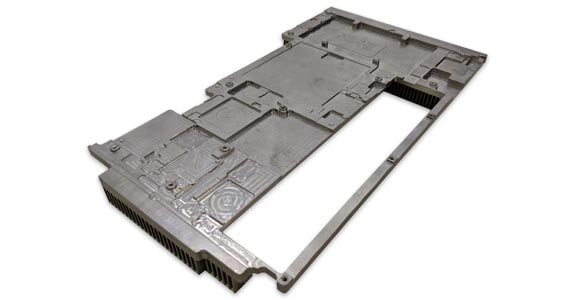
Aluminum Die Casting
Die-casting is a versatile process to produce metal parts by forcing molten metal under pressure into steel molds or dies with a high degree of accuracy and repeatability. Boyd’s decade of experience in high-pressure aluminum die casting enables us to produce aluminum die castings with tight tolerances, reducing the amount of finishing necessary for customers to achieve the desired look and performance.
Have questions? We’re ready to help!