Advanced Heat Sinks: High Performance Air Cooling Solutions
Heat sinks play a crucial role in thermal management by dissipating heat generated by electronic components in air cooled systems, contributing to safe, reliable, and efficient operation.
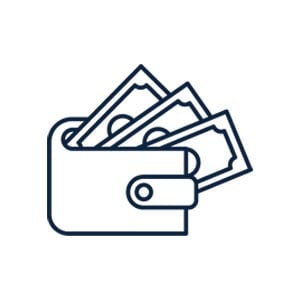
Wallet-Friendly Solutions
Cost-effective and readily available thermal solutions.
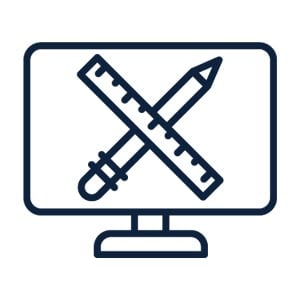
Extensive Options
Mix and match air cooling technologies for the best-fit solution for your application.
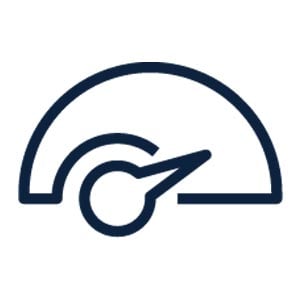
Boost Thermal Performance
Increase surface contact with advanced fin structures for improved heat transfer.
What are Advanced Heat Sinks?
Advanced heat sinks use multiple or more complex processes to produce high level heat sink customization and performance. Advanced heat sinks include bonded, brazed, zipper, or folded fin heat sink assemblies and fan heat sink combinations in addition to die cast and skived heat sinks.
Have a Question?
Why use Advanced Heat Sinks?
Advanced heat sinks leverage multiple technologies to enhance heat dissipation in an air cooled solution. Traditional heat sinks like extruded or stamped heat sinks are a mature technology well suited for lower level heat flux components. As electronic devices advance, cooling methods must also advance to meet increasing performance, lifetime, and reliability requirements.
Boyd’s Custom and Enhanced Heat Sink Solutions
Boyd’s half century of expertise in a wide variety of thermal management technologies enable us to design and manufacture heat sinks with multiple processes to produce custom, enhanced thermal management solutions specifically for your system.
Mix and Match Manufacturing Processes for Best Fit Fin Ratios
Assembled heat sinks combine several pieces into a single heat sink with thinner fins or higher fin aspect ratio compared to stamped or extruded heat sinks. Boyd’s heat sink assemblies leverage a range of fin fabrication methods to meet varying application requirements. By bonding individual fins or a fin stack onto a base, we can further customize base features, geometries, or leverage differing fin geometries to fully optimize air cooling performance.
Bonded Fin and Brazed Fin Heat Sink Assemblies
Bonded and brazed fin heat sinks assemblies consist of a grooved base with individual fins bonded into the grooves. Grooved bases are extruded, die-cast, or machined which allows for additional features like embedded heat pipes, vapor chambers, or encapsulated graphite heat spreaders. Boyd’s broad portfolio of standard extruded bases and standard fin stock allows quick design and manufacture of semi-custom epoxy bonded fin solutions as well as fully custom bonded or brazed fin heat sinks.
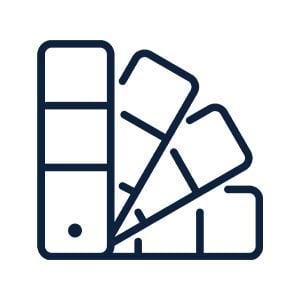
Design Flexibility
Wide range of material and fabrication options.
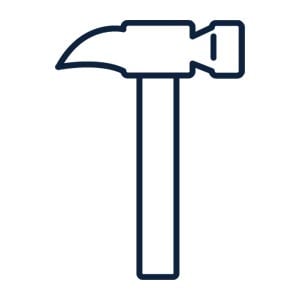
Robust Contruction
Ideal for heavy-duty applications
Zipper Fin Heat Sinks
Zipper fin heat sinks consist of a series of individual sheet metal fins that are stamped and folded together using interlocking features. Zipper fin heat sinks are an ideal air-cooled solution for high-powered forced convection applications. High mechanical stability and design flexibility of zipper fin heat sinks enable heat pipe integration, ducting, and fans or blowers for a comprehensive thermal management solution that meets specific application needs.
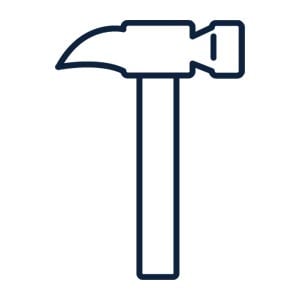
High Mechanical Stability
Joined together on both the top and bottom of the fins.
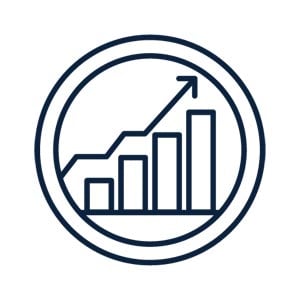
High Volume Production
With rapid manufacturing, zipper fins are ideal for volume production.
Folded Fin Heat Sinks
Folded fins provide more surface area and design flexibility than extruded heat sinks and other fabrications. Boyd’s extensive portfolio of folded fins includes over 3,000 different configurations that are manufactured for high heat transfer. Folded fins can be soldered, epoxy-bonded, or brazed as part of a custom heat sink, or utilized in a thermal system such as a heat exchanger.
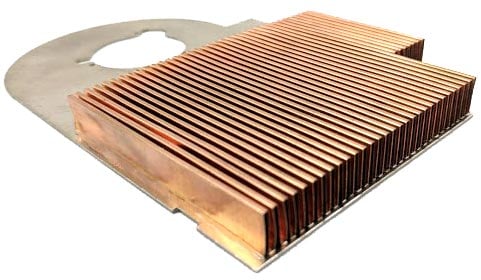
Fan Heat Sink Assemblies
Fan Heat Sink Assemblies are pre-assembled complete thermal solutions for various board-level applications. Boyd’s in-house fabricated heat sinks and axial fans allows you to mix and match components for quick semi-custom options or produce fully customized fan heat sink assemblies to meet your specific project requirements, dimensions, thermal performance, and configurations.
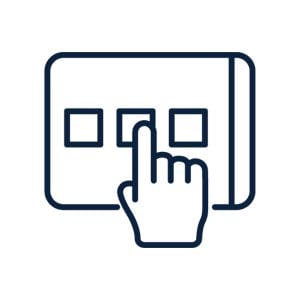
Extensive Options
Meet specific needs with our wide variety of heat sinks, mounting configurations, and fan options.
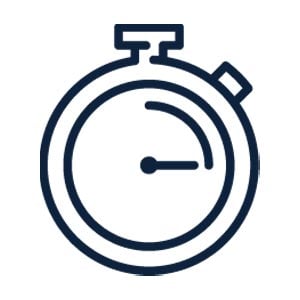
Save Time and Space
Ready-to-install, compact solutions reduce assembly time and additional hardware.
Advanced Single Piece Heat Sink Fabrication
Boyd’s advanced manufacturing methods enable us to fabricate advanced single-piece heat sinks with die casting or skiving. These processes provide a range of flexibility with a single manufacturing step where other heat sink constructions require a secondary assembly step.
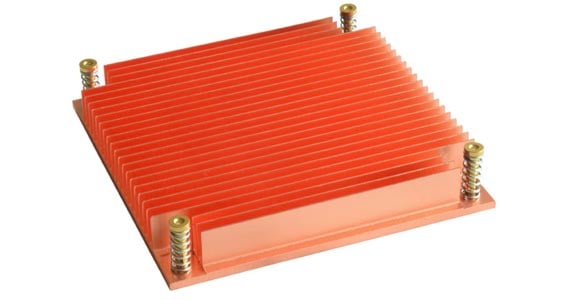
Skived Fin Heat Sinks
Skived Fin Heat Sinks are manufactured by precisely slicing the top of the base, called skiving, folding the slice perpendicular to the base, and repeating at regular intervals to create fins. The skiving process enables high fin density and thin fin heat sink geometries for greater heat transfer and thermal performance than other single-piece construction heat sinks. The breadth of skived fin geometries is ideal to create both air cooled heat sinks or augmenting liquid cold plates.
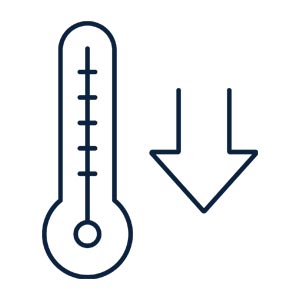
Reduced Thermal Resistance
No joints between the base and fins to deter heat transfer
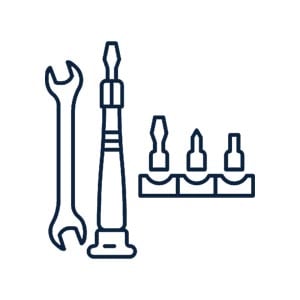
Reliable Mounting and Easy Assembly
Available with Shurlock pin attachments.
Die Cast Heat Sinks
Die Cast Heat Sinks are produced in near-net shape requiring little to no additional assembly or machining. High-Pressure Die Cast Heat Sinks produce complex shapes with a high degree of accuracy and repeatability. Leverage Boyd’s design and manufacturing expertise for a custom die-cast heat sink optimized for your application requirements while minimizing weight and die-cast tooling costs.
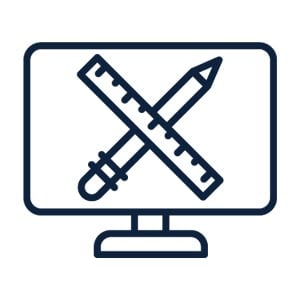
Design Flexibility
Produce complex shapes with a high degree of accuracy and repeatability.
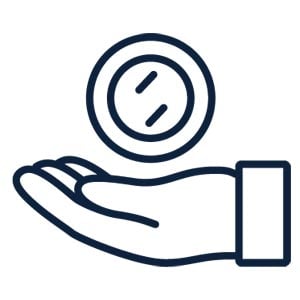
Cost-effective
Option for high volume applications.
Have questions? We’re ready to help!