What are Zipper Fins?
Zippers are a neat invention as they can uniformly connect two pieces of material into a single sheet of material. By utilizing a specialized geometry that interlocks with itself, continuous connections can be made. This makes handling a single zippered whole component easier instead of maneuvering a multitude of individual pieces. When we want to use a large quantity of thin fins on a heat sink, it would be a hassle to assemble each individual fin. This is where zipper fin heat sinks come in.
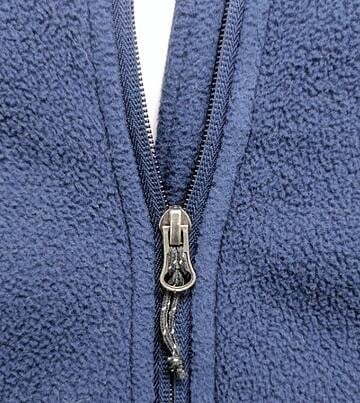
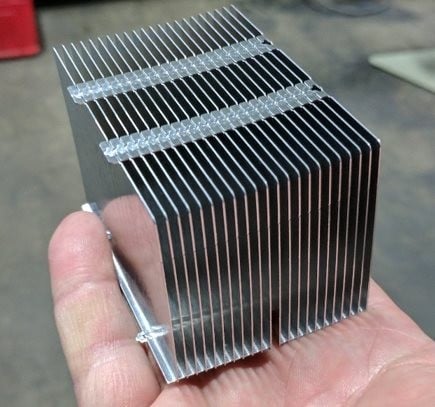
Zipper fins are sheets of metal that are progressively punched out of stock material. First the geometry of the fin is created with the punches. The length, height, and fin pitch are determined in this first set of punches. The fin thickness is defined by the thickness of the fin stock used. Secondary punching processes then fold the fin and lock them into place with the previous fin. When the fin stack has enough fins for the application this stack was designed for, it’s removed from the punching area, ready to become a full zipper fin heat sink.
Each zipper fin heat sink has it’s own design for the progressive punches for the fins. This makes zipper fin assemblies more application specific since any new zipper fin heat sink configuration typically needs a new set of punches. Zipper fin heat sinks are ideal for high volume applications as opposed to low quantity production runs since the cost of the punches will be spread out across fewer heat sinks.
How Genie Uses Zipper Fin Heat Sinks
Genie uses zipper fins stacks attached onto a base as a heat sink assembly. Genie only uses zipper fin heat sinks like this so you can easily compare a heat sink with these fins to other heat sink types. But zipper fin stacks can also be embedded with heat pipes, which generate self supporting heat sinks or larger tower heat sinks.
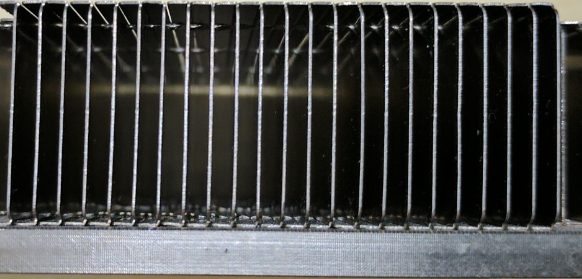
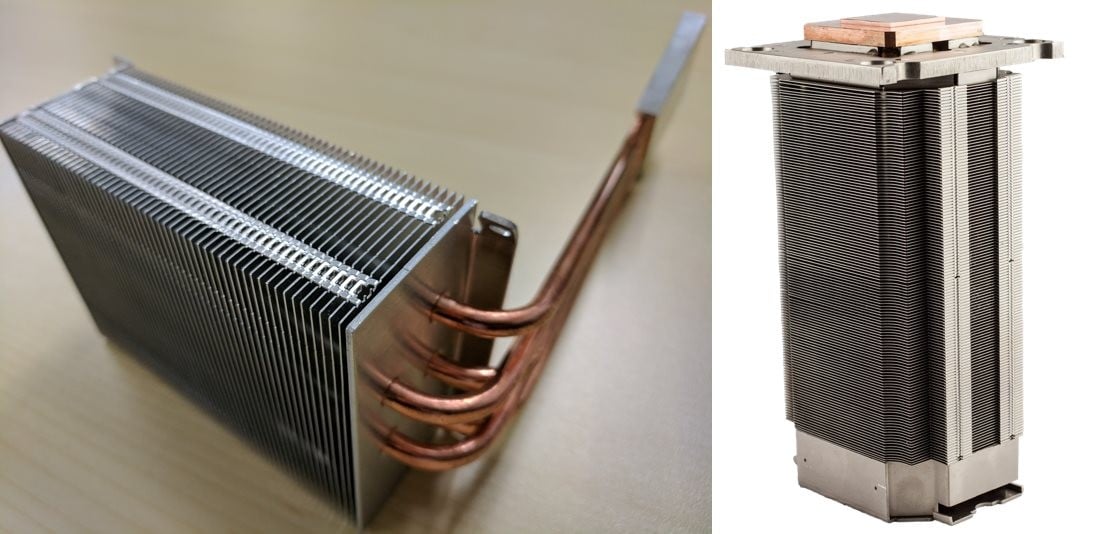
Let’s Mix and Match Materials in Our Zipper Fin Heat Sink
What’s neat about having separate components is that you can mix and match materials. You can have a copper base and aluminum fins or vice versa. Depending on your application needs, you may need an all aluminum or all copper heat sink. The material selection determines the joining method between the fins and the base. Aluminum resists soldering, so aluminum/aluminum joints are epoxy bonded. Epoxy doesn’t adhere well to copper, so copper/copper joints tend to be soldered. If mixed between the two, typically the aluminum component is nickel plated, then the assembly is soldered together.
Zipper fins heat sinks are a great heat transfer solution. While Genie uses them in the simplest form, zipper fins have a wide range of application and design flexibility. Contact Boyd Design Engineers for assistance with your zipper fin heat sink design.