An economical option for increasing surface area, folded fins increase heat transfer and performance in heat sinks, heat exchangers, and liquid cold plates.
The World of Folding
Most of the time when we hear folding, and not folded fin heat sinks. We first think of folding typical daily things like laundry or paper. Most of us don’t think or know about the awesome applications that folding has in technology. Science, technology, and engineering have embraced folding as a resource for innovations in a variety of fields. Material innovations that improve strength or flexibility of individual material sheets stem from the study of folding. Folding has improved storage for air bags for vehicles or solar arrays for space applications. Origami has helped develop heart stents to self-expand into place making heart surgery a tad less complication. Folded batteries, circuits, and foldable robotic forms are pushing the applications of electronics and robotics.
While not so flashy as paper origami, robotics, or medical applications, we can apply folding techniques in thermal management. In the thermal management world, folding metal sheets enables us to increase the amount of surface area within a given volume. Surface area is crucial for effective heat transfer.
Folding fins from a single piece also minimizes the number of components used to assemble heat transfer assemblies, such as folded fin heat sinks or larger heat exchangers. Since a fin stack is made with a single piece of material, it reduces machine set up time, assembly and handling time, and scrap material.
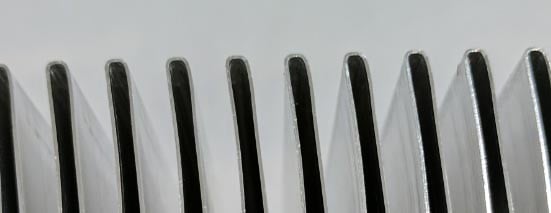
We’ve Taken Paper Origami and Gone Metal!
What Are Folded Fins?
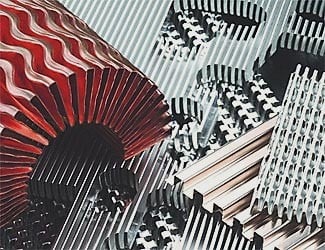
Folded fins come in a variety of materials and types. Most material that can be formed into thin sheets and easily folded can be used as a folded fin material. In thermal management, the most popular materials are copper and aluminum, since those have the highest thermal conductivities of commercially available materials. Copper and aluminum folded fins are the default materials used in Genie. Stainless steel, cupro nickel, titanium, Inconel or other nickel alloys are other common folded fin materials. Their use is heat transfer assemblies is highly dependent on the final application. You can use these materials in Genie by selecting the Custom option in the Heat Sink Design page of your project.
Folded Fins and Their Many Styles
Flat crest is the most common type of folded fin, since the crests or tops are where the fin stack is usually joined with a heat sink base. The flat crest fins maximize the amount of surface contact with the base, so the most heat can transfer from the base to the fins. These are the types of fins used in Genie. Other types of fins are available, but their use is application specific, just like materials other than aluminum and copper. These include round crest, louvered, lanced and offset, wavy, and ruffled.
How We Actually Use These Fin Stacks
Folded fins are rarely used on their own. Folded fin stacks are typically joined with a base that serves as an interface between the heat source and the fins. Genie defaults to either copper or aluminum bases, in which both have the option of embedded heat pipes. But like the fins, you can define other materials you would like to use for the base.
Mix and Match Materials of Your Folded Fin Heat Sink
What’s neat about having two separate components for the fins and the base is that you can mix and match materials. You can have a copper base and aluminum fins, or an all aluminum heat sink, or all copper heat sink, depending on what your application needs.
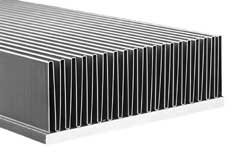
The material selection determines the joining method between the fins and the base. Aluminum resists soldering, so aluminum/aluminum joints are epoxy bonded. Epoxy doesn’t adhere well to copper, so copper/copper joints tend to be soldered. If mixed between the two, typically the aluminum component is nickel plated, then the assembly is soldered together.
Folded fins are also common components in liquid cold plates and heat exchangers since they easily increase surface area and improve system and device performance. Please reach out to our team if you need help with your folded fin application!