Skived Fin Heat Sinks: Singular Piece Solutions
Many heat sink designs consist of separate fins and base and are assembled together using an adhesive process to bond the two together. These heat sink assemblies have an added thermal resistance in the form of the adhesive layer between the base and the fins. Extrusions, which are a single piece heat sink, do not have this shortcoming of an additional interface resistance. The base and fins are one continuous piece of metal. Unfortunately, extrusions are commercially limited to aluminum. There isn’t a feasible option for copper heat sinks comprised of one single piece in this manufacturing method. Skived fin heat sinks fill this gap in manufacturability.
Precision Slicing for Generating Thin Fins
A skived fin heat sink is made from a single piece of metal, either copper or aluminum. A sharp blade precisely slices the top of single slab of the material. This process looks similar to cutting into a stick of butter. The sliced portion, while still connected to the main piece, is folded upwards to form a fin off of the base. The slicing process is repeated at regular intervals to form a series of fins which becomes a complete heat sink.
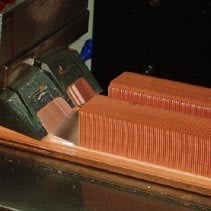
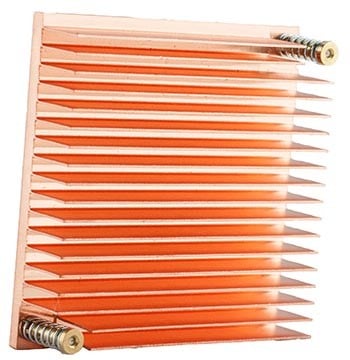
The biggest limitation to the geometry of skived fin heat sinks is the amount of force required to fold the fins up. The force required to erect these fins depends upon the thickness, flow length, and height of the fins. Genie accounts for these limitations when recommending heat sinks for you to continue customizing.
Try some skived fin heat sinks out in your design. It offers a unique blend of great characteristics of different technologies in a single package. If you need some assistance in picking the right skived fin heat sink for you, feel free to contact our Design Engineers.