Engineered Material Solutions for Medical Wearable Devices
How Boyd Adds Value to Every Layer of Device Constructions
Wearable medical devices are changing the world of health care as we know it. Innovations like insulin delivery devices are taking care beyond clinical settings while devices like ECG monitors give practitioners more data to make better treatment decisions. Demand for such devices is also creating significant opportunities for medical device manufacturers.
The global market for wearable medical devices was valued at around $21.3 billion USD in 2021. But that market is expected to grow quickly to reach around $196.6 billion by 2030. There are a number of contributing factors for this increase that go beyond advances in technology. Medicine in general is transitioning away from clinical settings to provide more mobile or virtual solutions that make care more accessible to patients. Societal factors such as increasing global obesity rates also indicate a future increase in demand for devices like continuous glucose monitors.
Taken altogether, medical device manufacturers have an opportunity to increase revenue and grow market share by creating the next generation of wearable devices, but there are significant challenges associated with designing and producing medical wearables. For example, skin is a difficult surface to bond to, wearable devices are often small and lightweight which restricts design freedom, different applications have different intended wear time, and devices need to be cleaned and sterilized. Thankfully, there are solutions to overcome these challenges.
Boyd helps medical device manufacturers create outstanding devices through materials expertise and unmatched converting capabilities. We add value to every layer in a medical wearable device stack-up. This whitepaper will explore each layer of a wearable medical device and how Boyd uses deep industry experience and manufacturing capabilities to help medical device OEMs enhance wearable products and achieve strategic product launch and realization goals.
Have a Question?
![Examples-of-Medical-Wearables] Examples-of-Medical-Wearables](https://www.boydcorp.com/wp-content/uploads/Resources/Technical-Papers/Examples-of-Medical-Wearables-5-737x342-1.jpg)
Decorative Overlay
The decorative overlay — or overpatch layer— encases the entire wearable device to help secure and protect it from the elements, increasing functionality and overall duration (or wear time). This is a secondary securement device, and it is up to the user’s discretion whether they would use this type of product to help anchor the wearable to the body. Decorative overlays can be made from a variety of durable, printable materials including flexible films, non-woven backings, foams, and spunlace or stretchable tech fabrics. Boyd converts these materials to exact specifications to create a custom overlay that perfectly fits the underlying device to ensure effective ingress protection. Boyd also prints onto overlay materials to add colorful designs, device usage information, patterns, or logos. This improves brand identification and enhances the user experience and overall wearable device aesthetics.
Cover Layer
The cover layer acts as the outer “skin” of the wearable to protect it from the elements, whether an overpatch is used or not. This seal is critical to the overall wearability and functionality of the sensor. The cover layer is typically stretchy and conformable in nature so that it moves as the body moves, making the device more comfortable and user friendly. The cover layer can be a converted component cut from foam or film roll stock, or a molded or thermoformed component if three-dimensional features are needed. Common materials used for the cover layer include nonwovens, foams, and tech fabrics. This material is often selected based on improving breathability for long wear time or waterproofing the wearable to protect sensitive internal electrical components, but the cover layer can also improve device aesthetics. Using a printable film or molded component, brands can create cover layers with distinctive shapes, features, and branding elements. Boyd’s cover film converting capabilities — including die cutting and digital printing — provide tight tolerance and cleanliness controls to enable greater design flexibility for medical device OEMs.
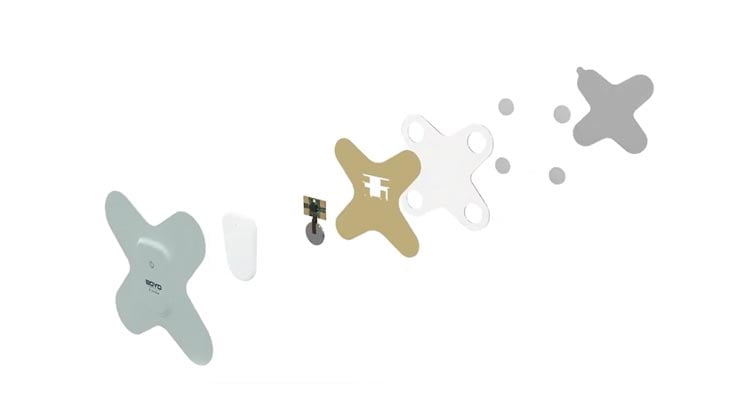
Inner Cushion Layer
Sometimes product developers want to add an inner layer to protect sensitive electronic components, either to cushion the device from potential damage or to provide additional sealing from water ingress. Boyd offers a cushioning layer that is used to protect delicate internal components and connections for more reliable performance. This layer could be a simple 2D soft foam shape, or a thermoformed or molded part if 3D features like cavities are needed. Commonly used materials include open- and closed cell foams. Utilizing raw material combinations achieves optimal performance by considering compression set and force deflection to create a soft and comfortable protective housing for the wearable’s electronics. Boyd’s materials experts guide material selection based on application requirements and the type of protection desired. We also have the converting capabilities to laminate various materials together to create a complete ingress and impact protection solution. Boyd can also incorporate through-holes to allow light from board-mounted LEDs to illuminate components like a power button and logo through to the cover layer.
Construction Adhesive Layer
Also known as the tie layer, the construction adhesive layer is used in the middle of a multilayer stack-up to bond various wearable layers together and enhance the structural integrity of the final assembled wearable device. Boyd offers a wide range of pressure-sensitive adhesives (PSAs) from 3M that require no cure time and bond with immediate strength. We also offer a range of medical-grade adhesives that help OEMs meet strict industry regulatory requirements. We are experts in converting PSAs like VHB tape and others to improve manufacturability for our medical wearable device customers. We use tight tolerance and cleanliness controls to create multi-layer constructions where precision and complexity are required.
Device Electronics
The on-device electronics are truly the heart of any wearable medical device. Components that connect power and sensors, house on-board data storage or transmit data via Bluetooth or other signals are critical for optimal functionality. These components often come in two forms: internal and external.
Internal:
The printed circuit board assembly (PCBA) is encapsulated within the wearable itself and connected to the electrode circuit via a conductive PSA.
External:
The PCBA is housed in a plastic module and is connected to the electrode circuit via snap connectors.
In most cases, OEMs produce their functional electronics components themselves. But for both types of construction design, Boyd integrates those electronics components (batteries, PCBAs, connectors, etc.) within the layers of the biosensor device, protecting it from shock, strain, and water ingress. We offer value-added assembly processes to ensure good conductivity and avoid damage to sensitive components. This also helps shorten project timelines and streamline production processes for our partners.
Electrode Circuit
The electrode circuit is the layer that connects stick to-skin electrodes to the device electronics. These circuits can be made in several different ways, either with flexible etched copper traces, or using conductive inks that are printed on one or both sides of the carrier layer to create a circuit. Conductive films can also be used to create simple circuits, and traditional snap connectors can be added if device electronics are external to the wearable. Using flexible materials helps the device move with the user’s body to ensure optimal functionality and comfort. Boyd offers custom printed flexible circuits that use conductive inks to print intricate circuit patterns onto carrier layers. With our subassembly capabilities, we can also bond functional electronics into the printed electronics layer using an electrically conductive adhesive system.
Skin Contact Adhesive Layer
The skin contact adhesive layer is the most critical layer in the wearable stack-up. This layer features highly engineered, biocompatible stick-to-skin adhesives that attach the wearable directly to the body. Common types of skin contact adhesives include acrylic adhesives, hybrid rubber adhesives, silicone adhesives, and hydrocolloids. The specific type of adhesive used is based on wear time, ease of removal, skin sensitivity, proximity to wounds, and other application factors.
The most commonly used stick-to-skin adhesives are acrylic and silicone:
- Acrylic – Better for longer duration wearables, provides good bonding to a wide variety of skin types, these adhesives can’t be too aggressive or they could damage skin.
- Silicone – Much gentler bond between the adhesive and the skin, better for short-term wearables, neonatal and geriatric patients.
Boyd offers a range of stick-to-skin tapes that require no cure time. With immediate strength, they stick directly to the skin, holding the sensor in place on the body while maintaining continuous direct contact with the skin. Our materials experts offer guidance on adhesives to ensure the optimal material for a given application.
The skin adhesive is typically combined with a backing layer made of conformable polyethylene terephthalate (PET) or polyurethane (PU) film, non-woven spunlace (PET or PU), or a soft foam layer, either open or closed cell, depending on if breathability or water resistance is desired. Boyd works with different device construction types, including those with a film or foam backing, or ones that feature a skin adhesive only with no backing.
Conductive Electrodes
Traditional hydrogel electrodes are thick, gel like polymers with high moisture content and added minerals to provide electrical conductivity through the thickness of the pad. Specific hydrogel formulations are selected based on the nature of the application, such as sensing or stimulating, or other wearability factors. Common types of conductive electrodes include conductive hydrogels, open- cell foam pads with conductive gel, or electrically conductive skin adhesives. Boyd offers a wide range of hydrogel electrode products that are combined with medical-grade adhesive tapes and converted into the direct skin contact layer.Delivery Liner
The delivery liner is a medical-grade carrier that protects the skin contact layer and aids in applying wearables to patients. Boyd offers a range of medical grade liner materials, including kraft paper and plastic films, that can be supplied in sheet or roll form. We customize liners to add pull tab features, oversize liners, split liners, or folded liners to make removal and application faster and easier. We also print onto liners to add branding elements, application instructions or other safety guidelines to improve the user experience.
Working With A Global Leader in Medical Device Manufacturing
With our materials expertise and innovative converting processes, Boyd experts enhance and add value to every layer of a medical wearable stack-up. Leading medical wearable brands choose Boyd as their manufacturing partner time and again because we have the knowledge, capabilities, capacity, scale, medical manufacturing experience, and global services to deliver reliable, high quality medical wearable devices with the greatest efficiency in the regions global customers need to consume them.
Our value-added subassembly services give you die-cut, molded, bonded, and integrated components to streamline production and create turnkey solutions for you. Our global scale gives you replicated manufactured technology from multiple ISO 13485 medical quality management system certified facilities and FDA registered sites located around the world — so we source materials and produce wearable components closer to where you will use them. We also offer clean room manufacturing and robust quality management systems with installation qualification (IP), operational qualification (OP), and performance qualification (PQ) validation protocols and rigorous process documentation. Our custom prototyping capabilities help you shorten product development lead times and accelerate product development cycles to help you accelerate product launches and get your wearable devices to market faster. We are also a 3M™ Preferred Converter, which gives us priority access to medical-grade materials and valuable resources for designing and testing wearable devices.
By working with Boyd, medical wearable device manufacturers save time, control costs, streamline production processes and enhance products to create the next generation of wearable medical device innovation.
Have questions? We’re ready to help!