Vapor Chambers and Assemblies: Passive, High Conductivity
Vapor chambers (VCs) leverage high heat transport capabilities of two phase cooling in a planar format. This makes vapor chamber assemblies ideal components when spreading high heat densities or heat loads across a larger surface.
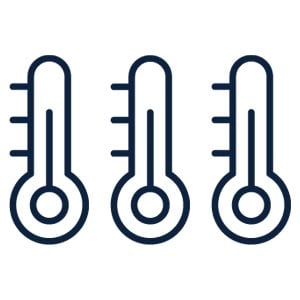
Dissipate High Heat Densities
Quickly and uniformly spread heat from densely packed heat sources with two phase heat transport.
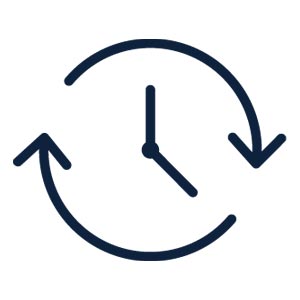
Longer Product Lifetimes
Leverage up to 20 years of consistent, passive heat transport without thermal performance degradation
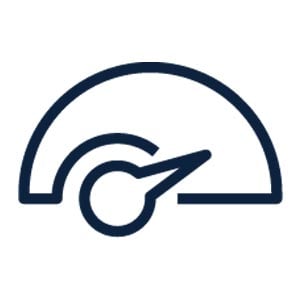
Highly Efficient
Increase heat spreading by 10 to 200 times that of solid copper, aluminum, or graphite.
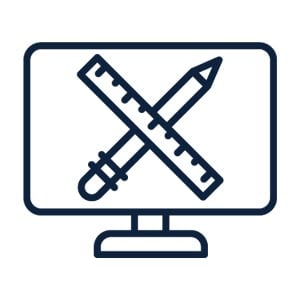
Design Flexibility
Fabricated in a variety of non-planar geometries which make them adaptable into more 3D formats.
Two Phase Enhanced Air Cooling for Power Electronics
(View transcript)
Vapor Chambers: Boost Thermals with Passive Performance
Vapor Chamber Assemblies utilize two-phase heat transport to quickly move heat within the assembly to improve its overall thermal performance. From heat spreading within the base or up into a fin structure, the versatility of vapor chambers enables unique design capabilities and can extend the effectiveness of air cooling solutions.
Have a Question?
What Are Vapor Chambers?
Vapor chambers are a thermal management component that uses two-phase heat transport to quickly move heat within the assembly to improve thermal performance.
Vapor chambers have three main parts: a thin, vacuum sealed shell or envelope, a working fluid, and a wick structure. The shell keeps the VC working fluid sealed for decades of consistent heat transport. The working fluid changes phase in the application temperature range and must be compatible with the vapor chamber shell and wick materials. The wick passively moves fluid through the heat pipe.
How Do Vapor Chambers Work?
A vapor chamber is a closed evaporator-condenser system. The sealed shell is a hollow vapor region lined with a capillary structure or wick. A working fluid at vapor pressure saturates the wick capillaries.
Liquid in the wick evaporates when the heat pipe starts absorbing heat. The vapor fills the vapor region, called the vapor space, and diffuses heat evenly across the vapor chamber. Heat distribution happens quickly, giving the vapor chamber its high thermal conductivity properties.
Cooler regions of vapor chamber shell and wick absorb heat from the vapor. The vapor no longer has enough latent energy to maintain a gaseous form, condenses back into liquid, and seeps into the wick structure. Capillary action within the wick returns the condensate to warmer vapor chamber regions and completes the operating cycle.
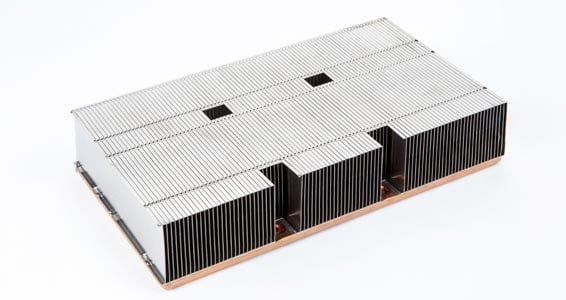
Why Use Vapor Chambers?
Vapor chambers can effectively conduct heat 10 to 50 times more than solid metal structures, possess higher through-plane conductivity than graphite for thicker applications, and requires minimal design changes. Vapor chambers evenly spread heat, so designers have flexibility in placing heat sources, the ability to increase the power of the components, or can reduce the overall size of the thermal management solution for smaller products. Smaller heat sink solutions enabled by vapor chambers improve system packaging and provide quieter operation by requiring less air flow.
Why Choose Boyd for Vapor Chambers?
Utilizing Boyd’s innovation and technical expertise in vapor chambers, customers can push their product design and performance. Our vapor chamber technologies enable cooling for next level processing speed and power in the same space. Ultra-thin vapor chamber formats keep products thin while enhancing heat spreading. Boyd is an ideal partner with broad customization options and high quality fabrication honed from decades of two-phase solution manufacturing.
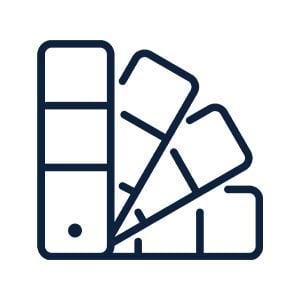
Vapor Chamber Materials
Copper-water VCs are most common with an operating temperature around 10°C to 250°C, but other liquids and materials can be used for extreme temperature ranges. Stainless steel vapor chambers provide extra strength to an assembly for additional ruggedization.
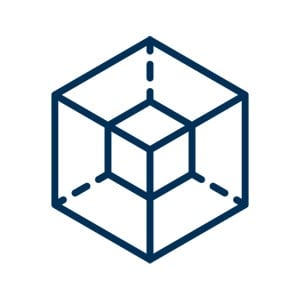
3D Vapor Chambers
Boyd maximizes cooling performance of available volumes with 3D vapor chamber assemblies. By extending vapor space into advanced, high density fin structures, Boyd creates isothermal, high surface area air cooled heat sinks for high performance cooling.
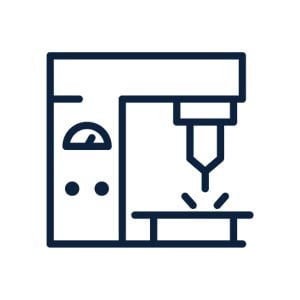
Mounting Customization
Vapor chambers can use non-planar geometries such as pedestals for varying heights and through holes. Boyd’s patented thru-hole technology enables straight and threaded holes through the vapor space region to simplify attachment hardware design.
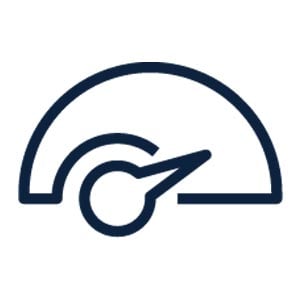
Ultra-Thin Vapor Chambers
Increase heat spreading by 10 to 200 times that of solid copper, aluminum, or graphite. With stainless steel, and copper options, Boyd designs and manufactures highly tailored vapor chambers with the thickness of a couple human hairs.
Boost Air Cooled Heat Sink Performance
Boyd integrates vapor chambers into specialized air cooled heat sinks to improve heat distribution to each of the fins, improving the overall performance of the heat sink. Typical copper-water sintered powdered wick provides high-heat flux heat dissipation, with some configurations reaching over 300 W/cm2. Customers can improve air cooled heat sink performance up to 30% when compared to typical aluminum or copper base spreaders. Leveraging vapor chambers includes all the benefits of added thermal performance, freeze/thaw resilience, and ability to withstand military shock and vibration standards without sacrificing the reliability of the assembly.
Have questions? We’re ready to help!