Air-Cooled Chassis and Enclosures
Combine Mechanical Support and Protection with Thermal Management.
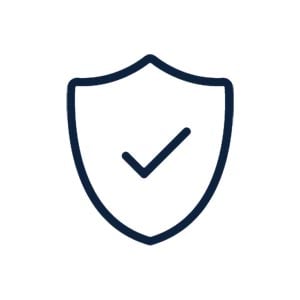
Protect Sensitive Equipment
Seal off electronics within an enclosure to protect against environmental contaminants, while still managing thermal performance.
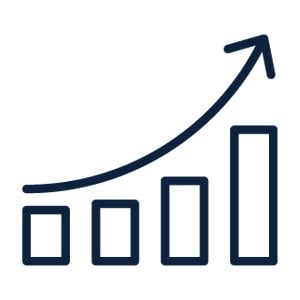
Enhance Mechanical Strength and Thermal Performance
Leverage the added strength of a chassis while using it to remove heat from high-heat systems
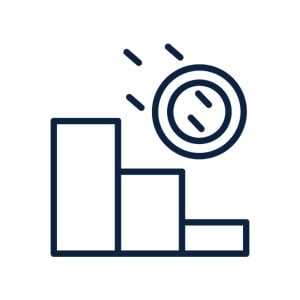
Reduce System Complexity and Cost
Integrate thermal and mechanical systems into a single component for simplified assembly and reduced costs.
Air-Cooled Chassis and Enclosures: Reduce Application Size, Weight and Power Consumption
Air-cooled chassis play a pivotal role in contemporary engineering practices to meet evolving size, weight, and power (SWaP) critical requirements. These Integrated enclosures or chassis are engineered with advanced thermal management technologies, addressing the challenges posed by stringent application requirements.
Popular fabrication methods include aluminum die casting, sheet metal bending, welding, dip brazing, and vacuum brazing as well as integrating two phase or graphite heat spreading technologies such as heat pipes and k-Core encapsulated graphite.
Creative engineers are more frequently incorporating heat spreading, thermal joints, and other technologies into enclosure designs so that these enclosures and chassis act as both a structural and thermal solution to replace traditional, mechanical-only enclosures.
Have a Question?
What Do Air-Cooled Chassis and Enclosures Do?
Air-Cooled Chassis and Enclosures integrate air cooling features like heat sinks, heat spreaders, or fins acting as both mechanical protection and thermal management solutions.
Have questions? We’re ready to help!