Shock and Noise, Vibration, Harshness Solutions
Noise, Vibration, Harshness (NVH), and shock from extreme environments can wear down mechanical and bonded joints, mating surfaces and device ruggedization or negatively impact end customer satisfaction with unwanted noise. Integrating components that effectively absorb, prevent or distribute this extra, intermittent energy enables smoother, quieter, more reliable performance by end users.
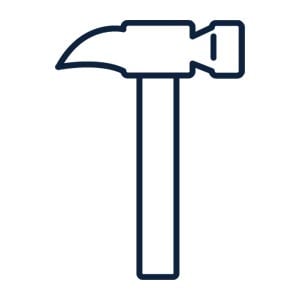
Ruggedized Protection
Protect against vibration that degrades the user experience.
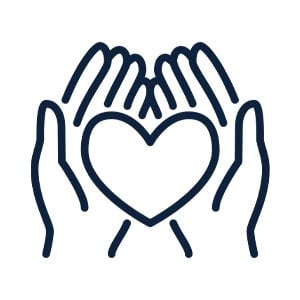
Enhanced Comfort and Safety
Manage undesirable acoustics and movement from regular or extreme consumer use.
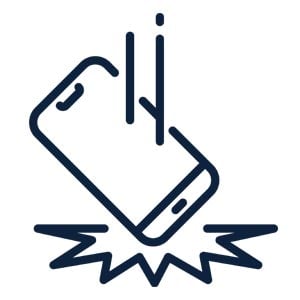
Protect Against Extremes
Cushion against drop shock and collision impact mechanical energy.
How to Cool and Protect EV Batteries Against Collision and Thermal Runaway
(View transcript)Ruggedize Batteries to Withstand Environmental Exposure
(View transcript)
Improve Performance and Reliability with NVH
Many applications are subject to extreme environments where Noise, Vibration, Harshness (NVH), and shock are prevalent. These conditions can wear down mechanical and bonded joints, mating surfaces and device ruggedization or negatively impact end customer satisfaction with unwanted noise. Integrating components that effectively absorb, prevent or distribute this extra, intermittent energy enables smoother, quieter, more reliable performance by end users. Boyd offers a wide variety of solutions to reduce NVH and absorb shock. By selecting the right material, manufacturing process, and geometry for products like vibration isolators, stamped dampers, grommets, bumpers and cushions, Boyd enables device and technology designers to focus on improving the functionality of end products instead of troubleshooting NVH and shock issues.
Have a Question?
What is Shock, Noise, Vibration, and Harshness?
Shock, noise, vibration, and harshness (NVH) refers to the undesirable qualities experienced in a mechanical system. Shock and NVH encompasses the assessment, control, and mitigation of shock (sudden acceleration or deceleration), noise (unwanted sounds), vibration (oscillations or shaking), and harshness (unpleasant sensations). Shock, noise, vibration, and harshness is generated from engines, suspensions, aerodynamics, other interactions between components, or end product use.
Why Use Shock and NVH Protection?
Shock and NVH protection helps dampen, absorb, or isolate either the source or the end user or sensitive components that require protection. Excessive shock and NVH can impact user experience and decrease comfort. Shock and NVH can also damage internal components like electronics and reduce product performance and lifetime.
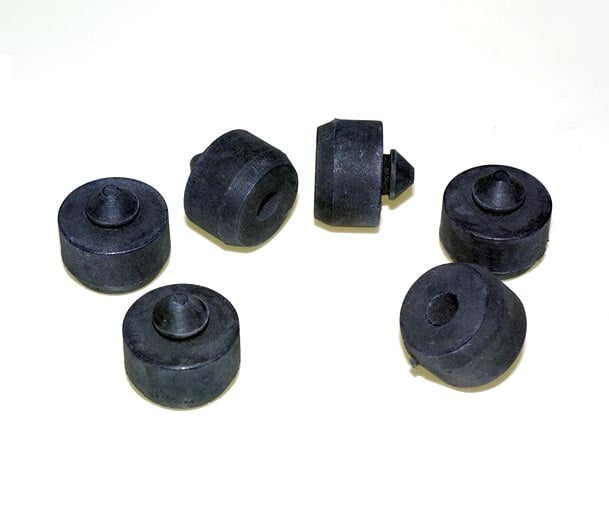
Why Use Boyd’s Shock and NVH Solutions?
Boyd’s experienced technical team has expertise in a broad range of advanced materials where we can mix and match the best fit materials and fabrication processes to mitigate the impact of shock, noise, vibration, and harshness in your application. Our engineers can design and manufacture ideal solutions for long term and dependable performance requirements for a wide range of conditions. From product or manufacturing design to complex tooling and assembly needs, we offer a comprehensive one-stop solution for shock and NVH solutions.
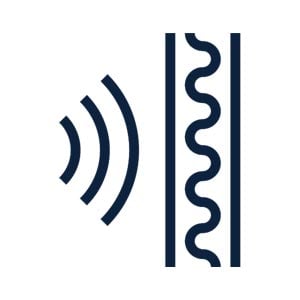
Dampers
Vibration damping can be added to a structure in many ways to reduce excessive resonant behavior. The most common type is material-based damping created by straining visco-elastic materials (VEM) in either shear or tension/compression. Performance is optimized by selecting a VEM with maximum loss factor in the temperature and frequency range of interest, and with a stiffness range that maximizes strain energy in the damping element. Vibration damping requires optimization through material selection, treatment design and placement to ensure good performance.
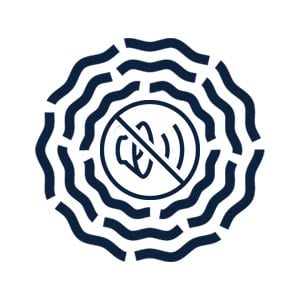
Absorbers and Barriers
For conditions involving excessive radiated noise, a common countermeasure is to enclose the noise source with acoustic absorbing materials to reduce noise levels before they are transmitted to the receiver. Often a dense barrier layer is incorporated to reduce the transmission of noise through the enclosure. Design parameters like foam type, thickness and cover films laminated to the foam are adjusted to achieve good acoustic absorption over the needed frequency range.
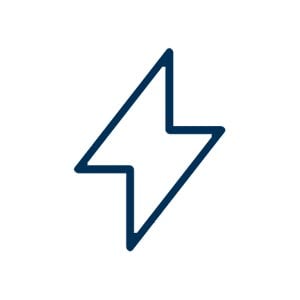
Isolators
A common method to mitigate vibration transmission is to insert compliant materials that isolate and de-couple the vibration. These isolating materials are converted into many geometries in a wide range of parts from die-cut isolation gaskets, grommets, bumpers or cushions, to molded rubber components. The isolator is selected to be as compliant as possible and with optimum damping to control unwanted amplification.
Mitigate Shock and NVH Impact with the Right Technology
Boyd offers a wide variety of solutions to reduce NVH and absorb shock. By selecting the right material, manufacturing process, and geometry for products like vibration isolators, stamped dampers, grommets, bumpers and cushions, Boyd enables device and technology designers to focus on improving the functionality of end products instead of troubleshooting NVH and shock issues.
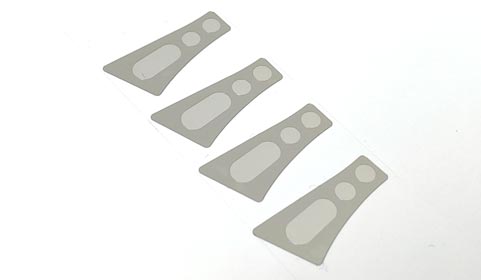
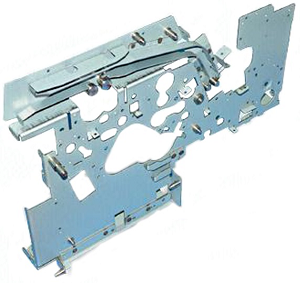
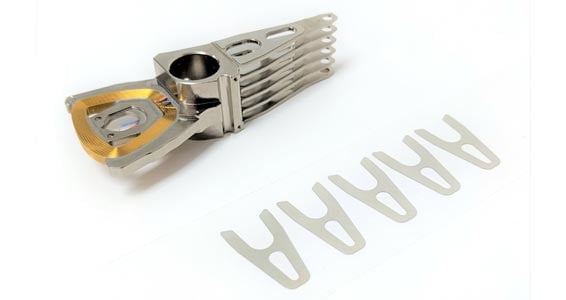
Boyd’s Stamped Damper Solutions
Boyd’s experienced technical team has expertise in stamped and fabricated metal components ideal for long term and dependable performance requirements for structural components like mounting and metal brackets made from SUS 304 stainless steel to hard disk drive (HDD) dampers. From product or manufacturing design to complex tooling for progressive die stamping to part cleansing and assembly needs, we offer a comprehensive one-stop solution for metal stamping and metal fabrication. With stringent controls for production flow, on‐time delivery and cleanroom manufacturing environments down to Class 100, we deliver zero‐defect metal stamping and fabricated products that adhere to international standards.
Isolator Seals
Isolator Seals protect from contaminant ingress as well as shock, vibration, and harshness. These seals are a low-cost solution to improve reliability and ensure longer lifetimes. Boyd’s custom rubber molding and plastic molding solutions feature a number of various manufacturing technologies to achieve specific shape, dimensional and performance needs across a wide variety of markets with innovative & cost effective tooling designs and quick speed to market. Color and texture matches are available for brand management and aesthetic needs. Over-molding technologies combine multiple materials and/or colors to consolidate complementary component designs. Our experienced field application engineers will review your designs to recommend adjustments that enhance performance or help meet cost saving objectives.
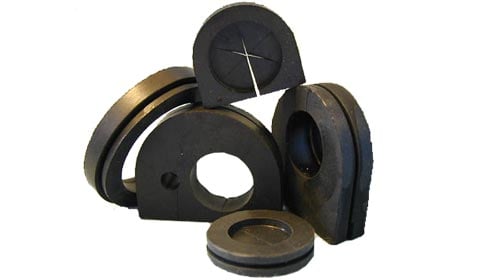
Shock, Noise, Vibration, and Harshness Solution Details
Materials
- Rubber
- Natural rubber/Polyisoprene (NR)
- Ethylene-Propylene-Diene-Monomer (EPDM)
- Styrene Butadiene rubber(Buna S/SBR/GR-S)
- Synthetic Polyisoprene (IR)
- Chlorsulfonated Polyethylene, Hyalon (CSM)
- Acrylonitrile Butadiene, Nitrile, Buna N (NBR)
- Chloroprene, Neoprene (CR)
- Silicone (Si)
- Epichlorohydrin(ECO)
- Fluoroelastomer
- Plastic
- Polyethylene (PE)
- Polypropylene (PP)
- Polycarbonate-ABS (PC-ABS)
- Acrylonitrile Butadiene Styrene (ABS)
- Nylon
- PVC
- Talc & glass fillers available
- Metals
- Stainless steel (ex. SUS 304)
- Aluminum
- Copper
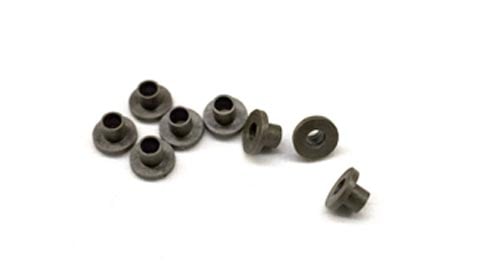
Capabilities
- Precision 10 to 1100 ton stamping presses
- Progressive die stamping or stage tool stamping
- CNC laser, turret punch press & wire cutting
- Metal forming
- Robotic laser & spot welding
- Precise finishing processes and coatings
- Cleanroom manufacturing Class 100 to Class 100K, ultrasonic cleaning
- Injection, compression, and transfer molding
- Vacuum molding & forming
- Metal insert over-molding
- 2 & 3 shot over-molding
Have questions? We’re ready to help!