Testing and Validating
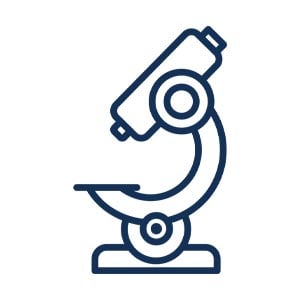
Verify Expected Function
Corroborate simulated or calculated performance with appropriate functionality tests before investing in production.
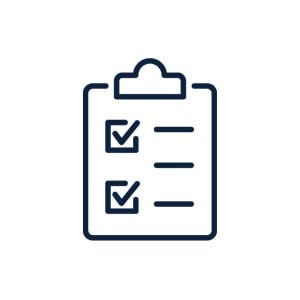
Make Informed Decisions
Collect useful data for refining or enhancing product design.
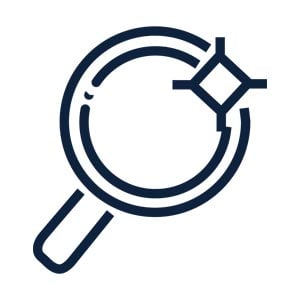
Find and Mitigate Warranty Risks
Identify and troubleshoot potential issues early, before manufacturing and consumer use.
Boyd Spotlight Series – Senior Quality Engineer
(View transcript)
Testing and Validating Solutions with Boyd
Boyd’s testing and validation services are designed to ensure that products and solutions meet application requirements as well as industry standards. With design centers across the globe, testing and validation services are available regionally, staffed by engineers familiar with both global standards and local needs. Boyd engineering’s commitment to innovative problem solving extends to testing services; engineers collaborate closely with customers and can adapt to any unique needs or specifications to ensure full product validation.
Testing and Validating Designs and Production Parts
Creating designs and solutions that adhere to the most stringent performance and quality standards is crucial to our customers’ success. That is why we have systems in place to ensure quality is continuously upheld, including our qualification process that ensures parts are produced uniformly and consistently.
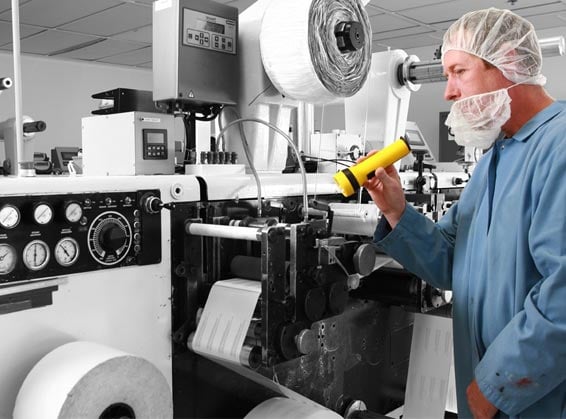
By rallying a range of state-of-the-art testing technologies in various stages of planning and production, the technical experts at Boyd eliminate inconsistencies in product development and control quality and improve reliability. With a strong culture of quality, our equipment facilitates the mapping of various stages of product development and manufacturing bottlenecks without compromising quality.
Quality Certifications
- ISO 9001
- IATF 16949 (Automotive)
- ISO 14001 (Environmental)
- ISO 13485 (Medical)
- AS9100 (Aerospace)
- OSHAS
- Nadcap™
Facility-Specific Certifications
- AWS D17.1 (MIL-STD 1595A / MIL-STD-2219)
- AWS B2.2:2010
- AWS C3.3
- AWS C3.7:2005
- AMS 2750D:2005
- AMS 2770H:2006
- MIL-H-6088G
- MIL-B-7883C
- Aerospace Qualified Welders (certified to AWS D17.1)
- AWS Qualified Brazers (certified to AWS B2.2)
- Certified Welding Inspectors (certified to AWS QC1 Standard)
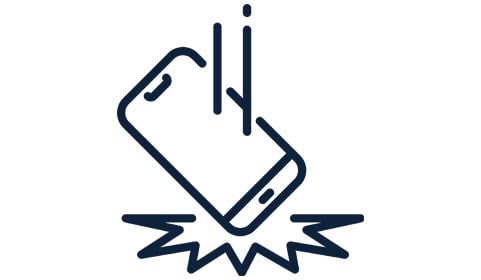
Mechanical Testing
Increasingly critical to ruggedized designs, ensure the structural integrity and compliance of your solution. From testing mechanical conformance, shock and vibration, to life and reliability testing, Boyd can validate the mechanical strength of your design.
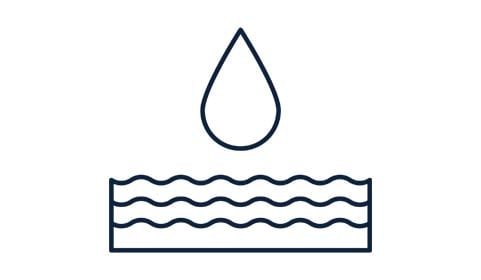
Fluid Testing
As liquid systems become more prevalent and more consumer goods are expected to seal against the elements, Fluid Testing is a keystone in production and design testing. Validate the seals and performance of liquid systems with a broad range of pressure, flow resistance, and leak testing.
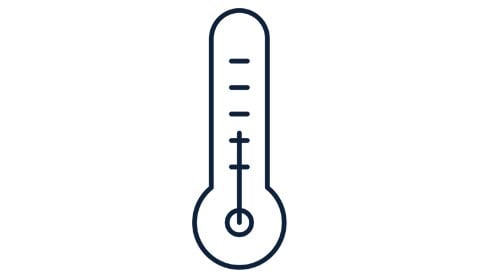
Thermal Testing
Test the performance of your thermal management solution to validate CFD simulation results. Ensure that complex systems meet temperature and pressure drop requirements to protect sensitive components and improve the reliability and lifetime of your product. Boyd’s Thermal testing runs the spectrum of testing liquid or air-cooling system heat dissipation, thermal shock testing, interface resistance testing, and comprehensive two-phase system testing.
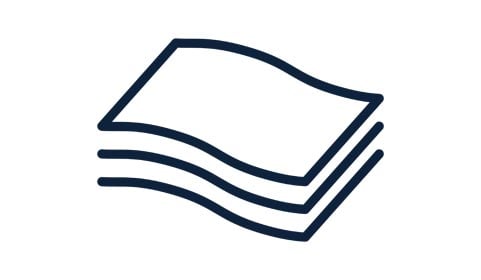
Material Testing
The cutting-edge testing tools and equipment at Boyd help to validate that all materials, products, and processes conform to customer needs. By implementing a range of state-of-the-art testing technologies in various stages of planning and production, the technical experts at Boyd eliminate inconsistencies in product development and control quality and improve reliability.
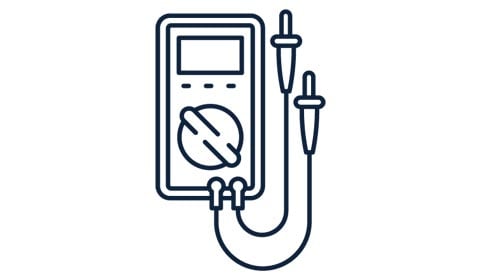
Electrical Testing
Custom electrical circuit testers are used to measure and test membrane switches, printed circuits, and other printed electronics. Boyd offers circuit testing on 100% of our printed electronics components.
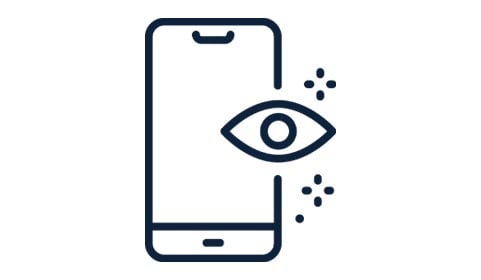
Display Testing
Boyd’s advanced optical and functional display testing ensure your integrated displays meet all visual and performance requirements. We can compare technologies and test how they affect function, output quality, overall performance, and cost effectiveness.
Have questions? We’re ready to help!