Thermosiphons are an efficient and versatile two-phase cooling solution that have grown in popularity over the last few years. In the first of our three-part blog series, we’ll be going over exactly what a Thermosiphon is and the key features that make it unique.
What Are Thermosiphons?
A Thermosiphon is a passive, two-phase cooling system that relies on gravity to circulate a fluid rather than a capillary wick structure often used in heat pipes and other heat transport devices. As with all passive two-phase cooling, the liquid and vapor exist within the self-contained envelope and contain no pumps or other moving parts.
While there are several different constructions for Thermosiphons, they generally all consist of three basic components: an evaporator, a fluid loop (or adiabatic section), and a condenser. The evaporator absorbs energy into the system, which causes the working fluid, usually a refrigerant or other dielectric fluid, to turn into vapor. The vapor then travels through the adiabatic section (vapor tube) due to the pressure difference between hot evaporator and cool condenser (buoyancy), where the heat is expelled from the system and the vapor condenses back into a liquid and returns to the evaporator via gravity. This process is repeated indefinitely as long as there is heat to reject from the system.
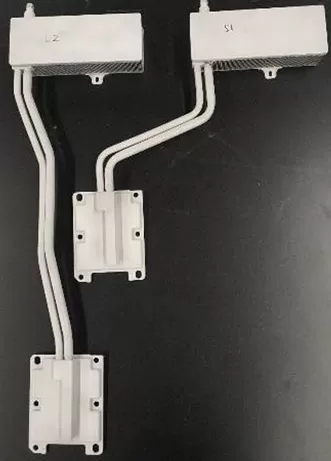
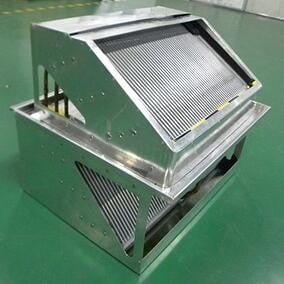
What makes Thermosiphons unique from other two-phase cooling systems is that they lack any kind of wicking structure. Where the wicking structure in a Heat Pipe creates a capillary pressure to return condensed fluid, Thermosiphons rely on gravity for the same process. This allows them to more efficiently carry higher heat loads across longer distances, but requires Thermosiphons to be designed and used in a specific gravity orientation. The thermosiphon evaporator must be located below the condenser so that gravity can return the working fluid.
Common Applications for Thermosiphons
Thermosiphons are useful for a wide variety of industries and devices. Thermosiphons are effective enterprise solutions for CPUs, GPUs, ASICs and FPGAs within servers, networking equipment, and cabinets. Industrial and power applications benefit from thermosiphons for cooling wind and solar inverter IGBTs. Power amplifiers in telecommunications equipment like Remote Radio Units and full cabinets leverage the high cooling capacity of thermosiphons.
The heat transfer coefficient of a thermosiphon is hundreds of times more than conventional materials like aluminum or copper and energy is transported with consistent temperatures throughout the unit. This makes Thermosiphons ideal for larger surfaces, heat transfer across multiple devices, or as a cost-effective option for any application where orientation with respect to gravity is known and fixed.
Thermosiphon Testing
At Boyd, Thermosiphons go through a variety of tests to ensure that they’re reliable and ready for use. Pressure testing, leakage testing, and thermal performance testing are just a few of the methods used at Boyd to ensure that each Thermosiphon meets specifications.
In our next blog, we’ll go into detail on the four types of Thermosiphon configurations at Boyd: Direct Contact Loop Thermosiphons, 2D Thermosiphon Fins, 3D Direct Contact Loop Thermosiphons, and Air-to-Air Loop Thermosiphons.