Polymer Forming
Boyd has decades of experience in polymer science. Leverage our vast knowledge of rubber and plastic compounds and chemical formulations to design three-dimensional solutions customized for your specific applications.
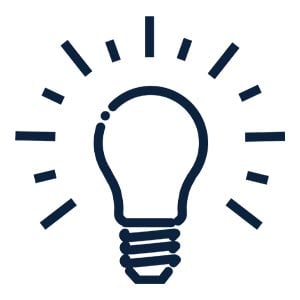
Unlimited Possibilities
Fabricate the most challenging components with Boyd’s versatility in elastomeric and plastic forming.
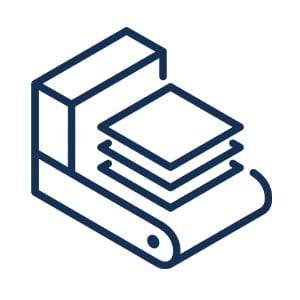
Save Costs and Secondary Operations
Meet complex project requirements with custom durometer, wall thickness, color matching, and up to four different materials in one profile.
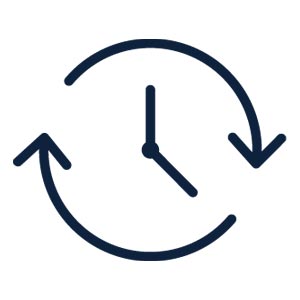
Reduce Production Time
Get your product to market quicker with rapid prototyping without expensive tooling for design samples, presentations, or proof-of-concept.
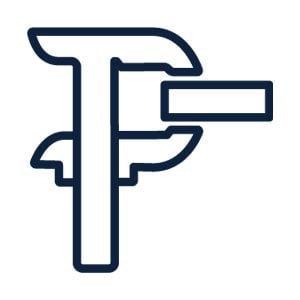
High Quality and Precision
Achieve design, functionality, and aesthetic goals with Boyd’s polymer forming manufacturing expertise.
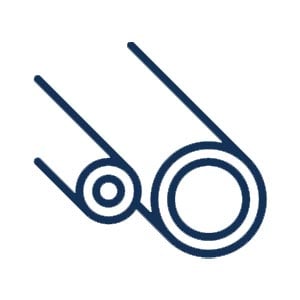
Meet Demanding Performance Applications
Leverage our extensive compound options, ranging from dense and sponge rubber, highly engineered thermoplastics, silicones, and custom compounds.
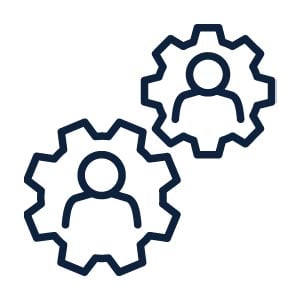
World Class Engineering Support
Push forming processes to their limit or innovate with our team to fabricate cutting-edge products.
In-Mold Decoration (IMD ) and In-Mold Labeling (IML) Solutions
(View transcript)
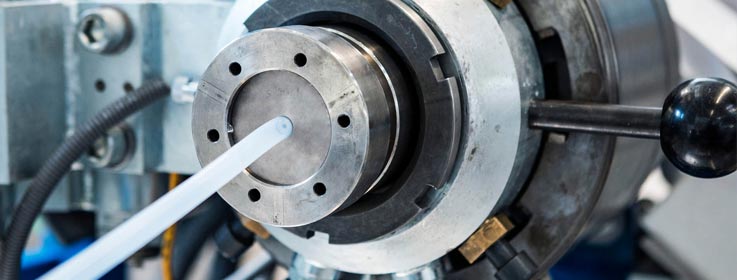
Polymer Forming for Multi-Functional Engineered Material Solutions
Polymer forming is the process of shaping and transforming polymer materials into desired products or structures. Forming includes processes like molding, extrusion, and additive manufacturing. Polymer forming is crucial in industrial technology, transportation, aerospace, electronics, and consumer goods markets. Customers benefit from Boyd’s polymer forming process variety with specialty in customized plastic and rubber solutions. Boyd leverages polymer forming design flexibility to fabricate multifunctional, lightweight, and cost-effective components for our customers’ most demanding applications.
Leveraging Automation for Higher Quality Plastic Components
Boyd implements smart manufacturing practices with robotic automation in some of our plastic-forming processes. Reduce lead times and production costs while enhancing quality and efficiency by digitizing manufacturing with Boyd.
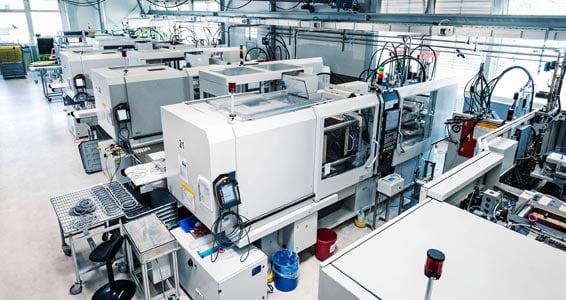
Meet Your Capacity Needs and Production Rate Requirements with Boyd
Boyd’s equipped to produce precise three-dimensional solutions with injection molding and multi-durometer extrusion of foam, sponge or dense rubbers and thermoplastics in intricate profile shapes.
Silicone and Plastic Injection Molding
Injection Molding is one of the cornerstones of Boyd’s plastic and silicone manufacturing capabilities. Injecting molten plastic or silicone into custom molds offers versatile design options and creates durable parts for harsh conditions. Boyd’s production facilities include several state-of-the-art injection molding machines of various sizes and capabilities, with machine tonnage ranging from 40 to 600 tons. We also combine our complementary capabilities like spray painting and laser etching or value-added membrane switches and displays to build complete user interfaces.
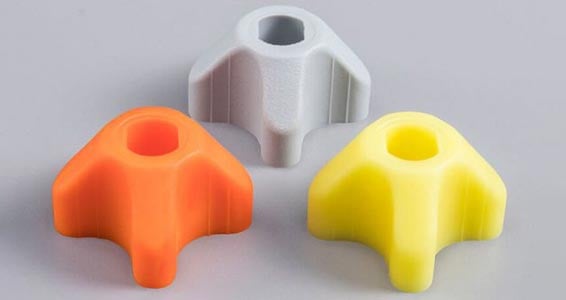
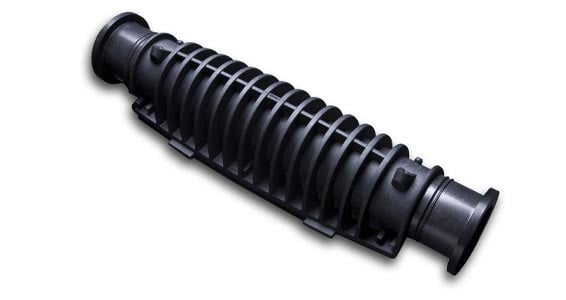
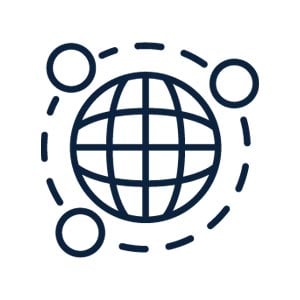
Save Cost & Simplify Your Supply Chain
Boyd can combine your injection molded component with switches, keypads, and displays for a vertically-integrated solution.
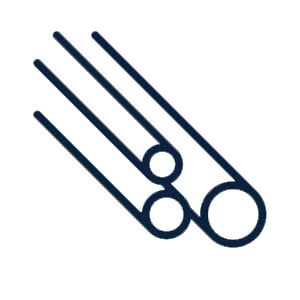
Performance Materials
Meet demanding performance specifications with broad material options ranging from commodity plastics, liquid silicone rubber, highly engineered polymers, and more.
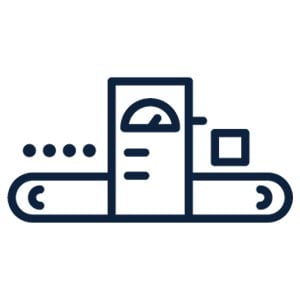
Unique Fabrication Methods
From in-mold decoration to two-shot molding and more, Boyd’s state-of-the-art injection molding equipment helps produce custom solutions to ensure your project meets every requirement.
Polymer Extrusion
Polymer extrusion is a manufacturing process that shapes a polymer material by forcing it through a die to create a continuous profile, tube, or film. Boyd’s extensive polymer extrusion capabilities create intricate profile shapes, tubes, seals, and cords out of rubber, polymers, or thermoplastics ensuring an optimal solution for your extrusion project. Our broad range of manufacturing lines can extrude up to four different materials in one profile with custom color matching for even the most complex applications. Extensive in-house extrusion tool and rapid prototyping capabilities create prototypes with quick turn-around time.
Multifunctional Precision Extrusions with Boyd
We extrude dense, foam, or sponge rubber, silicone rubber, and thermoplastics in intricate profile shapes for comprehensive streamlined solutions. Common extruded rubber and plastic components include finishing trim, RV slide-out seals, d-bulb seals, door seals, clip-on seals, window seals, trunk or hood seals, flex extenders, tank straps, and hoses.
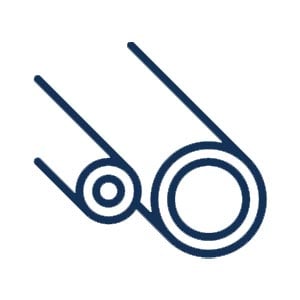
Meet Demanding Performance Specifications
Push your product’s performance with extensive extrusion material options, ranging from dense and sponge rubber, highly-engineered thermoplastics, silicones, and custom compounds.
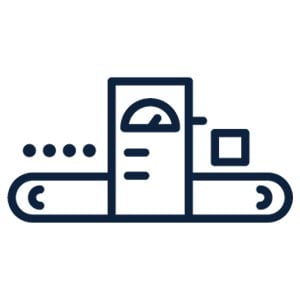
Save Costs and Secondary Operations
Boyd’s unique extrusion methods help you save cost and meet complex project requirements with custom durometer, shore hardness, wall thickness, color matching, and up to four different materials in one profile.
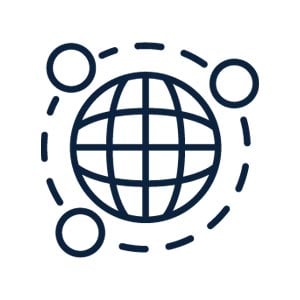
Save Cost and Simplify Your Supply Chain
Boyd can combine your custom extruded profiles, tubes, seals, and cords with other injection molding and finishing capabilities for a vertically-integrated solution optimized for your assembly operations.
Silicone 3D Printing and Prototyping
Build rubber and plastic parts layer by layer with 3D printing, or additive manufacturing. Boyd leverages the speed of 3D printing to produce rapid prototypes enabling fast product development for complex silicone and plastic products. Complex geometries that are difficult in other production methods are easily produced with 3D printing. Challenging features such as undercuts, re-entrant angles, hollow spaces, and through holes that change directions are much simpler with 3D printing. With reduced tooling costs, development time, and design risk, 3D printing is an ideal choice for complex polymer products.
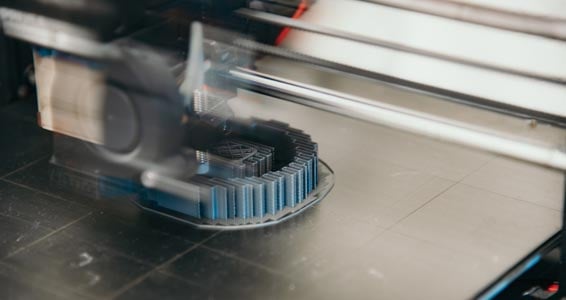
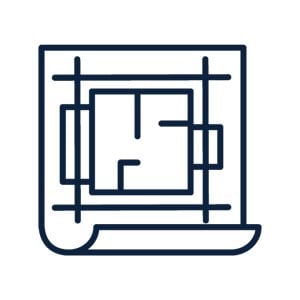
Flexible Design
Meet tough design specifications and realize complex part geometries that include undercuts, re-entrant angles, hollow spaces, and more with Boyd’s 3D printing options.
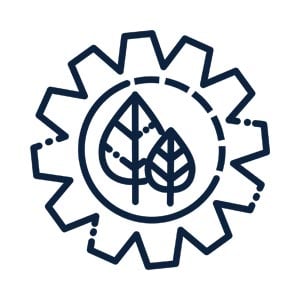
Eliminate Waste
Iterate and refine product designs quickly with small 3D printed production runs to cut down on extensive tooling costs and waste.
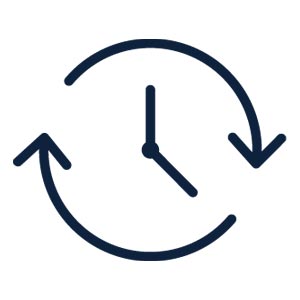
Reduced Production Time
Get your product to market quicker with prototypes that can be created and easily changed without expensive tooling for design samples, presentations, or proof-of-concept.
Over-molding and Encapsulation
Over-molding is a manufacturing process that combines two materials together to create a single part. Mold a softer plastic or rubber over a rigid plastic or metal for a final component that benefits from both material properties. Over-molding plastic components uses two different injection molds: one for the rigid substrate, and a second for the softer material. Overmolding gives you structural rigidity and mechanical stability with added friction for grip, a soft, rubberized feel, smoothed over sharp edges, reduced vibration, and much more. Boyd’s material science expertise spans a wide variety of thermoplastics and silicone rubber compounds to customize for specific project needs.
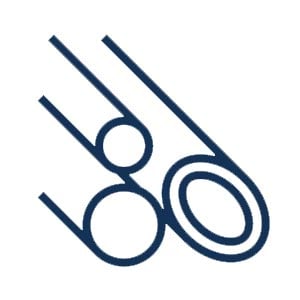
Reap the Benefits of Multiple Materials
Combine visual and functional benefits of multiple types of thermoplastics, rubbers, and silicones into a single component to meet tough visual and functional requirements.
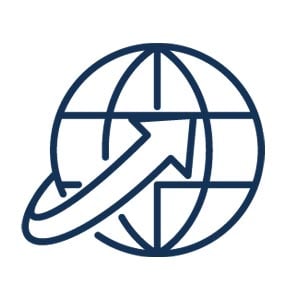
Reduce Cost and Time to Market
Lower weight, reduce cost, eliminate fabrication steps, and reduce overall manufacturing time with overmolding instead of assembling separate components.
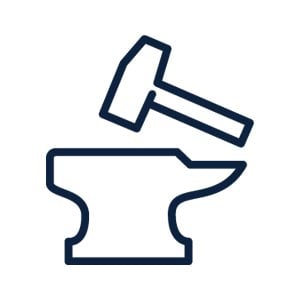
Protect Sensitive Components
Increase product lifetimes by leveraging durable rubbers and silicones to encapsulate and protect electronics and other sensitive components.
Have questions? We’re ready to help!