Plate Fin Heat Exchanger
Solid plates conduct heat from liquid flow paths to secondary fluid flows and offer increased structural integrity and easy customization.
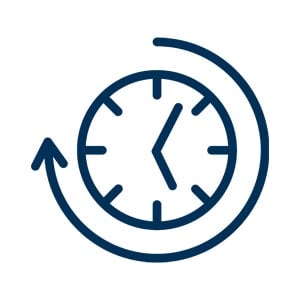
Longer Product Lifetimes
Vacuum brazed for maximum cleanliness, quality, and reliability
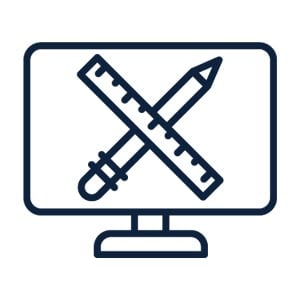
Design Flexibility
Flexible fin geometry and a variety of folded fin types.
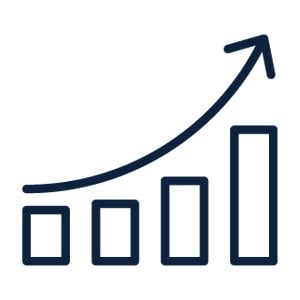
Improved Performance
Improve heat dissipation, device performance, and speed with added surface area.
Liquid to Liquid Heat Transfer
Plate Fin Heat Exchangers are used to transfer heat from a liquid loop to another fluid stream, either another liquid system. The heat transfer fin and plate construction add to the structural integrity of the heat exchanger, enabling it to withstand high pressures. This construction type also can contain large surface areas in relatively small heat exchanger volumes, which makes it a compact option for applications with tight volume or weight requirements.
Have a Question?
How Do Plate Fin Heat Exchangers Work?
A Plate Fin Heat Exchanger utilizes solid plates to conduct heat from one fluid flow path to heat transfer fins which then transfer heat to a second fluid.
Why Use Boyd’s Plate Fin Heat Exchangers?
Boyd’s aluminum Plate Fin Heat Exchangers are custom-designed, as every system is unique. The Plate Fin Heat Exchanger construction is easily customizable to meet a broad range of heat transfer and system requirements. We vacuum braze our plate heat exchangers for maximum cleanliness, quality, and reliability. Through our numerically controlled process and robust fixtures, we assure complete metallurgical bonding between plate fins for rugged and leak-free operation. Boyd operates multiple vacuum brazing ovens, including one that can braze parts up to 3.05 m (10 feet) long and 0.97 m (3 feet 2 inches) wide.
A Plate-Fin Heat Exchanger can be designed to use any combination of gas, liquid, and two-phase fluids. Our experienced engineering team carefully selects the number of plate and fin layers, the size of the plates and fin, and the type of fin for optimum performance. Manifold ducting and mounting brackets are welded in place as specified, and any required paint or coating (including MilSpec compliant) can be added.
Plate Fin Heat Exchanger Product Details
Plate Fin Heat Exchanger Materials
- Cast Aluminum Alloys:
- A356
- A357
- C443
- 700 series
- Wrought Aluminum:
- Multi clad braze sheets
- Al 1100
- Al 3000 series (not heat treatable)
- Al 6000 series (heat treatable)
- Al 6061
- Al 6063
- Al 6082
- Al 6951
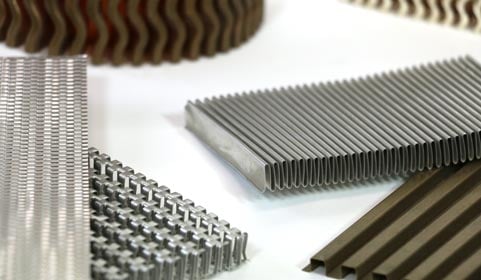
Fin Types
- Round-crested
- Flat-crested
- Lanced & offset
- Louvered
- Wavy/ruffled
Have questions? We’re ready to help!