Heat Pipes: Effective, Reliable Cooling Solutions
Heat pipes are reliable, passive two phase heat transport. Combine them with other thermal technologies for long lasting, higher performance, efficient cooling solutions.
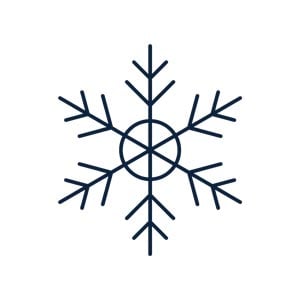
High-Precision Temperature Control
Remove heat from constrained or densely packed areas
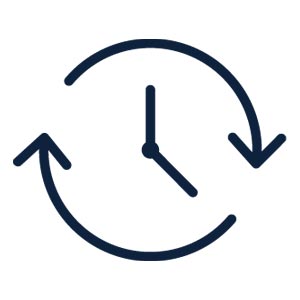
Longer Product Lifetimes
Leverage up to 20 years of consistent, passive heat transport without thermal performance degradation
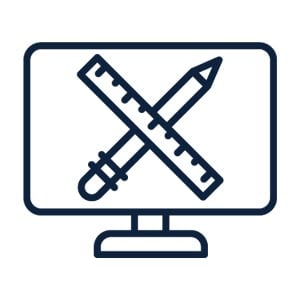
Cost Efficient Design Flexibility
Routable, cost effective heat pipes move heat where cooling is available
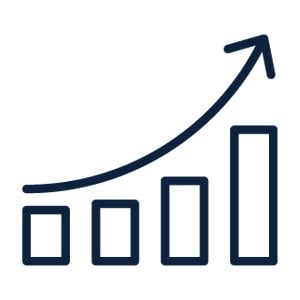
Efficient Heat Transport Boosts Thermal Performance
Increase heat transfer by 10 to 200 times that of solid copper, aluminum, or graphite.
Two Phase Cooling Video
(View transcript)
Heat Pipes: Reliable, Versatile Two-Phase Cooling
Boyd has pioneered heat pipe technology development and set the standard for two phase cooling solutions for over 50 years. Our broad expertise in heat pipe materials, fluids, constructions, and other thermal technologies makes Boyd an ideal heat pipe designer and manufacturer for the most demanding and innovative applications.
Have a Question?
What Are Heat Pipes?
Heat pipes utilize the high heat capacity of fluid phase change in a robust format, making them one of the most efficient and versatile thermal management technologies to reliably and quickly transport heat.
Heat pipes are made of three main components: a vacuum sealed shell or envelope, a working fluid, and a wick structure. The shell keeps the heat pipe working fluid vacuum sealed for decades of consistent heat transport. The working fluid changes phase in the application temperature range and must be compatible with the heat pipe shell and wick materials. The wick passively moves fluid through the heat pipe.
How Do Heat Pipes work?
A heat pipe is a closed evaporator-condenser system. The sealed shell is a hollow tube lined with a capillary structure or wick. A working fluid at a specified vapor pressure saturates the wick capillaries in a state of equilibrium between liquid and vapor.
Liquid in the wick evaporates when the heat pipe starts absorbing heat. The vapor fills the hollow area of the heat pipe, called the vapor space, and diffuses heat evenly across the heat pipe. Heat distribution across the heat pipe happens quickly and determines the high thermal conductivity of the heat pipe.
When a spot along the heat pipe drops below the evaporation temperature, the vapor contacts the cooler wick and shell and releases its latent heat into the casing. The vapor no longer has enough energy to maintain a gaseous form and condenses back into liquid then seeps into the wick structure. Capillary action within the wick returns the condensate to the evaporator region and completes the operating cycle.
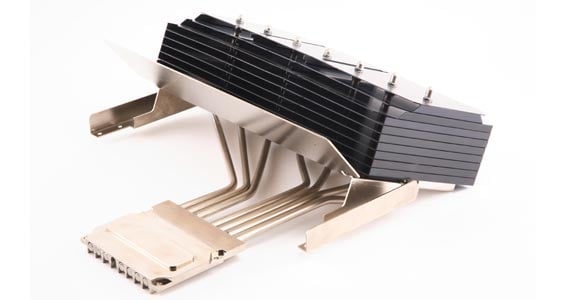
Why use Heat Pipes?
Heat pipes have an extremely effective high thermal conductivity. Solid conductors like aluminum, copper, graphite, and diamond have thermal conductivities ranging from 250 W/m•K to 1,500 W/m•K, but heat pipe effective thermal conductivity ranges from 5,000 W/m•K to 200,000 W/m•K. Heat pipes also transfer heat over relatively long distances.
Over 50 years of Heat Pipe Heritage
Boyd has developed specialized heat pipes for challenging applications for over half a century. We have an immense thermal management technology portfolio available today to uniquely integrate with heat pipe technology and invent creative thermal solutions that implement the best fit combination of technologies. Our engineering team’s experience coupled with proven manufacturing techniques enables Boyd to produce optimized and reliable heat pipe technologies to enhance your thermal system efficiency at scale.
Efficiently Spread and Transport Heat
Heat pipes integrated into other thermal technologies create a more wholistic, higher performing, more efficient thermal management solution. Heat pipes enhance air cooling with higher thermal conductivity and can transport heat, spread heat, or improve air-cooled heat sink efficiency to delay the need for liquid cooled solutions in increasing heat loads.
Using Heat Pipes to Transport Heat
Heat pipes are designed and manufactured to move heat from a heat source or high heat flux region to a remote area. This functionality is ideal to remove heat from constrained or densely packed areas to regions with cooler air or more volume for air cooled heat sinks. With more design flexibility, product designers and architects can push product performance and layouts to enable some of the most challenging air cooled applications with a reliable, cost-effective solution.
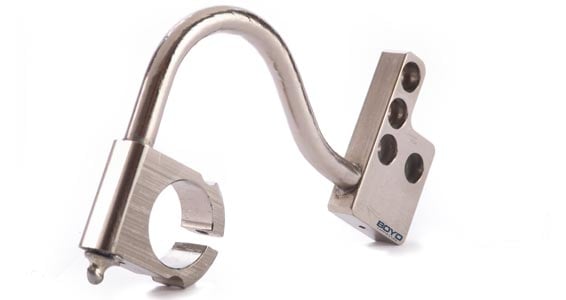
Using Heat Pipes to Spread Heat
Embedded heat pipes remove local hot spots, reduce heat buildup around electronic components, and improve air cooled heat sink efficiency by 20% (compared to aluminum or copper base spreaders) with faster, more even heat spreading. This is especially impactful in applications where the heat source is small relative to heat sink fin area, like electronics or computers. Bend or flatten heat pipes to meet thermal and geometric requirements, reduce overall height, increase surface contact, or route around keep-out areas like mounting hardware. Embedded heat spreading heat pipes give thermal architects more flexibility because they don’t require changing heat sink geometry, which is useful in retrofit applications or to increase the power of existing products.
Meet Application Requirements with the Right Construction
Boyd’s broad heat pipe technology portfolio demonstrates our deep heat pipe expertise and heritage that you can leverage to maximize reliable thermal performance in any application.
Copper Water Heat Pipes
Copper-water heat pipes are a popular component across a wide variety of applications because of the high heat capacity of two-phase water cooling in a versatile copper package. Boyd’s tightly controlled manufacturing processes backed by product field experience ensure our copper-water heat pipes can last well over 20 years.


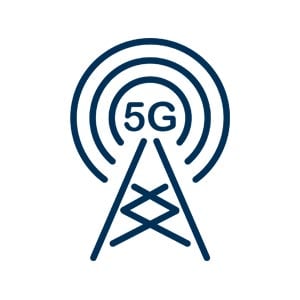
Telecom and 5G
Enhanced die cast heat spreaders, telecom server microprocessor and test equipment cooling

Cloud Computing
Heat spreading and cooling assemblies for CPUs, GPUs and DIMM cards
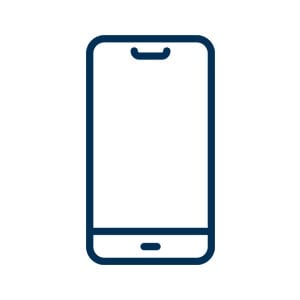
Home Electronics
Laptop and notebook cooling assemblies, handheld and console gaming system cooling systems
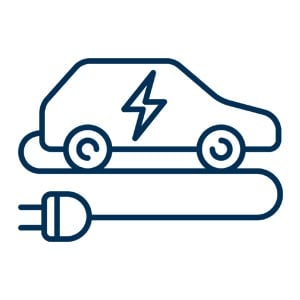
Energy Management
Solar receivers, thermionic converters, alkali metal thermal-to-electric converters (AMTEC), stirling engine interfaces, engine component and fusion applications

Industrial Equipment
Chemical and materials processing, glass making, epitaxial deposition, semiconductor crystal growth, vapor deposition, diffusion annealing, thermophysical property characterization, and temperature and thermocouple calibration
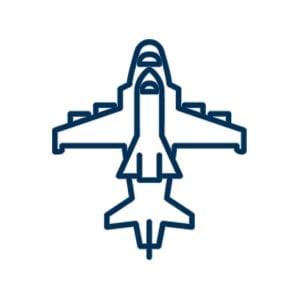
Aerospace and Defense
Magnetoplasmadynamic (MPD) thrusters, isotope separation, aerospace leading edges, rocket nozzles, high-temperature space radiators
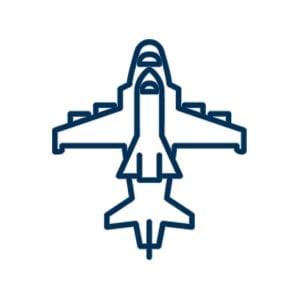
Aerospace and Defense
Cryocooler interfaces, infrared sensor cooling, camera and sensor thermal management in launch and orbit conditions, satellite component cooling, superconducting magnets, deep sea applications, high acceleration and geosynchronous orbit applications

Medical
Low or cryonic medical equipment temperature management, refrigerator and freezer cooling systems for sample preservation and testing and sensitive detection devices in medical laboratory equipment
Loop Heat Pipes
Loop Heat Pipes (LHPs) are bendable, flexible, routable, and can transport heat further than conventional heat pipes. Ideal for cooling dispersed systems, they can incorporate multiple evaporators and passive or active thermal regulators to handle multiple heat sources. Loop Heat Pipes can transport heat up to 23 meters (75 feet), withstand millions of flex cycles, and resist gravity loads up to 9g. They are a low-mass solution to solve complex and far-reaching geometries and are rugged technologies for demanding environments.
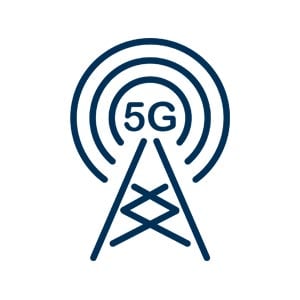
Telecommunications
Computer or server microprocessor cooling and test equipment thermal management

Aerospace
Lightweight avionics, motor and electronics cooling solutions in more electric aircraft (MEA), electronic heat transport to stowed radiator panels during satellite launch. They can also operate as thermal diodes to prevent backward heat leak.
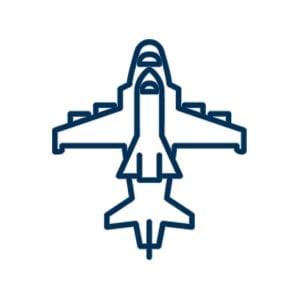
Defense
Actuator-mounted electronics cooling, engine waste heat wing and cowl anti-icing, and thermal signature suppression
Flexible Heat Pipes
Flexible Heat Pipes enable engineers to optimize heat-generating component locations to maximize serviceability and reliability and still maintain thermal performance in harsh operating conditions and where space is at a premium. Optimize moving actuator and remote terminal placement without sacrificing thermals. Added mobility also streamlines installation and maintenance in tight spaces.

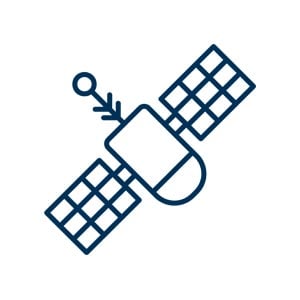
Aerospace
Avionics and aircraft equipment thermal management systems
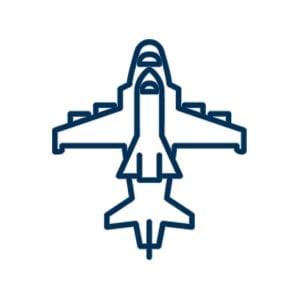
Defense
Avionics and aircraft equipment thermal management systems
Variable Conductance Heat Pipes
Variable Conductance Heat Pipes (VCHP) help engineers precisely control temperatures through controlled heat transport and rejection. They control evaporator temperature by using non-condensable gas (NCG) in the heat pipe, controlling the available condenser area. VCHPs are a cost-effective solution to maintain critical device temperatures without active components or sensors.

Medical
CAT scan cooling system
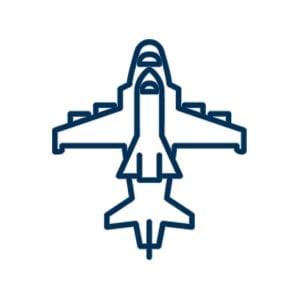
Aerospace
Satellite radiator panel thermal control, frozen startup conditions
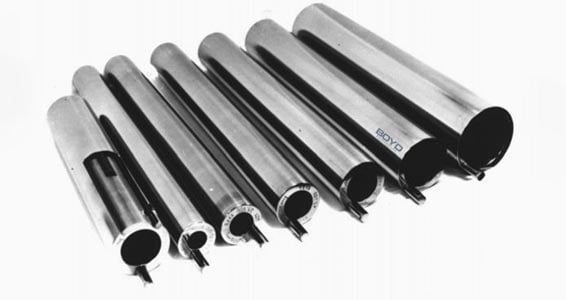
Isothermal Furnace Liners (IFLs) are ring-shaped liquid metal heat pipes that provide a uniform temperature working environment or zone using a single heater and controller for exact processes. They save time and energy while maximizing productivity by achieving isothermal wall temperature. IFLs are simple to install, expand design flexibility, and are extremely reliable and cost-effective.
Temperature adjustment is a simple one-step process and frequent profile measurements are unnecessary. Unlike probes, IFLs do not depend on heat transfer paths connecting to surrounding walls or the outside environment. Measured spatial temperature variation in an IFL is less than 10mK and in many cases may exceed the sensitivity of available measurement techniques.
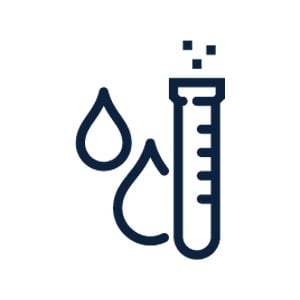
Lab and Test Equipment
Thermocouple and temperature calibration, research process tubes, laboratory furnaces

Industrial Equipment
Black body radiators, concentrated solar receivers, chemical processing

Semiconductor
Semiconductor crystal growth, vapor deposition
Constant Conductance Heat Pipes
Axially-grooved Constant Conductance Heat Pipes (CCHPs) thermally transfer high heat loads over 3 meters. They use a circle of grooves in the interior heat pipe wall envelope as the wick to efficiently pull condensate back to the evaporator from cooler surfaces where working fluid has condensed. They can cost less to fabricate than conventional wick heat pipes.
Axially grooved heat pipes work best where gravity is not a factor, like horizontal configurations or in space. They are low maintenance and ideal for applications where service is extremely difficult. Long-range heat transfer increases design flexibility, giving engineers thermal design options in challenging locations.
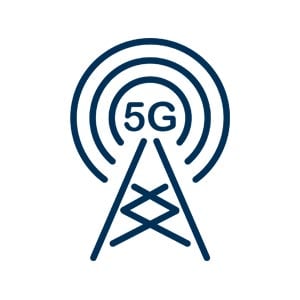
Telecommunications
Communications satellite cooling
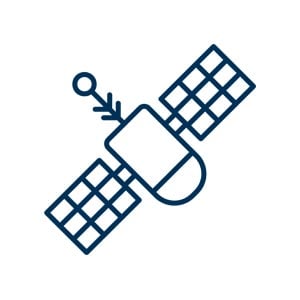
Aerospace
Satellite thermal control, radiator panels
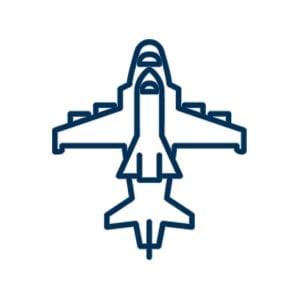
Defense
Defense satellite cooling
Heat Pipe Product Details
Heat Pipe Envelope & Wick Materials
- Copper
- 300 Series Stainless Steels
- Incoloy 800
- Inconel ® 600, 601, 718, 625
- Haynes 230, 188, 214
- Nickel
- Hastelloy C / Inconel® C-276
- Titanium
- Tantalum
- Molybdenum
- TZM (molybdenum-titanium-zirconium alloy)
- Rhenium
- Niobium
- Tungsten
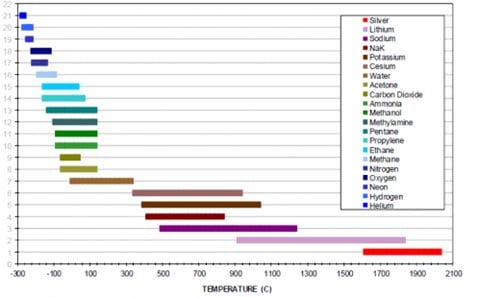
Heat Pipe Envelope & Wick Materials
- Copper
- 300 Series Stainless Steels
- Incoloy 800
- Inconel ® 600, 601, 718, 625
- Haynes 230, 188, 214
- Nickel
- Hastelloy C / Inconel® C-276
- Titanium
- Tantalum
- Molybdenum
- TZM (molybdenum-titanium-zirconium alloy)
- Rhenium
- Niobium
- Tungsten
Have questions? We’re ready to help!