SOLIMIDE® Foam for Semiconductor Equipment
Introduction
A leading process control instrumentation company approached Boyd for help redesigning the heating jackets for semiconductor fabrication and testing equipment. The jackets needed to tightly cover the equipment’s vacuum tubes and process lines and provide active heating and thermal insulation to maintain constant temperatures up to 200°C.
The heating jackets must be compatible with a variety of semiconductor equipment, including gas analyzers, mass flow controllers, thin film deposition instruments, and more, necessitating stringent environmental and fabrication requirements. Having relied on Boyd’s thermal expertise and precision converting experience on several successful past projects, the customer reached out for help.
Project Details
Customer:
Process Control Instrumentation Company
Application:
Semiconductor Manufacturing and Testing Equipment
Technology:
SOLIMIDE® Foam
Industry:
Semiconductor
Location:
United States
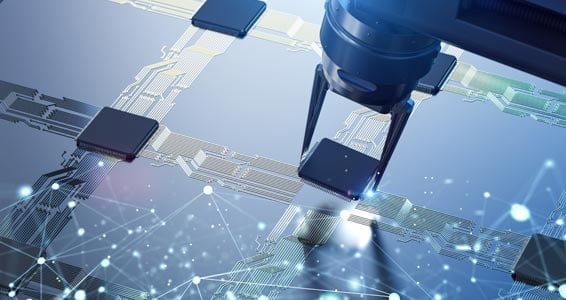
SOLIMIDE® for Semiconductor Equipment Challenge
The customer was initially using a combination of fiberglass batting and silicone foam as insulation within the heating jackets, but quickly ran into issues with this construction. These materials could be difficult to fabricate, generate particulates and outgassing, and were difficult to install. They wanted to transition to a cost-effective material that could not only handle the extreme temperatures, but also optimize environmental control, simplify fabrication, and facilitate installation and removal.
Project Goals
- Minimize outgassing and particle generation to protect employees and sensitive equipment
- Ensure materials could be fabricated into tight shapes and unique geometries while still meeting thermal requirements
- Engineer a cost-effective solution that was simple to install and remove for regular maintenance
Boyd’s SOLIMIDE® Solution
After analyzing the challenges with the initial heating jacket construction, Boyd’s engineers recommended the complete replacement of silicone foam and fiberglass batting with SOLIMIDE® foam. SOLIMIDE® is a lightweight, open-celled polyimide foam that Boyd successfully incorporated in similar pipe and duct lining applications in other industries. Boyd’s engineers knew that this polyimide foam could exceed the thermal requirements, solve many of the current issues, and improve overall heating jacket performance.
One of the biggest challenges with the initial jacket design was the material’s impact on the manufacturing environment. Silicone foams can heavily outgas at high temperatures, which condenses on sensitive materials and devices. Fiberglass batting easily generates particles that can damage other critical components in the same work environment and endanger the safety of employees with skin irritation and lung inhalation of particulate.
Since heating jackets are used in highly regulated semiconductor production and testing equipment in clean rooms with other sensitive devices, system architects must select materials that cannot damage other components. SOLIMIDE® was an ideal replacement since it features minimal outgassing, is formaldehyde free, and has extremely low particle generation.
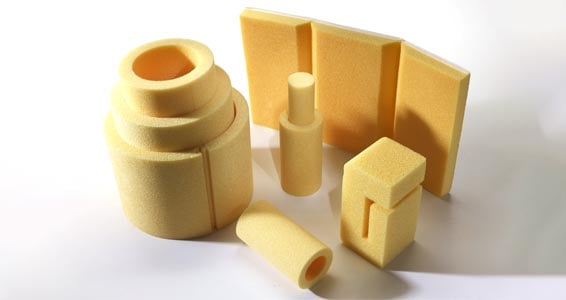
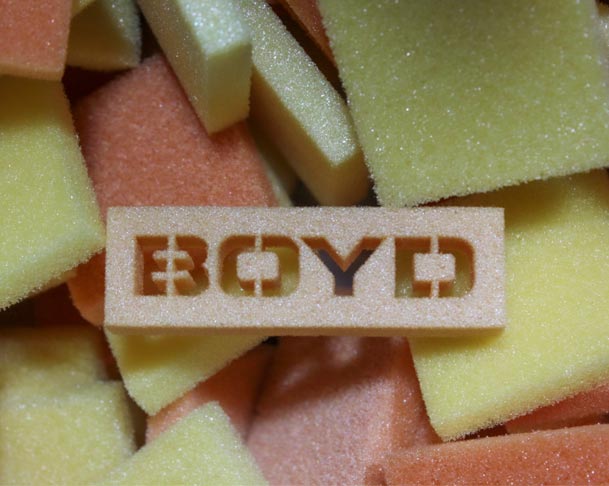
SOLIMIDE® foams are also flexible and much easier to convert into tight shapes and angles compared to silicone foams and fiberglass. Given the wide variety of vacuum tubes and process lines that required jackets, different diameters, lengths, and shapes would be necessary. SOLIMIDE® was easily converted into dozens of standard sizes and dimensions and was fabricable into custom shapes to match unique equipment.
Additionally, the lightweight and self-supporting construction of SOLIMIDE® foam made the new heating jackets significantly simpler to install and remove. Some semiconductor equipment required constant maintenance where jackets for underlying lines were replaced weekly. Because SOLIMIDE® could be manufactured into custom shapes to easily fit pipes and was much safer to work with, it significantly simplified equipment maintenance.
After extensive testing, prototypes for the new heating jackets featuring SOLIMIDE® foam were implemented on process lines. The new jacket construction exceeded thermal requirements (with some SOLIMIDE® formulations able to withstand continuous use up to 300°C) while solving all other project challenges. Using SOLIMIDE® in place of fiberglass and silicone also lowered the overall heat jacket weight and was cost competitive with the original materials.
Boyd’s SOLIMIDE® Results
Combining extensive material science expertise with our precision converting experience, Boyd was able to optimize safety, streamline installation, and simplify the fabrication process for the semiconductor equipment heating jackets. The new jackets are currently manufactured in several standard sizes along with a variety of custom diameters, lengths, and shapes and can be found on semiconductor testing equipment around the world. The success of the project has led to other opportunities with the customer to use SOLIMIDE® foam to optimize other components and processes.
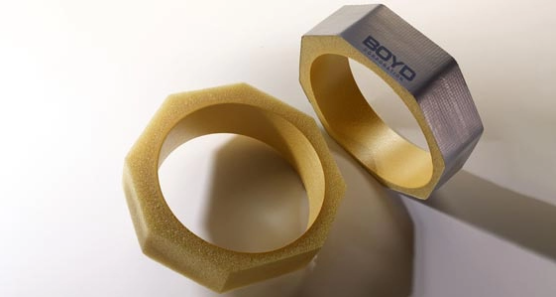
Have questions? We’re ready to help!