Key Factors that Determine the Cost of Fabricating Heat Exchangers
Manufacturing costs can be greatly impacted by demand, but this is not necessarily within the thermal or design engineers’ control. However, you can reduce costs by understanding how core and frame materials, interface tolerances, coatings, and other requirements can affect the cost of a heat exchanger. By involving your heat exchanger manufacturer early in the design process, you’ll be able to identify the manufacturing cost drivers and select the most cost effective design.
Core and Frame Materials
Core and frame material specifications can add significantly to the cost of a heat exchanger. The core, which may consist of tubes, fin, and/or sheet metal, can be manufactured using a variety of metals. The metals most commonly used in heat exchangers are copper, aluminum, and stainless steel. The cost of these metals has risen significantly over the past several years, making their percent of the total heat exchanger cost even greater. Since stainless steel is more expensive than copper or aluminum, it makes sense to opt for copper or aluminum unless your application requires stainless steel. Heat exchangers may also be manufactured using nickel, cupronickel, hastelloy®, inconel®, titanium, or other metals. However, these metals are not used as frequently due to their higher costs.
Usually the core’s materials are specified to ensure that fluid path metals are compatible with the coolant selected for the application. For example, stainless steel might be specified for use with deionized water, whereas cupronickel might be specified for use with saltwater. Heat exchanger core material may also be selected based on weight. Aluminum and titanium are preferential for military and aerospace applications since these metals are less dense.
Core costs can also vary based on the type of heat exchanger selected. Cost variations are due to the different amounts of materials required to make the specific heat exchanger as well as the amount of factory time required to manufacture the part. The least expensive type of heat exchanger to manufacture is a copper tube-fin heat exchanger. Stainless steel tube-fin heat exchangers are more expensive than copper because stainless steel is more expensive by weight, it requires more time to punch, and it must be welded. Like tube-fin heat exchangers, vacuum-brazed flat tube oil cooler heat exchangers are relatively easy to produce. Conversely, the most expensive type of heat exchanger to produce is a vacuum-brazed plate-fin heat exchanger.
Other heat exchanger specifications that can add cost are the materials and processes used to attach the heat exchanger’s frame to the core. Pop rivets are the least expensive option, followed by screws and then welding. Screws will provide a bit more strength than pop rivets. Flat tube heat exchanger frames are generally attached with rivets or welding. With welding, the result is an even stronger and more reliable part that is better able to handle shock and vibration. Welding is also preferable when space and weight are concerns, such as with plate-fin heat exchangers that are used in weight sensitive applications (e.g. airborne applications). Welding eliminates the need to use rivets, which can add weight. In addition, rivets may require a larger heat exchanger frame than welding does since the rivets need a wide section of metal to pass through and effectively hold the heat exchanger frame and core together. Due to additional factory time involved in the welding process, however, welding is more expensive than the other two methods.
Interface Tolerances for Installing Heat Exchangers
After core and frame materials, interface tolerance specifications for mounting and plumbing features are the next biggest cost drivers. For mounting features, the most cost effective approach is to design mounting features into individual sheet metal components. This will yield tolerances ranging from ± 0.03″ to ± 0.06″ ( ±0.076cm to ± 0.1.52 cm). If tighter tolerances are needed, the product will have to be machined during the final production stages, which will require additional machine time. The heat exchanger is also at risk of contamination from metal chips or coolant from machining, so extra care must be taken. This additional machining step can therefore add significantly to the cost.
Normal plumbing tolerances are ± 1/8″- ± 3/16″ (± 0.318 cm to ± 0.476 cm) for copper tube fin heat exchangers and ± 1/8″ (± 0.318 cm) for stainless steel and aluminum products. If tighter tolerances are required for plumbing, more expensive tooling and an increase in labor and inspection time will also be required. Off-the-shelf plumbing fittings are the least costly, however, they have looser tolerances. A beaded tube fitting that mates with a 3/8″ (0.953 cm) ID hose and is secured with a clamp does not require tight tolerances, so opting for this type of fitting may help to keep costs low. The most expensive fitting options are custom machined fittings.
Coatings for Heat Exchangers and Cold Plates
Finishes to Protect Thermal Management Solutions
Custom heat exchangers and cold plates are often coated for corrosion protection or for cosmetic purposes. Chemical conversion coating, anodization, e-coating, and painting are four coating options that will help to minimize corrosion and/or result in a more attractive component. One of the most widely used coating options is chemical conversion coating or chromate conversion coating, also known as “Chem Film” or alodine. Conversion coating helps to minimize surface oxidation and is often specified for military as well as commercial heat exchangers and cold plates. It also sometimes serves as a surface preparation for paint.Anodization
Another option that can be used to protect aluminum is anodization. Anodizing minimizes corrosion and abrasion by modifying the crystal structure close to the metal surface. It produces a harder part with even greater corrosion protection. However, it is more expensive than chemical conversion coating.
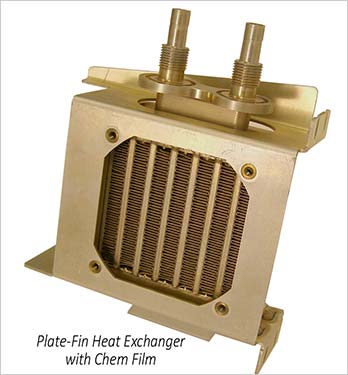
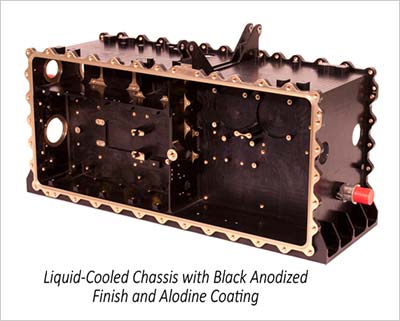
Electrodeposition or E-Coat
A third coating method that provides corrosion protection is called an e-coat, also known as electrodeposition or electrocoating. A DC charge is applied to a metal part immersed in a bath of oppositely charged paint particles. The paint particles are drawn to the metal part and paint is deposited on the part, forming an even, continuous film over the entire surface. Of the four types of coatings described here, it is the most expensive type of corrosion protection.
Paint
Heat exchangers and cold plates may also be painted for corrosion protection or cosmetic purposes. For example, copper heat exchangers are sometimes painted for aesthetics since uncoated copper may change color over time.
Although these are four of the most common coatings for heat exchangers and cold plates, there are a large number of coating options available to Original Equipment Manufacturers (OEMs).
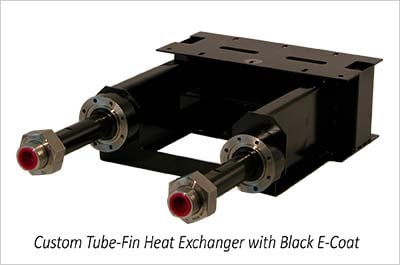
Heat Exchanger Coatings
Another significant cost driver is heat exchanger coatings for corrosion protection or for cosmetic purposes. Coating for corrosion protection is most common on aluminum heat exchangers, since aluminum corrodes more easily than other metals. There are several types of heat exchanger coatings to minimize corrosion: chemical conversion coating, anodization, e-coating, and painting.
One of the most widely used coating options is chemical conversion coating or chromate conversion coating, also known as “Chem Film”, that minimizes surface oxidation. Most government and commercial heat exchanger engineering specifications require that aluminum be chemical conversion coated (per military standard MIL-DTL-5541F, previously MIL-C-5541E).
In addition to Chem Film, another option that can be used to protect aluminum is anodization. Anodizing minimizes corrosion and abrasion by modifying the crystal structure close to the metal surface. It produces a harder part with even greater corrosion protection. However, it is not a common coating and it’s more expensive than chemical conversion coating.
A third coating method that provides corrosion protection is called an e-coat, also known as electrodeposition or electrocoating. A DC charge is applied to a metal part immersed in a bath of oppositely charged paint particles. The paint particles are drawn to the metal part and paint is deposited on the part, forming an even, continuous film over the entire surface. It is the most expensive type of heat exchanger corrosion protection.
Heat exchangers may also be coated with paint for corrosion protection or cosmetic purposes. For example, copper heat exchangers are sometimes painted for aesthetics since uncoated copper may change color over time. For epoxy paint applications, the cost per heat exchanger can range from $10-$200 per heat exchanger. The cost of the paint application will depend not only on the coating itself, but also on the amount of surface area to be coated. Weigh the value of the added corrosion resistance or improved appearance against cost to determine to opt for coating or painting. How long do you want your heat exchanger to last? Will your heat exchanger be visible and how important to your end users is heat exchanger appearance? The appearance of a heat exchanger on equipment in a hospital is likely to be more important than the appearance of a heat exchanger on equipment in a factory.
Heat Exchanger Design and Manufacturing Partnerships
Working with a heat exchanger manufacturer early in the design stage or being flexible on a build to print design will allow for the greatest amount of cost savings. Although the biggest cost driver in heat exchanger manufacturing is annual demand, there are many other factors over which thermal and/or component engineers have some control. Ensure that there is a reason for every specification, as every specification may drive up cost. When core and frame materials, tolerances, and coating specification are outlined, it’s important to determine whether they are necessary for the application or not. In addition, it’s important to realize that there are many alternatives in heat exchanger design as well as the manufacturing processes used, both of which impact cost.