Composite Material Science
Learn about advanced composite components and the resins and reinforcement materials that bring strength to these lightweight, rugged material science technologies.
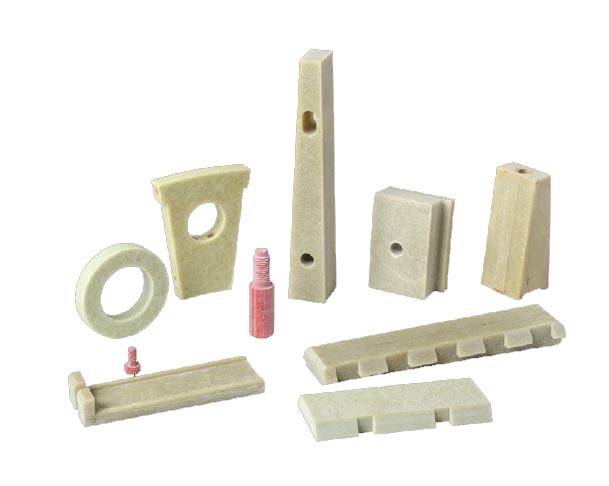
Composite Material Science at Boyd
A composite material is a blend of at least two non-mixable components that still have strong mutual adhesion. The resulting composite possesses improved properties compared to its components.
Exceptional mechanical, electrical, and thermal properties make composite materials an ideal lighter weight replacement for traditional metals and other alloys. Many composites exhibit:
- Low density
- High dielectric properties
- Considerable chemical and corrosion resistance
- High specific resistance and rigidity
- Fatigue or cycling resistance
- Excellent self-extinguishability
- Low combustion fume toxicity
Composite additives can also help adjust:
- Electrical or thermal conductivity
- The coefficient of thermal expansion (CTE)
- Energy absorption for shock or acoustics
Boyd’s material scientists leverage expertise and experience to develop and produce composite materials that meet demanding specifications. Boyd specializes in producing composites for a wide range of applications and industries such as transportation, electronics, energy, medical, and industrial technologies.
What are Composite Materials?
A composite material is the resulting blend of a binder, reinforcement, and additives that have improved properties over the parent materials.
Reinforcement acts as a framework that contributes mechanical strength to the composite. Composite reinforcements are classified as short, long or continuous fibers and add mechanical resistance and rigidity to the composite.
Binders act as the matrix that coheres the structure into a single component, transmits stresses to the reinforcement, and protects the reinforcement from the environment. Binders are generally a thermoplastic or a thermoset-based resin.
Additives and charges are generally included in composites to improve specific properties of the material, such as UV resistance, conductivity, fire resistance, etc.
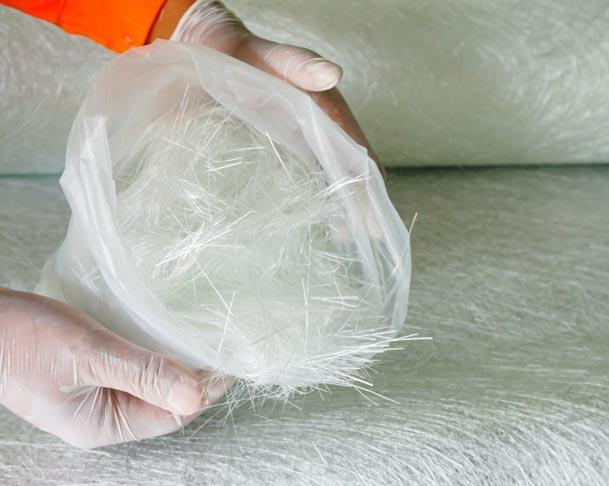
Stratified Composite Structures
Stratified Composite Structures are constructed from multiple thin layers of reinforcements impregnated with resin, called pleats, layered together to form a single component. Each pleat uses long-fiber reinforcements and is several tenths of a millimeter thick. These pleats are typically oriented in different directions from each other to produce desired mechanical properties.
Boyd offers a complete range of organic matrix composites (OMC) in either thermoset resin (TS) or thermoplastic resin (TP).
- Unsaturated polyester (UP)
- Vinyl ester (VE)
- Epoxy (EP)
- Phenolic (PF)
- Methacrylate (A)
- Polybismaleimides (BMI)
- Silicone (SI)
- Melamine (MF)
- Polyethylene (PE)
- Polypropylene (PP)
- Polyamide (PA)
- Polyimide (PI)
- Polybutylene terephthalate (PBT)
- Polyetherethercetone (PEEK)
- Poly(phenylene sulphide) (PPS)
- Poly(phenylene oxide) (PPO)
- Thread (Roving)
- Unidirectional web (UD)
- Woven
- Woven fabric
- Non-woven
- Glass mat, cut glass mat fibers or any other type of fibre with the same architecture
- Short fibers (0.1 to 1 mm)
- Long fibers (1 to 50 mm)
- Continuous fibers (>50 mm)
Manufacturing Capabilities
Boyd processes composite materials into semi-finished or finished products using several manufacturing methods, primarily machining, stamping, molding, and pultrusion. Common composite geometries include:
- Laminate panels
- Machined parts
- Tubes, cylinders and bars
- Round and threaded rods
- Custom pultruded profiles
- Custom molded parts
Have questions? We’re ready to help!